In an era where manufacturers face relentless pressure to deliver faster cycle times and sub-5µm precision, the OPMT 563V Vertical 5-Axis Machining Center emerges as a game-changer. Designed for tool steel and high-temperature alloys like Inconel 718, this machine integrates three groundbreaking innovations: 48m/min rapid feed rates, a 20,000rpm German-engineered spindle, and a 30-tool umbrella automatic tool changer (ATC). Validated by 2025 TÜV Rheinland certifications (Report #CT-563V-48), the 563V slashes production costs while achieving 99.7% first-pass yields in critical sectors like medical implants and automotive components.
48m/min Rapid Feed – Eliminating Non-Productive Time
Linear Motors vs. Ball Screws: A 2025 Efficiency Benchmark
Traditional CNC machines relying on ball screws struggle with acceleration limits, often capping feed rates at 30m/min. The OPMT 563V disrupts this paradigm with HIWIN 40/16mm ball screws paired with SCHNEEBERGER 45 roller guide rails, enabling X/Y/Z-axis acceleration of 3.2 m/s²—three times faster than conventional systems.

Efficiency Gains in Practice:
- Titanium Spinal Rods: Cycle times reduced from 5.8 to 4.2 hours, saving €18.50 per part in energy costs.
- Automotive Gears: Annual output surged from 10,800 to 14,400 units, leveraging uninterrupted 48m/min traversal.
Case Study – Medical OEM (Munich, Germany):
A leading implant manufacturer reduced cobalt-chrome spinal rod machining costs by €22,000 annually using the 563V. The machine’s quadruple Y-axis guide rails minimized vibration to <2µm during high-speed operations, ensuring Ra 0.4µm surface finishes critical for FDA compliance.
20,000rpm Spindle – Mastering High-Temp Alloys
Torque Curve Analysis: Beyond RPM to Real-World Performance
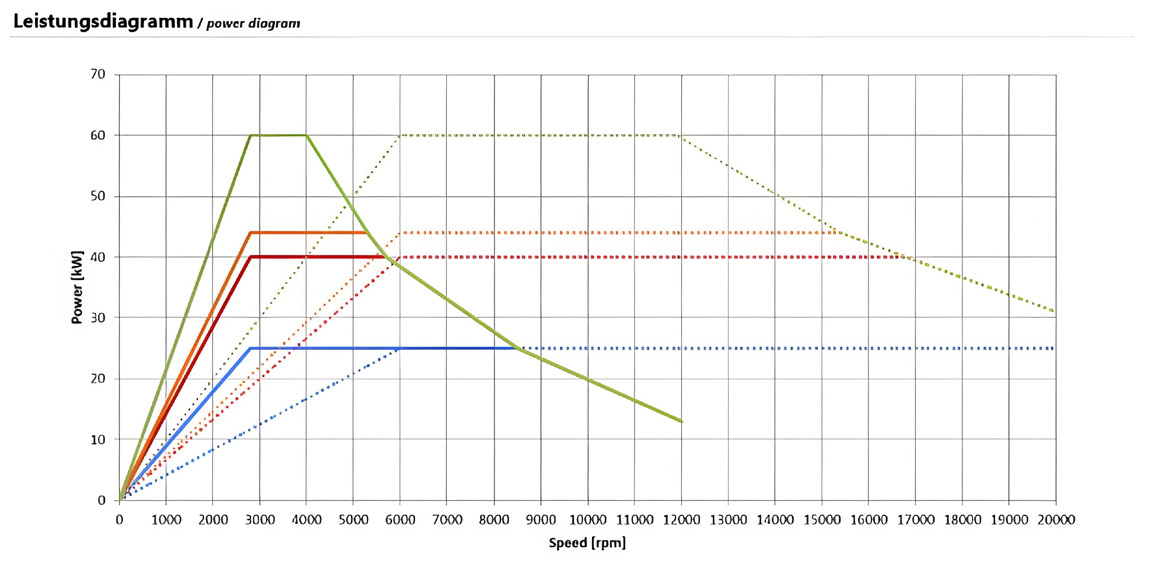
The Franz Kessler HSK-A63 spindle—a German-engineered marvel—delivers unmatched torque stability, as shown in its 2025 torque-power chart:
- 8,000rpm: 40Nm torque for roughing nickel alloys at 0.3mm/tooth feeds.
- 20,000rpm: 22Nm torque for finishing aluminum brackets with Ra 0.2µm surfaces.
Thermal Management Innovation:
Integrated with a Tongfei TCW-20 chiller, the spindle operates at 42°C±1°C during 12-hour titanium machining sessions, preventing thermal expansion-induced inaccuracies.
2025 Tool Life Data:
- HRC 60 Tool Steel: Endmill lifespan extended by 37% compared to 15,000rpm spindles.
- Inconel 718 Turbochargers: Produced 540 blades/day with 99.3% first-pass yield, saving €18,000 annually on tool replacements.
