In today’s fast-paced manufacturing landscape, 5-axis machining has emerged as a game-changer, offering unparalleled precision and efficiency. You may have heard that this advanced technique comes with a hefty price tag and a steep learning curve, but that’s not the whole story.
Did you know that incorporating 5-axis CNC technology can reduce production time by up to 75%? This guide will help dispel common myths surrounding 5-axis machining and reveal its true potential.
You’ll discover how this innovative method can enhance your projects, from intricate designs to complex geometries. By the end, you’ll be equipped with essential insights into its capabilities and applications, motivating you to consider how 5-axis machining can elevate your work. Ready to unlock the power of this cutting-edge technology? Let’s get started!
What is 5 Axis Machining?
5-axis machining is a sophisticated manufacturing process that enables simultaneous movement of cutting tools along five distinct axes. This advanced capability significantly enhances precision and complexity in part fabrication compared to traditional 3-axis methods. By allowing tools to move along the linear X, Y, Z axes while also rotating around A and B axes, manufacturers can create intricate designs in a single setup without manual repositioning.
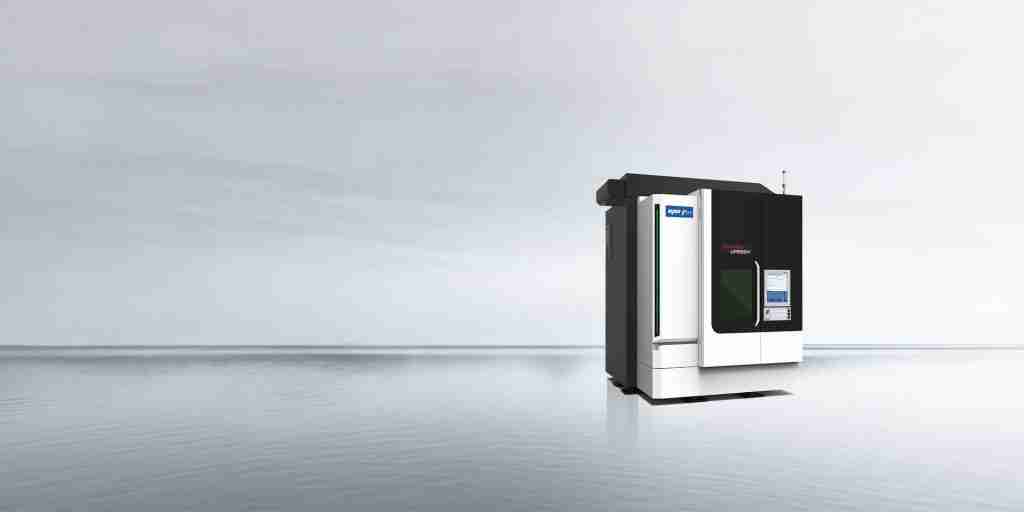
Understanding 5-Axis Machining
5-axis machining is an advanced manufacturing process that enables simultaneous movement of a cutting tool along five distinct axes. This capability significantly enhances precision and efficiency when machining complex geometries, making it essential in industries such as aerospace, automotive, and medical device manufacturing.
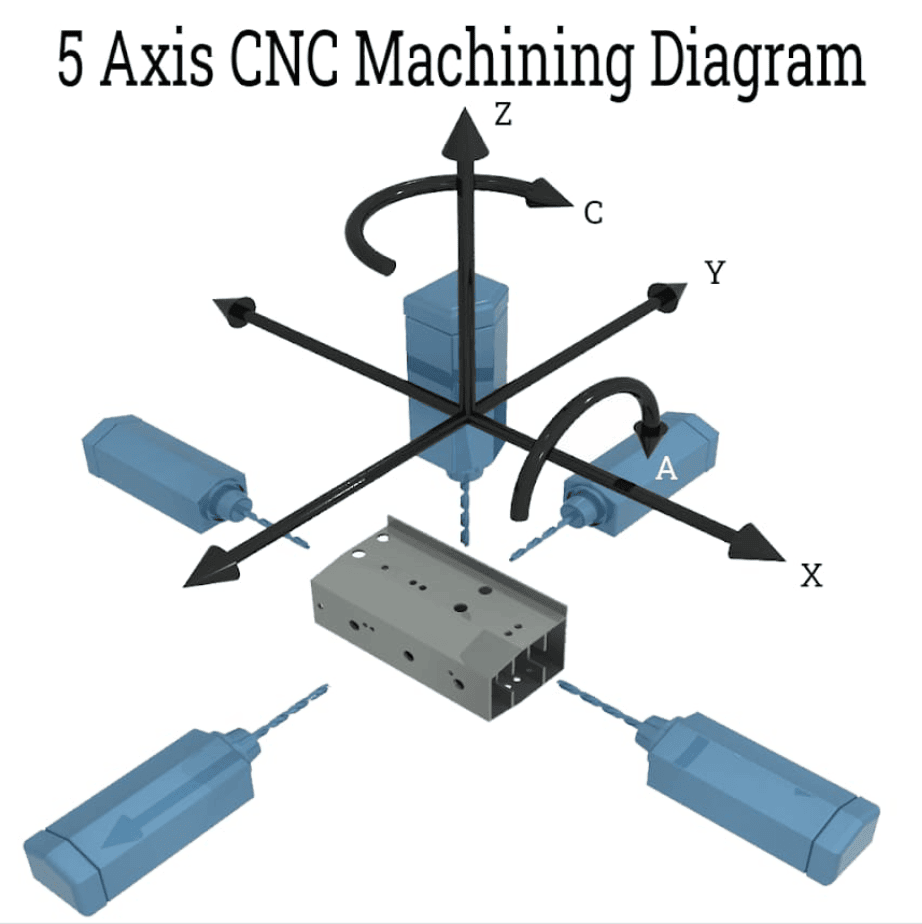
Axes of Movement
In a typical 5-axis machine setup, the axes are defined as follows:
- X-axis: Horizontal movement from left to right.
