Five-axis CNC (Computer Numerical Control) machine tools represent a significant leap forward in precision machining technology, addressing the challenges of complex geometry fabrication. With the ability to move the cutting tool or workpiece across five axes simultaneously, these machines enhance accuracy and efficiency, making them essential for modern manufacturing. Did you know that five-axis machining can reduce setup time by up to 75%?
At OPMT Laser, we understand your need for innovative solutions that streamline production and elevate quality. This article will guide you through the structural principles of five-axis CNC machine tools, exploring their unique capabilities and advantages. You’ll discover how these advanced systems can transform your machining processes and why they are becoming indispensable in today’s competitive landscape. Get ready to unlock new possibilities in precision machining!
Understanding the Axes of a Five-Axis CNC Machine
Five-axis CNC machining is a revolutionary approach in manufacturing that enhances precision and versatility. This technology utilizes five distinct axes of movement, allowing for intricate part fabrication with unparalleled accuracy. The three linear axes—X, Y, and Z—work in conjunction with two rotational axes, A and B, to enable the cutting tool to approach the workpiece from virtually any angle.

Linear Axes Explained
- X-axis: This axis allows movement from left to right, facilitating horizontal traversing across the workpiece.
- Y-axis: Movement along this axis occurs from front to back, providing depth and enabling precision cuts that require forward and backward motion.
- Z-axis: The vertical movement achieved through the Z-axis allows the tool to engage with the workpiece by moving up and down.
These linear movements are essential for achieving detailed machining operations, ensuring that components are crafted with high precision.
Rotational Axes Overview
- A-axis: This axis enables rotation around the X-axis, allowing for tilting of the cutting tool to access complex angles.
- B-axis: Similar to the A-axis, this axis rotates around the Y-axis, further enhancing the machine’s ability to handle intricate designs.
The integration of these rotational movements significantly expands machining capabilities, making it possible to create complex geometries that would be difficult or impossible with traditional three-axis machines.
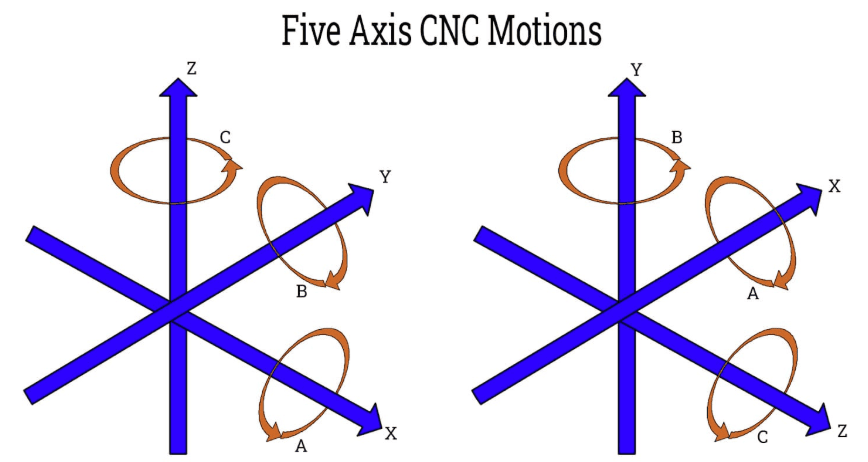
Benefits of Five-Axis CNC Machining
Five-axis CNC machines offer numerous advantages over their three-axis counterparts:
- Higher Precision: The ability to machine parts in a single setup minimizes errors associated with multiple repositioning, resulting in superior accuracy.
- Complex Geometries: These machines can produce intricate designs that meet stringent industry standards without requiring extensive manual intervention.
- Reduced Setup Time: By eliminating the need for multiple setups, five-axis machining streamlines production processes, leading to faster turnaround times.
- Improved Surface Finish: Continuous motion across all axes allows for better tool engagement with the workpiece, yielding smoother finishes and reducing tool wear.
