Nylons have been a cornerstone of manufacturing since their inception in the 1930s, and their versatility continues to captivate industries today. As polyamide polymers, these materials are essential in producing everything from plastic films to metal coatings, particularly in demanding sectors like oil and gas. Did you know that Nylon 12 (PA 12) is recognized for its exceptional strength and lightweight properties, making it a top choice for additive manufacturing?
You may be wondering how this material can enhance your projects. In this article, we will uncover the impressive properties of PA 12, including its moisture resistance and thermal stability, while also exploring its diverse applications across various industries. Whether you’re a seasoned professional or just starting to learn about advanced materials, you’ll find valuable insights that can help you make informed choices for your next project. Get ready to discover how Nylon 12 can elevate your manufacturing processes!
Nylon 12 Properties
PA 12, commonly referred to as Nylon 12, is a versatile thermoplastic renowned for its exceptional toughness, tensile strength, and impact resistance. This material is widely utilized in various applications, including automotive components and 3D printing, due to its remarkable mechanical attributes.
Key Characteristics of PA 12
- Tensile Strength: PA 12 exhibits impressive tensile strength, making it suitable for demanding applications where durability is essential.
- Chemical Resistance: This polyamide demonstrates strong resistance to many chemicals, oils, and solvents, ensuring longevity in challenging environments.
- Thermal Stability: PA 12 maintains structural integrity at elevated temperatures, withstanding heat up to 185°C without significant degradation.
Applications of Nylon 12
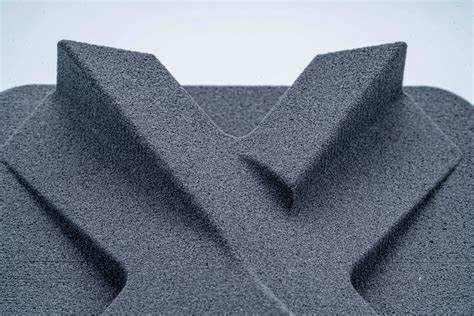
Nylon 12 finds use in numerous industries due to its beneficial properties. Common applications include:
- Automotive Components: Utilized for gears, bearings, and other critical parts that require high impact strength.
- Aerospace Parts: Lightweight yet durable materials are essential in aerospace applications where performance and reliability are paramount.
- Functional Prototypes: In additive manufacturing processes like Fused Deposition Modeling (FDM) and Multi Jet Fusion (MJF), PA 12 serves as an effective material for creating prototypes and functional parts.
Understanding the differences between generic PA 12 and proprietary forms is crucial for selecting the right material for specific applications. Below is a comparison of various Nylon 12 types:
Material Type | Process | Key Features |
---|---|---|
Generic PA 12 | Injection Molding | High impact strength and abrasion resistance |
FDM Nylon 12™ | Fused Deposition Modeling (FDM) | Cost-effective for rapid prototyping |
HP® High Reusability PA 12 | Multi Jet Fusion (MJF) | Enhanced reusability and efficiency in production |
By leveraging these properties and understanding the unique advantages of different Nylon 12 variants, manufacturers can make informed decisions that enhance product performance and longevity.
FDM Nylon 12™ Overview
FDM Nylon 12™ is a high-performance thermoplastic filament primarily utilized in Stratasys FDM printers. Renowned for its exceptional tensile strength of 48 MPa, this material is valued for its flexibility and durability, making it suitable for producing robust components. During the printing process, the filament is heated and extruded through the printer’s nozzle, allowing for precise layer deposition.
Support Structures in FDM Printing
Similar to other Fused Deposition Modeling (FDM) techniques, designs featuring overhangs necessitate the incorporation of support structures. Many modern FDM printers are equipped with dual extrusion capabilities—one nozzle for Nylon 12™ and another for a removable support material such as water-soluble PVA. This functionality streamlines post-processing by enabling easy removal of supports once printing is complete.