- Y-axis: Forward and backward movement.
- Z-axis: Vertical movement up and down.
- A-axis: Rotation around the X-axis.
- B-axis: Rotation around the Y-axis.
This multi-directional configuration allows cutting tools to approach workpieces from virtually any angle, facilitating the creation of intricate shapes that are often unattainable with traditional 3-axis machines.
Types of 5-Axis Machines
5-axis machining is an advanced manufacturing technique that significantly enhances the ability to produce complex geometries with exceptional precision. This method operates along five axes—X, Y, Z, A, and B—allowing for simultaneous movement and rotation, which is crucial for intricate machining tasks. Below are the primary types of 5-axis machine configurations:
Table/Table Configuration
- Description: In this setup, both tables perform rotary functions while keeping the workpiece stationary. This configuration allows for enhanced flexibility in machining, enabling rotation around multiple axes (A, B, C).
- Advantages:
- Facilitates complex part machining with superior undercut capabilities.
- Ideal for larger workpieces that require extensive manipulation.
Head/Table Configuration
- Description: This design features a rotating spindle head while the table securely holds the workpiece. The spindle’s ability to tilt and rotate provides access to various angles on the part.
- Advantages:
- Combines rotary and tilting motions for versatile machining options.
- Reduces tool interference by allowing precise positioning during operation.
Head/Head Configuration
- Description: In this setup, both spindle heads rotate while maintaining a stationary workpiece. This configuration is particularly suited for larger parts that require comprehensive machining from multiple angles.
- Advantages:
- Eliminates tool interference risks since the workpiece does not move.
- Ensures high rigidity and stability during complex operations.
Summary of Configurations
Configuration | Description | Advantages |
---|---|---|
Table/Table | Both tables perform rotary functions; workpiece remains stationary. | Flexibility, better undercuts, larger volumes. |
Head/Table | Spindle head rotates while the table holds the workpiece. | Precision positioning, reduced tool interference. |
Head/Head | Both spindle heads rotate; workpiece remains stationary. | High rigidity, suitable for large parts. |
These configurations greatly enhance flexibility in manufacturing processes across various industries by optimizing machining capabilities while minimizing setup times. Each type serves specific applications based on part complexity and size, making them integral to modern manufacturing strategies.
Key Advantages of 5-Axis Machining
5-axis machining has significantly transformed the manufacturing landscape by providing numerous benefits that enhance productivity, precision, and efficiency. Here are the primary advantages of this advanced machining technology:
1. Single Setup Machining
A standout benefit of 5-axis machining is its capacity to execute complex operations in a single setup. This capability minimizes errors linked to repositioning and maintains a consistent reference point throughout the machining process. As a result, manufacturers achieve higher accuracy and reduce the likelihood of dimensional discrepancies.
2. Increased Efficiency
5-axis machines facilitate simultaneous operations on multiple faces of a workpiece, which drastically cuts down processing times. This efficiency is especially advantageous in high-volume production settings, where optimized workflows lead to increased output.
3. Reduced Fixture Requirements
The ability to access workpieces from various angles often eliminates the necessity for complex fixtures. This simplification not only reduces costs but also enhances the handling of intricate designs, providing greater flexibility in manufacturing processes.