For manufacturers looking to enhance their production capabilities, OPMT Laser offers innovative CNC systems tailored for five-axis machining. Explore our 5-Axis CNC Machining Center for advanced solutions.
Applications Across Industries
Five-axis CNC machining is widely utilized in various sectors due to its versatility and precision. Common applications include:
- Medical Devices: Manufacturing components such as surgical instruments and implants that require high dimensional tolerances.
- Automotive Parts: Creating complex engine components and molds that enhance performance and efficiency.
- Consumer Electronics: Producing detailed parts for devices that demand high precision and aesthetic quality.
By integrating five-axis CNC technology into manufacturing workflows, companies can achieve higher productivity levels while maintaining quality standards. OPMT Laser is committed to providing cutting-edge solutions in five-axis CNC machining to meet these evolving needs.
For more information on our innovative products, visit our Laser Processing Solutions page.
Basic Structure Components of CNC Machines
Understanding the basic structure components of CNC machines is essential for maximizing their performance and efficiency. These components work together to create a robust system that ensures precision in machining processes.
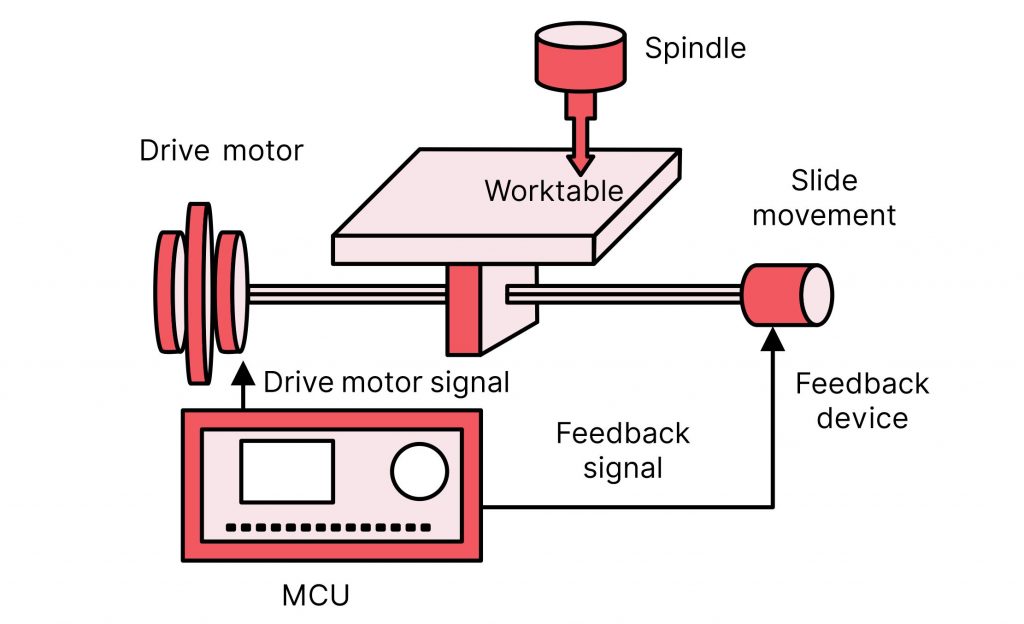
Machine Frame
The machine frame is the backbone of any CNC machine, providing a rigid structure that supports all other components. It is designed to withstand operational stresses and vibrations, ensuring stability during machining. Typically made from high-quality materials like cast iron or welded steel, the frame’s durability directly influences the machine’s overall performance. A well-constructed frame minimizes deflection and maintains alignment, which is crucial for achieving high precision in cutting operations. Have you ever wondered how a sturdy frame can impact your machining accuracy? It’s simple: a stable foundation leads to better results.
Worktable
The worktable serves as the mounting surface for the workpiece, playing a pivotal role in the machining process. In advanced five-axis machines, this table can tilt and rotate, allowing operators to access various sides of the workpiece without manual repositioning. This feature not only enhances efficiency but also improves precision by reducing setup time. For instance, when using a machine like the WJC532V Water Guided Laser Five-Axis Machining Center, operators can achieve complex geometries with ease. The design often includes T-slots or clamps to secure the workpiece firmly, ensuring it remains in place throughout the operation.