Mechanical Specifications
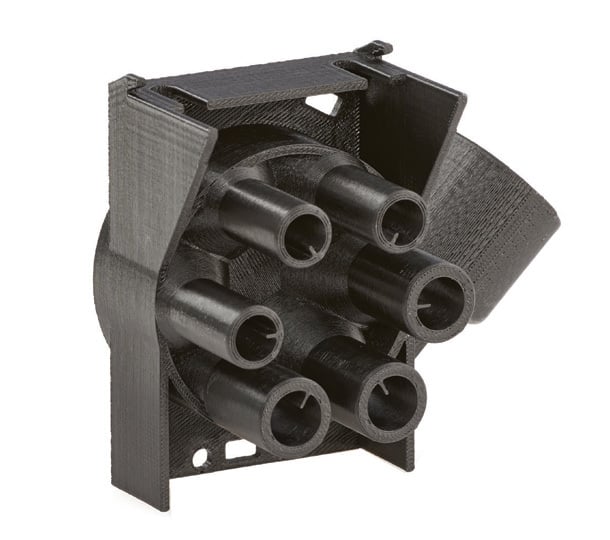
The mechanical properties of HP PA 12 are crucial for evaluating its performance in various applications:
Property | Value |
---|---|
Tensile Strength (XY) | 48 MPa / 6960 psi |
Tensile Modulus (XY) | 1700 MPa / 247 ksi |
Elongation at Break (XY) | 20% |
IZOD Impact Strength | 3.5 kJ/m² |
Heat Deflection (XY) | 175 ºC / 347 ºF |
These specifications underscore Nylon 12’s suitability for demanding applications across diverse industries, including aerospace and automotive sectors.
MJF and HP® 3D High Reusability Polyamide 12
HP® 3D High Reusability Polyamide 12 (HP® PA 12) is a specialized thermoplastic designed for use with Multi Jet Fusion (MJF) technology. This material is valued for its impressive mechanical properties, including high tensile strength, durability, and a reusability ratio of up to 80%, which significantly minimizes waste during production.
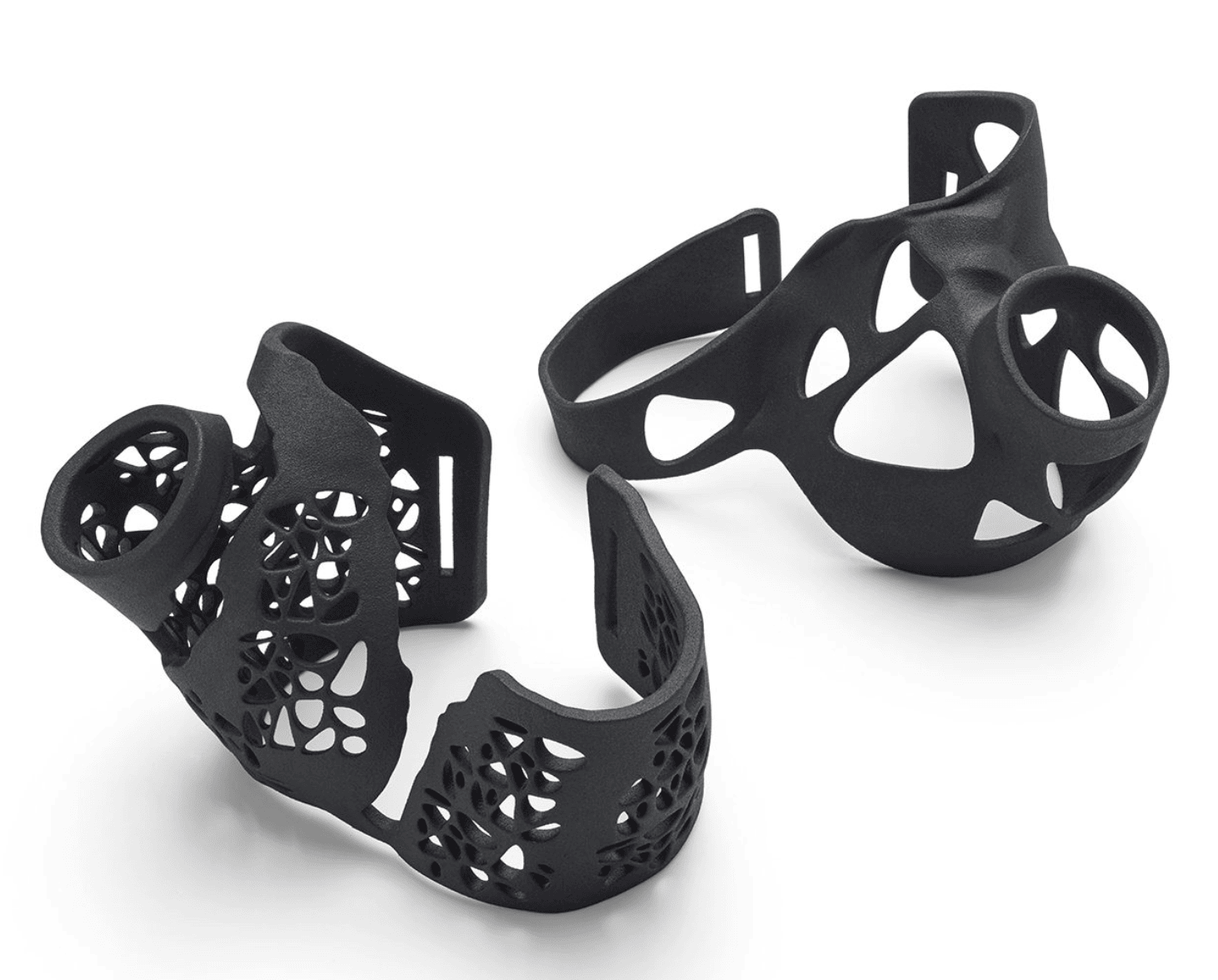
Customers frequently opt for the MJF process due to its self-supporting capabilities, granting engineers the flexibility to design complex geometries without the need for traditional support structures. This feature allows for the creation of intricate assemblies as single pieces, enhancing manufacturing efficiency and reducing assembly time.
After the printing process with HP® MJF, parts must be carefully extracted from the bed of unfused powder. This essential post-processing step ensures the integrity of the final product and should be considered when evaluating overall production costs. Unlike Fused Deposition Modeling (FDM), MJF technology produces nearly isotropic materials, resulting in minimal stiffness variation across different printing directions.
In 2025, as industries increasingly prioritize sustainability and efficiency, HP® PA 12 remains a leading choice for manufacturers seeking reliable and environmentally friendly solutions in additive manufacturing.
Why Use HP® PA 12
