Single-laser grinding machines are revolutionizing the precision machining landscape, addressing the growing demand for efficiency and accuracy in manufacturing. Did you know that laser technology can enhance grinding precision by up to 30%? This article promises to equip you with valuable insights into the operation of single-laser grinding machines, highlighting their significant advantages, potential limitations, and practical tips for effective use across various industries.
Whether you’re a seasoned professional or just starting your journey in machining, understanding these advanced tools can elevate your work. You’ll discover how to leverage this innovative technology to improve your processes and outcomes. Ready to unlock the potential of single-laser grinding machines? Let’s get started!
What is a Single-Laser Grinding Machine?
A single-laser grinding machine employs a concentrated laser beam to grind materials with exceptional precision. Unlike traditional grinding methods that rely on physical contact between the grinding wheel and the workpiece, this innovative technology uses thermal energy from the laser to remove material. This results in finer surface finishes and improved control over the grinding process.
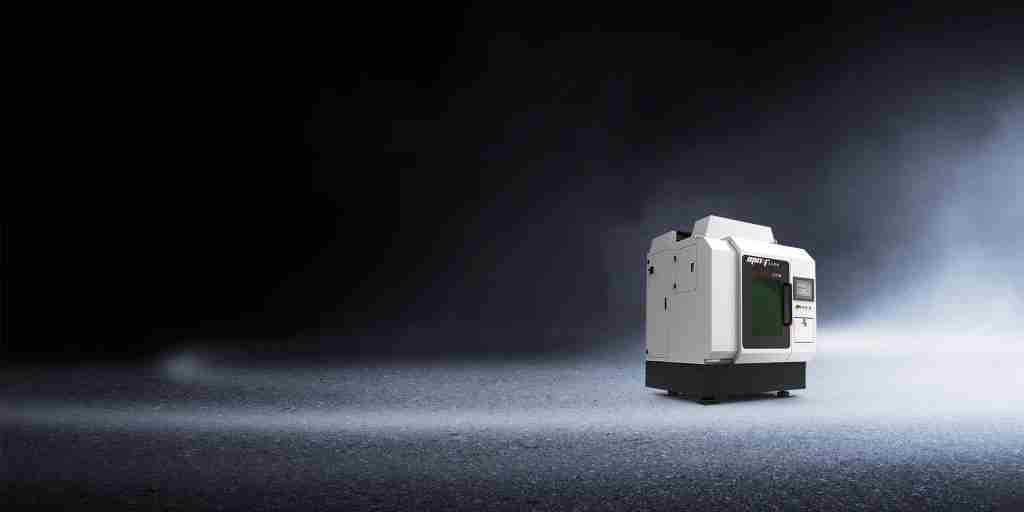
Read More: Best 10 Single-laser Grinding Machine Suppliers
How a Single-Laser Grinding Machine Works
A single-laser grinding machine employs advanced laser technology for precise material removal, making it particularly effective for delicate components. This innovative approach minimizes mechanical wear and reduces the risk of damage, enhancing overall operational efficiency.
Core Components
- Control System: A computer numerical control (CNC) system governs the movement of the laser head, adjusting parameters such as speed and intensity based on the specific material characteristics. This level of control enhances precision and enables the creation of complex shapes and finishes.
- Laser Source: The machine features a high-powered laser that generates a concentrated beam of light. This intense energy allows for accurate and efficient material removal.
- Optical System: Utilizing lenses and mirrors, the optical system focuses the laser beam onto the workpiece, ensuring maximum intensity at the contact point to optimize the grinding process.
- Material Interaction: When the focused laser beam interacts with the workpiece, it generates heat that raises the material to its melting or vaporization point. This non-contact method effectively removes material without mechanical abrasion, resulting in clean cuts and smooth finishes while significantly reducing wear on traditional grinding tools.
Advantages and Applications of Single-Laser Grinding Technology
Single-laser grinding technology is revolutionizing manufacturing processes across various sectors, offering distinct advantages that enhance productivity and precision. Here’s a concise overview of its key benefits and applications:
Key Advantages
- Unmatched Precision: Single-laser grinding machines deliver exceptional accuracy, achieving fine tolerances crucial for industries like aerospace, automotive, and electronics. This precision allows for intricate designs that traditional methods often cannot replicate.
- Superior Surface Quality: The laser grinding process produces smoother surface finishes, frequently eliminating the need for post-processing. This efficiency saves both time and costs.
- Material Versatility: These machines can effectively grind various materials, including metals, ceramics, and composites, making them suitable for a wide range of applications.
- Minimal Tool Wear: As a non-contact process, laser grinding reduces wear on tools, leading to lower operational costs and less frequent maintenance.
- Automation Compatibility: Single-laser grinding machines can seamlessly integrate into automated production lines, enhancing efficiency and ensuring consistent quality with minimal human intervention.
Common Applications
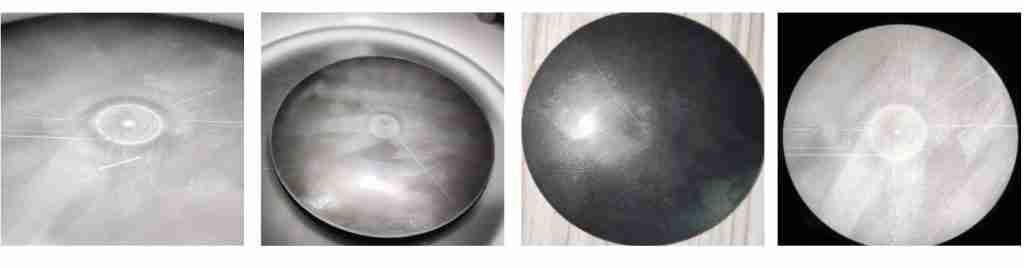
- Aerospace Engineering: Grinding turbine blades requires high precision, making single-laser technology ideal for this critical application.