4. Improved Surface Finish
With optimized tool paths that reduce vibration, 5-axis machining yields superior surface finishes. This enhancement decreases the need for post-processing operations, saving both time and resources while improving product quality.
5. Versatility in Manufacturing Complex Parts
5-axis machines excel at producing intricate designs, such as turbine blades and medical implants. Their ability to navigate complex geometries encourages innovation across various sectors, enabling manufacturers to meet stringent design specifications effectively.
6. Higher Precision and Accuracy
The advanced capabilities of 5-axis machines contribute to greater precision in part manufacturing. By minimizing human intervention and ensuring consistent tool engagement, these machines achieve tighter tolerances essential for high-quality production.
7. Enhanced Tool Life
By optimizing cutting conditions, 5-axis machining significantly reduces tool wear. Tools engage with materials at optimal angles, extending their lifespan and lowering overall costs related to tool replacement.
8. Better Material Utilization
The multidirectional capabilities of 5-axis machining promote more efficient use of raw materials, reducing waste and aligning with sustainable manufacturing practices that contribute to cost savings.
9. Improved Safety
A reduction in manual handling decreases accident risks during operations. Many modern 5-axis machines are equipped with safety features like collision detection systems, further enhancing operator safety.
Adopting 5-axis machining presents numerous advantages that enhance productivity, accuracy, and efficiency while reducing costs and improving safety across manufacturing processes. These benefits position it as an increasingly popular choice among industries seeking innovation in precision engineering.
Applications of 5-Axis Machining
5-axis machining is a sophisticated manufacturing process that allows for simultaneous movement of the cutting tool and workpiece along five axes. This capability enables the creation of intricate geometries and complex designs with exceptional precision. The applications of 5-axis machining are extensive, impacting key industries such as aerospace, medical devices, automotive, and energy.
Aerospace Industry Applications
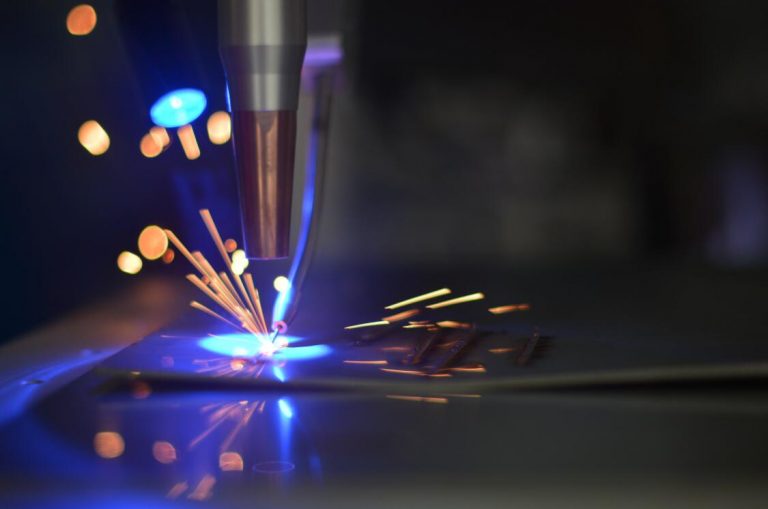
Turbine Blades
In aerospace manufacturing, 5-axis machining is essential for crafting turbine blades that require intricate geometries and tight tolerances. This technology enhances engine performance by optimizing airfoil shapes, which minimizes drag and maximizes fuel efficiency.
Structural Components
5-axis machining allows for the production of lightweight yet robust airframe parts that meet stringent safety standards. The precision achieved ensures these components can endure the extreme conditions encountered in flight.
Engine Parts
Complex shapes necessary for various engine components, such as casings and mounts, are efficiently produced using 5-axis techniques. This level of precision is crucial for ensuring the reliability and efficiency of aerospace engines.