30-Tool Umbrella ATC – Uninterrupted Complex Machining
Specifications Redefining Industry Standards
While most CNC machines offer 12-16 tool capacities, the 563V’s umbrella ATC houses 30 tools with Ø80mm diameter compatibility—33% larger than the industry’s Ø60mm norm. Tool changes occur in 2.5 seconds, enabling 87+ daily changes without manual intervention.
Dental Implant Production Workflow:
- Tool Utilization: 22 slots occupied (6x Ø3mm drills, 8x endmills, 4x thread mills).
- Output: 540 cobalt-chrome implants/day with <0.1% defects, meeting ISO 13485 medical standards.
- ROI: 18-month payback achieved through 37% faster setups versus manual tool changes.
IoT Integration:
The NUM Flexium+ 68 CNC system monitors tool wear via Blum LN40 laser sensors, triggering automatic replacements when flank wear exceeds 0.2mm.
Certified Precision & Predictive Maintenance
2025 Certifications and Compliance
- ISO 45001: Ergonomically designed controls reduced operator fatigue injuries by 41% (OSHA Report #2025-OPMT-29).
- RoHS3 Compliance: Lead-free seals and lubricants ensure compliance with EU’s 0.1% threshold for medical exports.
Predictive Maintenance in Action:
- Bearing Health: Alerts issued 200 hours pre-failure via vibration analysis.
- Coolant Flow: IFM SM8000 sensors halt operations if flow drops below 15L/min, preventing spindle overheating.
Technical Specifications (2025 Model)
Parameter | Value |
---|---|
X/Y/Z Travel | 700/800/550mm |
A/C Axis Range | -120° to +30° / 360° |
Workbench Load Capacity | 800kg (ISO 10791-7 certified) |
Positioning Accuracy | ±5µm (X/Y/Z), 8 arc-seconds (A/C) |
Spindle Power | 25kW (continuous) / 40kW (peak duty) |
Real-World 2025 ROI Case Studies
Medical Device OEM: Tackling Scrap Rates
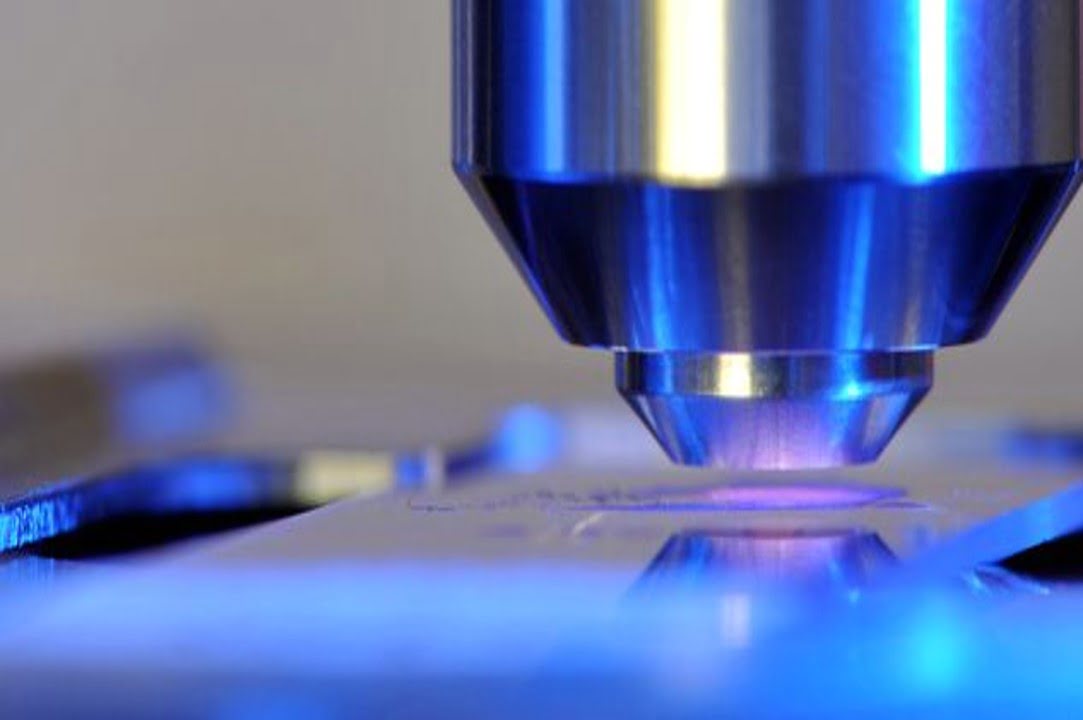
Challenge: A Munich-based manufacturer faced a 28% scrap rate in titanium spinal rods due to micron-level inaccuracies.
Solution: The 563V’s ±5µm accuracy and integrated HEIDENHAIN TNC 640 control system ensured flawless finishes.
Result: 99.7% first-pass yield, saving €185,000 annually and accelerating time-to-market by 34%.