Spindle
The spindle is a critical component that holds and drives the cutting tool. In five-axis machines, spindles are engineered for multi-directional rotation, enabling intricate cutting operations that require flexibility and precision. The performance of the spindle affects not only the speed and torque applied to the tool but also the quality of the finished product. For example, spindles in machines like the LP550V are designed for high-speed applications, allowing for efficient material removal while maintaining surface quality.
Control System
An advanced control system interprets CAD/CAM data and translates it into precise movements of the machine’s axes. This system is essential for managing simultaneous motion across multiple axes during machining, ensuring every movement is executed with accuracy. A well-designed control system enhances productivity by optimizing machining paths and reducing cycle times. Have you considered how much time could be saved with an efficient control system? By integrating cutting-edge technology, OPMT Laser ensures that its CNC systems deliver unmatched precision and reliability.
The basic structure components—machine frame, worktable, spindle, and control system—are integral to the functionality of CNC machines. Understanding these elements allows operators to appreciate their importance in achieving high-quality results in manufacturing processes. OPMT Laser is dedicated to providing innovative CNC solutions that incorporate these essential components for optimal performance. Explore our range of products to find solutions tailored to your specific machining needs.
For more information on our innovative solutions, check out our product offerings such as Micro3D L530V and LightGrind LT20.
Advantages of Five-Axis Machining
Five-axis machining represents a significant advancement in CNC technology, offering numerous benefits that enhance precision and efficiency in manufacturing. This innovative approach allows for complex part production with minimal setups, making it a game-changer for industries requiring high precision.
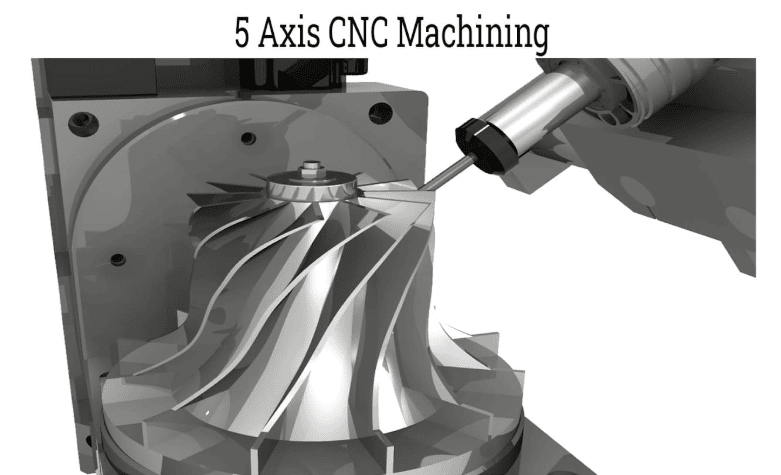
Single Setup Efficiency
One of the most notable advantages of five-axis machining is its ability to complete all operations in a single setup. Unlike traditional three-axis machines that often necessitate multiple repositioning steps, five-axis systems streamline the process. This efficiency not only reduces production time but also minimizes the risk of errors associated with repositioning. By maintaining the workpiece in a fixed position, manufacturers can achieve faster turnaround times and lower operational costs, which is essential for companies like OPMT Laser that focus on innovative CNC systems.
Enhanced Accuracy and Surface Finish
Five-axis machining significantly improves dimensional accuracy and surface finishes. The continuous engagement of tools allows for optimal cutting conditions, resulting in parts with superior quality. This enhancement reduces the need for secondary finishing operations, saving both time and resources. For instance, manufacturers can expect less scrap material and rework, leading to increased profitability.
Capability for Complex Geometries
The added axes in five-axis machines enable the creation of intricate designs that are often required in high-precision industries such as medical device manufacturing. This capability allows manufacturers to explore innovative designs that would be challenging to produce with traditional methods. The flexibility offered by five-axis machining empowers businesses to push the boundaries of design while maintaining high standards of quality.
