In today’s fast-paced manufacturing world, where efficiency, sustainability, and personalization reign supreme, laser texture processing has emerged as a game-changing innovation. This cutting-edge technology is reshaping the landscape of mold and product design, offering unparalleled advantages over traditional methods.
The Progression of Surface Modification Techniques
Surface modification has undergone significant advancements, transforming manufacturing processes across industries. This evolution has led to more precise, efficient, and environmentally friendly methods of altering material surfaces.
Traditional Chemical Approaches
In the past, chemical etching was the primary method for texturing molds and other surfaces. This process involved:
- Using corrosive substances to create patterns
- Complex and time-intensive operations
- Generating chemical waste, raising environmental concerns
- Offering limited design flexibility
- Producing inconsistent results across production runs
Laser Technology: A Leap Forward
The introduction of laser texture processing in recent years has addressed many limitations of chemical etching:
Feature | Chemical Etching | Laser Texturing |
---|---|---|
Precision | Limited | Micrometer accuracy |
Consistency | Variable | Highly uniform |
Environmental Impact | High | Minimal |
Design Flexibility | Restricted | Extensive |
Processing Time | Long | Significantly reduced |
Laser texturing has revolutionized surface modification by:
- Achieving intricate patterns with exceptional accuracy
- Ensuring uniform results across large production volumes
- Eliminating chemical waste, reducing environmental impact
- Expanding the range of possible textures and designs
- Dramatically improving processing efficiency
Applications and Benefits
Modern surface texturing techniques find applications in various industries:
- Automotive: Enhancing aerodynamics and aesthetics
- Medical: Improving implant integration and reducing bacterial adhesion
- Electronics: Optimizing heat dissipation and component performance
- Aerospace: Increasing fuel efficiency through drag reduction
These advancements have led to:
- Improved product functionality
- Enhanced manufacturing efficiency
- Reduced environmental impact
- Expanded design possibilities
As of 2025, ongoing research continues to refine laser texturing techniques, promising even greater precision and versatility in surface modification.
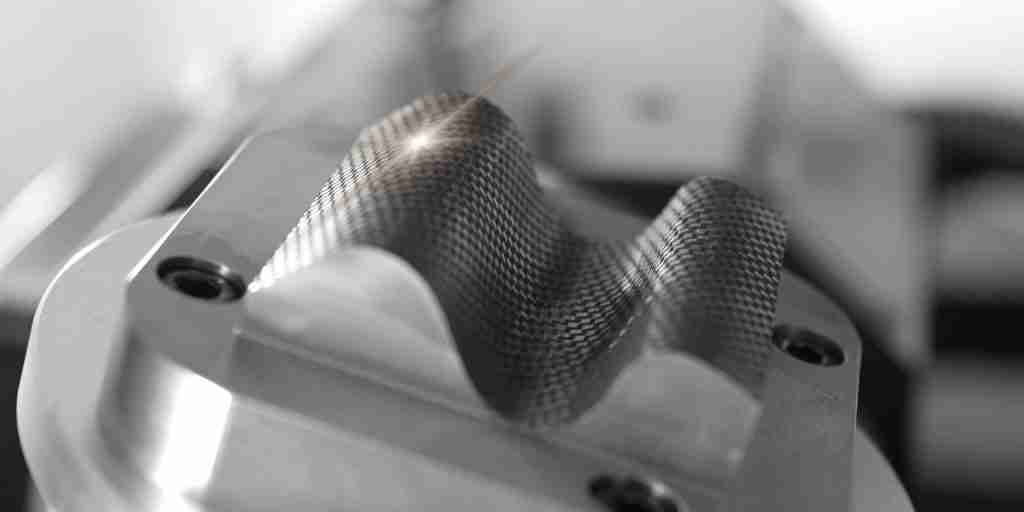
The Power of Laser Texture Processing: Revolutionizing Surface Engineering
Laser texture processing is transforming surface engineering by enabling precise, efficient, and eco-friendly material modification. This cutting-edge technique harnesses focused light beams to etch intricate patterns directly onto material surfaces, offering unparalleled control and versatility.
Precision Meets Efficiency
How does laser texture processing achieve such remarkable results? By utilizing high-powered lasers, manufacturers can create complex textures with micrometer-level accuracy. This process dramatically reduces production cycles compared to traditional methods. The laser’s precision allows for:
- Consistent texture quality across different molds and facilities
- Intricate patterns on complex 3D surfaces
- Rapid prototyping and design iteration
Eco-Friendly Manufacturing
Why is laser texturing considered environmentally friendly? Unlike conventional texturing methods, laser processing eliminates the need for harsh chemicals. This approach:
- Reduces workplace hazards
- Minimizes environmental impact
- Aligns with sustainable manufacturing practices
Unleashing Design Freedom
How does laser texturing empower designers? The technology’s versatility allows for:
- Creation of unique surface finishes
- Enhanced product aesthetics
- Customization of functional properties
Designers can now push the boundaries of product aesthetics and functionality, exploring new possibilities in surface engineering.
Functionality Meets Aesthetics
What functional benefits does laser texturing offer? Beyond visual appeal, laser-textured surfaces can enhance product performance:
Functional Benefit | Application Example |
---|---|
Anti-slip properties | Improved grip on tools |
Fingerprint resistance | Sleek electronic device finishes |
Glare reduction | Enhanced display visibility |
These improvements contribute to both product usability and consumer satisfaction.