- Automotive Manufacturing: The finishing of engine components benefits from the superior surface quality achieved through laser grinding, enhancing performance and durability.
- Electronics Production: Processing semiconductor wafers is another vital application where precision is paramount to maintain delicate features without damage.
Limitations to Consider
Despite their advantages, single-laser grinding machines come with certain limitations:
- High Initial Investment: The cost of acquiring these advanced machines can be substantial compared to traditional grinders, which may deter smaller businesses.
- Material Constraints: Some materials may not be suitable for laser grinding due to their thermal properties or structural integrity concerns.
- Specialized Skill Requirements: Operating these machines often necessitates specialized training in complex software and laser dynamics to optimize their capabilities effectively.
Single-laser grinding technology offers remarkable precision, surface quality, and versatility while reducing tool wear and supporting automation. However, potential users must weigh the initial investment, material compatibility, and necessary operator expertise to maximize the benefits in their manufacturing processes.
Cost-Benefit Analysis of Single-Laser Grinding Machines
Single-laser grinding machines deliver significant cost-effectiveness in modern manufacturing, particularly in precision machining. While the initial investment can be high, ranging from tens of thousands to millions of dollars depending on power and features, the long-term operational costs are generally lower due to increased production efficiency and reduced material waste, enhancing the return on investment (ROI).
Operationally, these machines typically consume less power and incur lower maintenance costs compared to traditional equipment. The automation features of laser technology decrease reliance on manual labor, further reducing labor costs. Additionally, single-laser grinding machines can cut various materials quickly, significantly boosting production rates. Research indicates that operating costs for laser cutting can range from $4 to $20 per hour, while traditional methods may exceed $30.
However, potential limitations include challenges in cutting certain reflective materials and the need for skilled operators. Therefore, businesses should thoroughly assess their production needs, market potential, and long-term benefits before investing. Overall, single-laser grinding machines offer an efficient, low-consumption, and precise solution that is a worthy investment for many manufacturers.
Laser Surface Treatment Equipment Costs
Understanding the cost landscape for laser surface treatment systems is crucial for businesses and professionals in 2025. Prices vary widely based on equipment type, specifications, and capabilities. This guide breaks down the pricing for different laser technologies, from handheld units to industrial-scale systems.
Handheld laser cleaning devices start at $3,000 for basic models, with advanced high-power units reaching $16,000. Industrial-scale laser cleaning systems begin at $20,000 for entry-level equipment, while high-end models exceed $50,000. Fiber laser cutting machines range from $10,000 for entry-level units to over $30,000 for industrial-grade equipment. CO2 laser systems offer the broadest price range, starting at $2,000 for basic models and reaching six figures for top-tier industrial lasers.
Key factors influencing equipment costs include power output, work area size, automation features, brand reputation, laser type, material compatibility, additional features, and software capabilities. When budgeting, consider expenses beyond the initial purchase, such as installation, operator training, maintenance, and consumables. While high-end machines have steeper upfront costs, they often deliver better long-term value through improved efficiency, versatility, and durability.
Laser Category | Entry-Level Price | High-End Price |
---|---|---|
Handheld Cleaning | $3,000 | $16,000 |
Industrial Cleaning | $20,000 | $50,000+ |
Fiber Cutting | $10,000 | $30,000+ |
CO2 Systems | $2,000 | $100,000+ |
Practical Tips for Using Single-Laser Grinding Machines
To optimize the use of single-laser grinding machines effectively, it’s crucial to adopt best practices that enhance performance and precision. Here are essential tips for maximizing efficiency:
Understand Material Properties
- Material Interaction: Different materials react differently to laser processing. Familiarize yourself with each material’s characteristics, such as heat sensitivity and melting points, to fine-tune settings like power levels and cutting speeds for optimal results.
Regular Maintenance
- Optical Components: Keep the optical components of your laser machine clean and properly aligned. Dirty or misaligned optics can severely impact cutting quality and efficiency. Regular cleaning ensures optimal beam focus.
- Routine Checks: Establish a maintenance schedule that includes checking gas pressure, coolant levels, and the condition of moving parts. This proactive approach can help identify potential issues early, preventing costly repairs.
Utilize Software Features
- Simulation Tools: Leverage advanced software for simulation and parameter optimization before actual machining. These tools allow you to visualize outcomes based on different settings, saving time and reducing material waste.
- Parameter Monitoring: Regularly assess machine performance and adjust parameters as needed. Tweak power settings according to material thickness and type to maintain desired cut quality without sacrificing efficiency.
Monitor Performance
- Quality Assurance: Continuously evaluate output quality during operations. Look for signs of wear or surface degradation that may require adjustments in speed or power settings to uphold high standards of precision.
- Feedback Mechanism: Create a system for operators to report issues or suggest improvements based on their experiences. This feedback can lead to enhanced operational practices and optimized machine settings over time.
By implementing these strategies, you can significantly enhance the efficiency and effectiveness of single-laser grinding machines, ensuring high-quality results while minimizing downtime and material waste.
Conclusion
A solid understanding of single-laser grinding machines is crucial for professionals in manufacturing sectors that demand high precision and quality. By leveraging this technology, industries can achieve superior results while minimizing costs associated with traditional machining methods. As advancements continue in laser technology, staying informed about new developments will be essential for maintaining competitive advantages in precision machining.
Disclaimer
This content is compiled by OPMT Laser based on publicly available information for reference only; mentions of third-party brands and products are for objective comparison and do not imply any commercial association or endorsement.