Increased Efficiency and Productivity
The ability to machine multiple sides of a workpiece in one cycle enhances productivity and reduces lead times. By minimizing downtime associated with setup changes, five-axis machines allow manufacturers to maximize output without sacrificing quality. This efficiency is critical for businesses looking to meet tight deadlines while maintaining competitive pricing.
Reduced Material Waste
Five-axis machining optimizes material usage by allowing for more efficient nesting of parts within raw materials. This capability not only minimizes scrap but also aligns with sustainable manufacturing practices. Companies can significantly reduce their environmental impact while improving their bottom line through better resource management.
Improved Tool Life
The design of five-axis machines promotes even tool wear by allowing tools to approach workpieces from various angles. This feature extends the lifespan of cutting tools, reducing the frequency of tool changes and associated costs. For manufacturers, this translates into lower operational expenses and improved productivity.
Enhanced Safety for Operators
With advanced features such as collision detection systems, five-axis machines inherently reduce the need for manual intervention, minimizing risks associated with operator error. This focus on safety not only protects workers but also ensures consistent production quality.
By leveraging these advantages, OPMT Laser positions itself as a leader in precision manufacturing solutions. The integration of five-axis machining technology not only enhances operational efficiency but also meets the evolving demands of modern industries. For more information on OPMT Laser’s innovative CNC systems, explore our product offerings such as Micro3D L530V and WJC532V Water Guided Laser Five-Axis Machining Center.
Kinematic Solutions in CNC Machining
Understanding kinematic solutions is essential for optimizing the performance of CNC machines, particularly in five-axis configurations. These solutions dictate how machines move and position tools relative to the workpiece, significantly impacting machining precision and efficiency.
Head/Head Configuration
In a head/head configuration, rotary axes are integrated into the spindle head, allowing it to navigate around a fixed worktable. This setup is particularly beneficial for larger components, providing stability and support during machining operations. However, it may limit the range of motion needed for intricate designs.
Key benefits include:
- Enhanced Stability: The design minimizes vibrations, ensuring that larger parts remain securely held during machining.
- Potential Limitations: While effective for sizable components, this configuration may require additional setups for complex geometries.
For those seeking reliable solutions, OPMT Laser offers advanced CNC systems tailored to meet diverse manufacturing needs.
Table-Based Configuration
In contrast, a table-based configuration incorporates rotational axes within the worktable itself. This design enhances flexibility in part positioning and allows for tool access from multiple angles without needing to reposition the workpiece.
Advantages of this configuration include:
- Versatility: It enables complex machining tasks with fewer setups, improving overall efficiency.
- Improved Accessibility: Operators can easily access all sides of the workpiece, enhancing precision and reducing cycle times.
For more information on innovative CNC systems that leverage these configurations, explore OPMT Laser’s offerings such as the 563V Vertical 5-Axis Machining Center.
Both configurations—head/head and table-based—offer unique advantages and challenges that affect their suitability for different machining applications. By understanding these kinematic principles, manufacturers can make informed decisions that enhance productivity and quality in their operations. OPMT Laser is committed to providing cutting-edge solutions that optimize CNC machining processes for various industries.
Conclusion
The structural principles of five-axis CNC machine tools are essential for modern manufacturing, enabling the production of intricate components with unmatched precision. With the ability to manipulate multiple axes simultaneously, these machines not only boost operational efficiency but also inspire innovative designs. Did you know that utilizing five-axis machining can reduce production time by up to 30%?
By partnering with OPMT Laser, you can harness this technology to elevate your manufacturing capabilities, ensuring you stay competitive in an ever-evolving market. Explore our range of advanced products, such as the 563V Vertical 5-Axis Machining Center and the Light 5X-60V, to discover how we can help you achieve superior quality and efficiency. Are you ready to transform your manufacturing processes?
Disclaimer
This content is compiled by OPMT Laser based on publicly available information for reference only; mentions of third-party brands and products are for objective comparison and do not imply any commercial association or endorsement.