Applications Across Industries
Where is laser texture processing making an impact? Its versatility has led to adoption in various sectors:
- Automotive: Enhancing interior trim and lighting components
- Consumer Electronics: Creating unique textures for smartphones and laptops
- Medical Devices: Improving grip and functionality of surgical instruments
- Packaging: Developing distinctive finishes for luxury goods
The Future of Surface Engineering
What’s next for laser texture processing? As the technology continues to evolve, we can expect:
- Increased precision and speed
- Integration with other manufacturing processes
- Expansion into new industries and applications
Laser texture processing is poised to play a crucial role in advancing surface engineering techniques, driving innovation across multiple sectors.
OPMT’s 5-Axis Laser Texture Processing Solution
Light 5X 60V Vertical 5-Axis Laser Machining Center
– Tool Carving
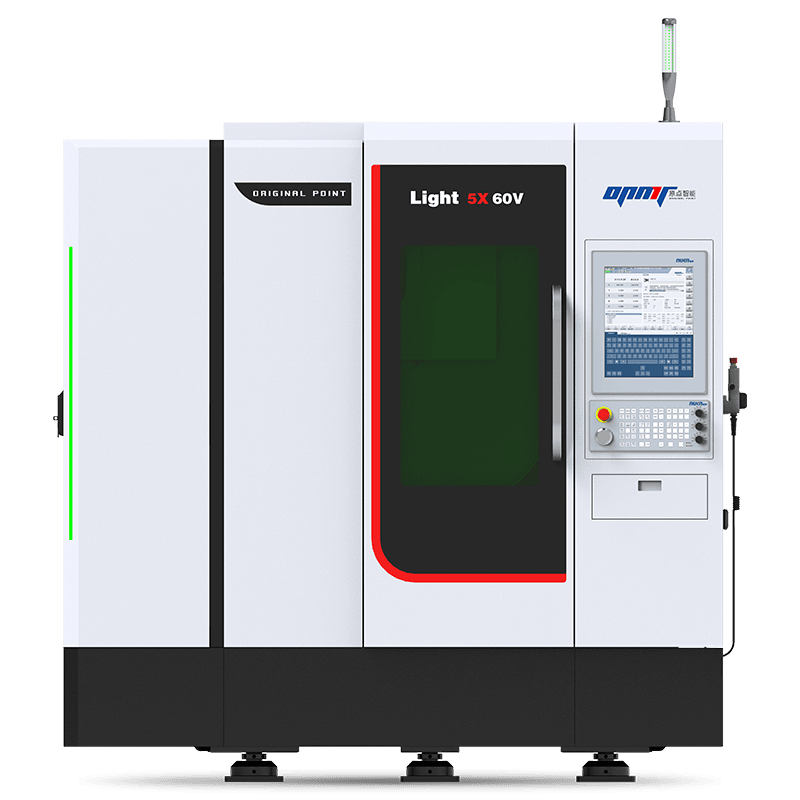
OPMT’s advanced 5-axis laser texture processing solution is revolutionizing the manufacturing landscape by delivering exceptional precision and efficiency. This innovative system enables manufacturers to create intricate surface textures and functional patterns across a diverse range of materials, including metals, ceramics, and plastics. With its ability to perform complex 3D surface texturing, OPMT’s technology meets the growing demand for high-quality, customized products in various industries.
Key Features and Advantages
The 5-axis laser texturing technology offers several compelling benefits:
- Versatile Texturing Capabilities: Capable of producing both aesthetic and functional textures, this solution caters to a wide array of applications, from automotive components to consumer electronics.
- Multi-Dimensional Processing: The unique 5-axis configuration allows for intricate designs on complex geometries, enhancing product innovation and design flexibility.
- Non-Contact Processing: This method ensures minimal material distortion and maintains the integrity of delicate components, which is crucial for high-precision manufacturing.
- Energy Efficiency: The optimized laser technology significantly reduces energy consumption, contributing to lower operational costs and a smaller environmental footprint.
Technological Highlights
OPMT’s system integrates cutting-edge features that enhance its performance:
- Flexible Laser Options: Users can select between nanosecond and femtosecond lasers tailored to specific precision requirements, ensuring optimal results for various applications.
- Advanced Scanning Optics: Multiple lens options (F100, F163, F255) provide versatility in achieving different texturing effects and accommodating complex mold cavities.
- Proprietary Software: OPMT’s in-house developed software streamlines the entire process—from laser marking to texture program generation—ensuring efficient workflow management and collision detection.
The Future of Manufacturing
As industries increasingly prioritize customization and quality, OPMT’s laser texture processing technology is set to play a pivotal role in shaping the future of manufacturing. By leveraging this advanced solution, manufacturers can elevate their product offerings to new levels of sophistication and functionality. With ongoing innovations in laser technology, OPMT remains committed to providing cutting-edge solutions that meet the evolving needs of the market.
Conclusion
Laser texture processing represents a significant leap forward in manufacturing technology. Its ability to combine precision, efficiency, and design freedom is transforming how we approach surface texturing across multiple industries. As companies like OPMT continue to push the boundaries of what’s possible with laser technology, we can expect to see even more innovative applications and advancements in the years to come.
For manufacturers looking to stay ahead of the curve and deliver products that stand out in today’s competitive market, embracing laser texture processing is not just an option – it’s a strategic imperative.
Disclaimer
This content is compiled by OPMT Laser based on publicly available information for reference only; mentions of third-party brands and products are for objective comparison and do not imply any commercial association or endorsement.