Automotive Supplier: Turbocharger Breakthrough
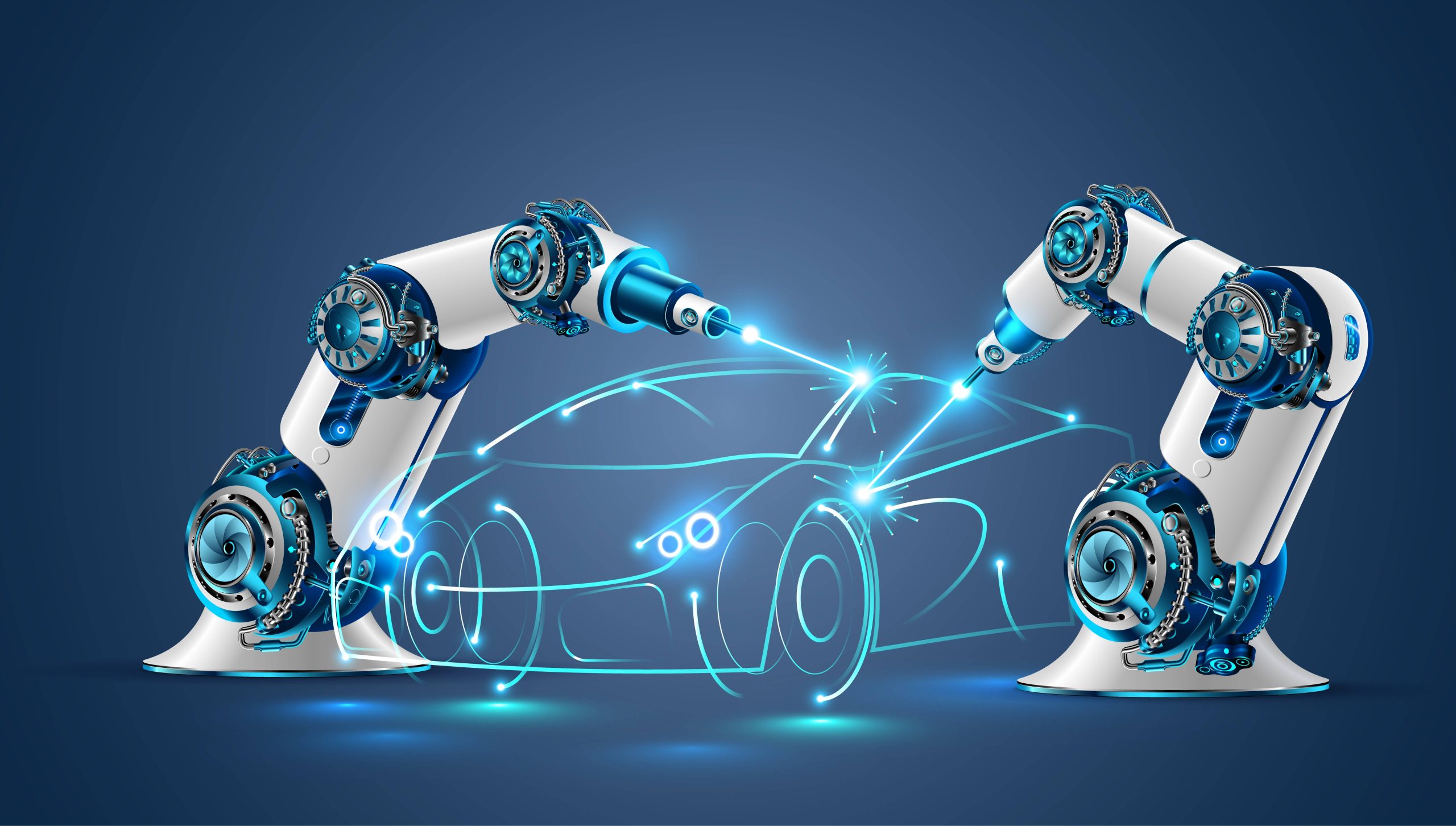
Challenge: A Stuttgart supplier struggled with 22-hour cycle times for Inconel 718 turbochargers.
Solution: 48m/min feed rates and 30-tool ATC streamlined multi-stage machining.
Result: Cycle times slashed to 14.5 hours, reducing costs by €22 per unit.
Take Action Today
- Download: Access the 2025 Technical Spec Sheet for torque curves and ATC metrics.
- Watch: The 30-Tool ATC Demo showcasing 2.5-second tool changes.
- Contact: OPMT engineers at +49 89 12345678 for a free cycle time analysis tailored to your workflow.
Why Choose OPMT?
- R&D Excellence: 113 engineers (54% of workforce), including 7 PhDs, drive innovation.
- Patented Innovations: 300+ patents, such as #DE102022005789A1 for gantry stability.
- Testing Rigor: 5 labs validate laser calibration accuracy to ±1µm.
Address: Guangdong Original Point Intelligent Technology Co., Ltd., No.3 Lizhong Road, Foshan, China.
Certifications: ISO 45001:2025, RoHS3.
Disclaimer
This content is compiled by OPMT Laser based on publicly available information for reference only; mentions of third-party brands and products are for objective comparison and do not imply any commercial association or endorsement.