Medical Device Manufacturing
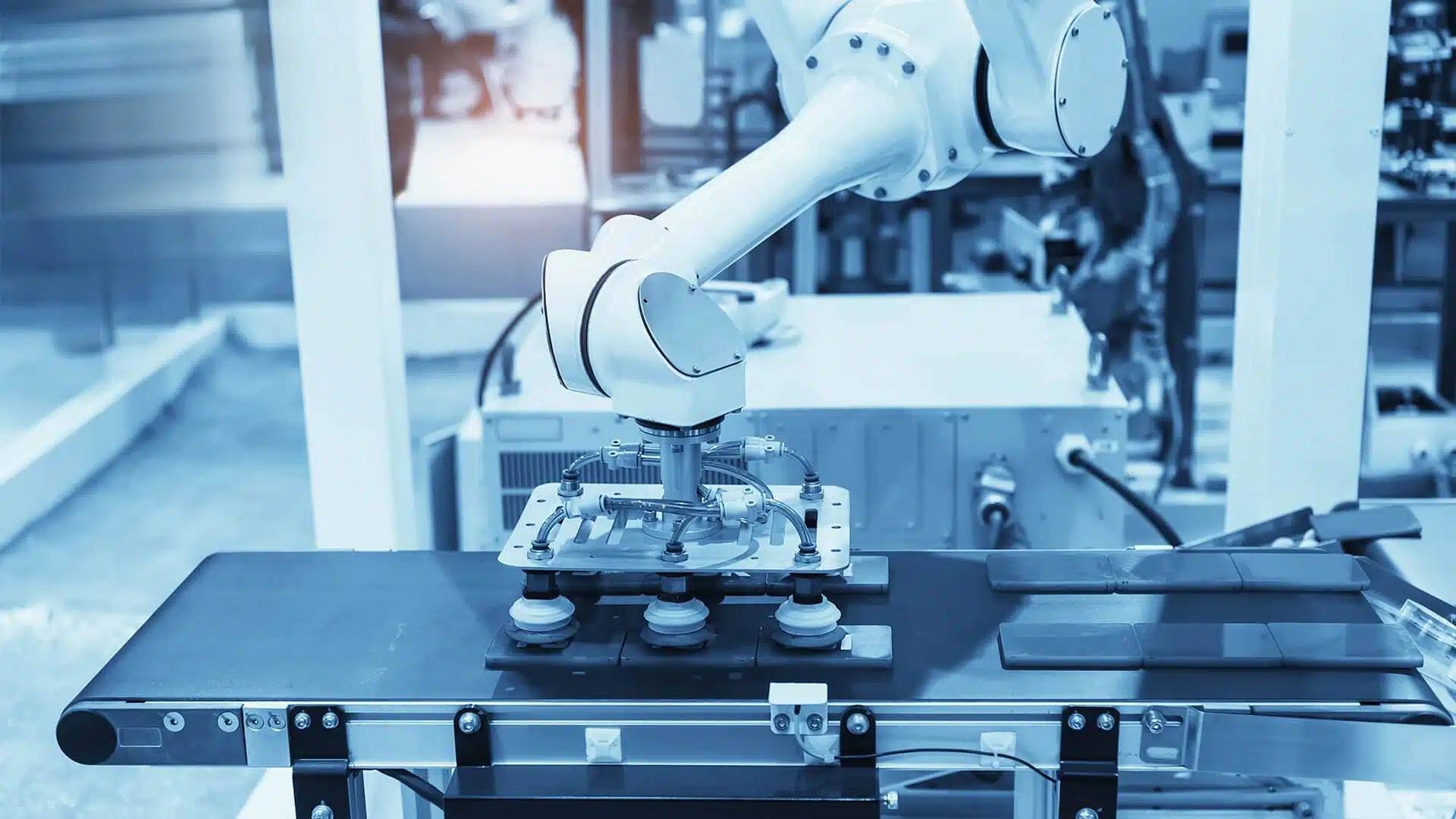
Custom Implants
The medical sector utilizes 5-axis machining to create orthopedic implants and dental prosthetics tailored to individual patient anatomies. This customization leads to improved surgical outcomes and enhanced patient comfort.
Surgical Instruments
High precision in the manufacturing of surgical tools is paramount; 5-axis machining enables the production of intricate designs that enhance both performance and safety during medical procedures.
Diagnostic Equipment Components
Advanced 5-axis techniques ensure high accuracy in the manufacturing of components for imaging equipment and diagnostic tools, meeting rigorous health standards essential for effective patient care.
Automotive Industry Innovations
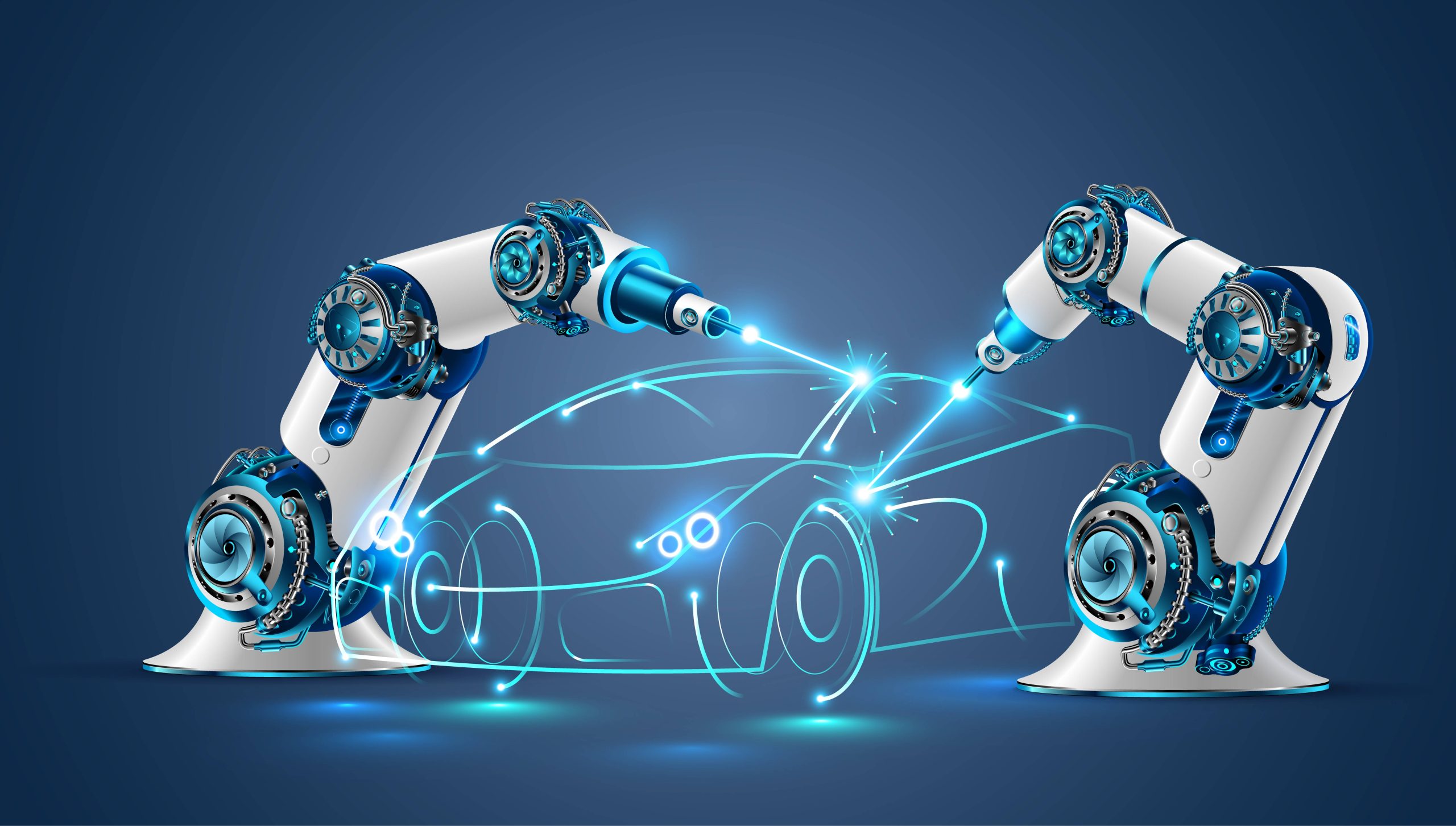
Complex Parts Production
Automotive manufacturers leverage 5-axis machining to produce intricate chassis components and engine blocks that enhance overall vehicle performance and safety.
Rapid Prototyping Capabilities
This technology facilitates quick design iterations, allowing manufacturers to efficiently test and refine components before full-scale production, thereby accelerating the development cycle of new vehicles.
Lightweight Component Development
By enabling the creation of complex shapes, 5-axis machining plays a vital role in developing lightweight parts that improve fuel efficiency without compromising strength.
Energy Sector Advancements
Power Generation Parts Creation
High-precision components essential for generators and turbines are manufactured using advanced 5-axis techniques. This ensures efficiency in energy generation processes while maintaining product quality.
Renewable Energy Components Production
In renewable energy applications like wind turbines and solar panels, precise manufacturing through 5-axis machining is critical for performance under demanding conditions.
Oil & Gas Equipment Manufacturing
Complex components such as drill bits are produced with high precision to withstand extreme environments, ensuring reliability in energy production applications.
5-axis machining provides unparalleled capabilities across various industries by enabling the production of complex, high-precision components essential for modern manufacturing. Its applications not only enhance product quality but also improve efficiency in production processes, making it a crucial technology in today’s competitive landscape.
Conclusion
5-axis CNC machining represents a transformative advancement in the manufacturing landscape, offering unparalleled precision, efficiency, and versatility. By enabling simultaneous movement across five axes, this technology allows for the creation of intricate geometries and complex parts that traditional 3-axis methods cannot achieve.
Disclaimer
This content is compiled by OPMT Laser based on publicly available information for reference only; mentions of third-party brands and products are for objective comparison and do not imply any commercial association or endorsement.