HP® PA 12 is a superior material for applications that require a balance of strength and precision. This polyamide features nearly isotropic mechanical properties, enabling intricate designs with excellent surface quality. SyBridge utilizes HP® PA 12 to manufacture components with high density and low porosity, making it ideal for various applications, including texturing, coloring, embossing, and engraving. Its density closely resembles that of traditional injection molding materials like ABS, ensuring mechanical performance that meets rigorous standards, particularly in the medical field where biocompatibility is crucial.
As a cost-effective alternative for low-volume production runs, HP® PA 12 does not compromise on quality. Its ease of sterilization enhances its suitability for medical applications where safety is paramount. By leveraging its unique properties, industries can achieve significant advancements in product design and functionality, addressing evolving market demands throughout 2025 and beyond.
Popular Applications
HP® PA 12 is celebrated for its durability, making it an ideal choice for applications that require flexible materials resistant to breaking or cracking under repeated use. Some widely utilized applications include:
- Snap-fit closures
- Casings
- Mounting hardware for outdoor enclosures
- Threaded inserts
- Parts subjected to vibration
- Kinetic components
- Jigs and fixtures
The density of HP® PA 12 is comparable to common plastics like ABS. However, its flexibility enables designers to create strong yet lightweight components through designing for additive manufacturing (DFAM). This capability allows for the production of parts that not only meet rigorous industry standards but also exhibit exceptional fatigue resistance—making it a perfect fit for demanding sectors such as aerospace and automotive industries.
Sustainability and Cost Considerations of HP PA 12
HP® PA 12 is engineered to significantly reduce waste by allowing for the reuse of leftover powder from previous builds. This innovative material composition enables the use of 20% new powder alongside 80% recycled powder in each production cycle. By recycling HP® PA 12, manufacturers not only minimize material waste but also maintain cost efficiency, ensuring competitive pricing for high-quality materials.
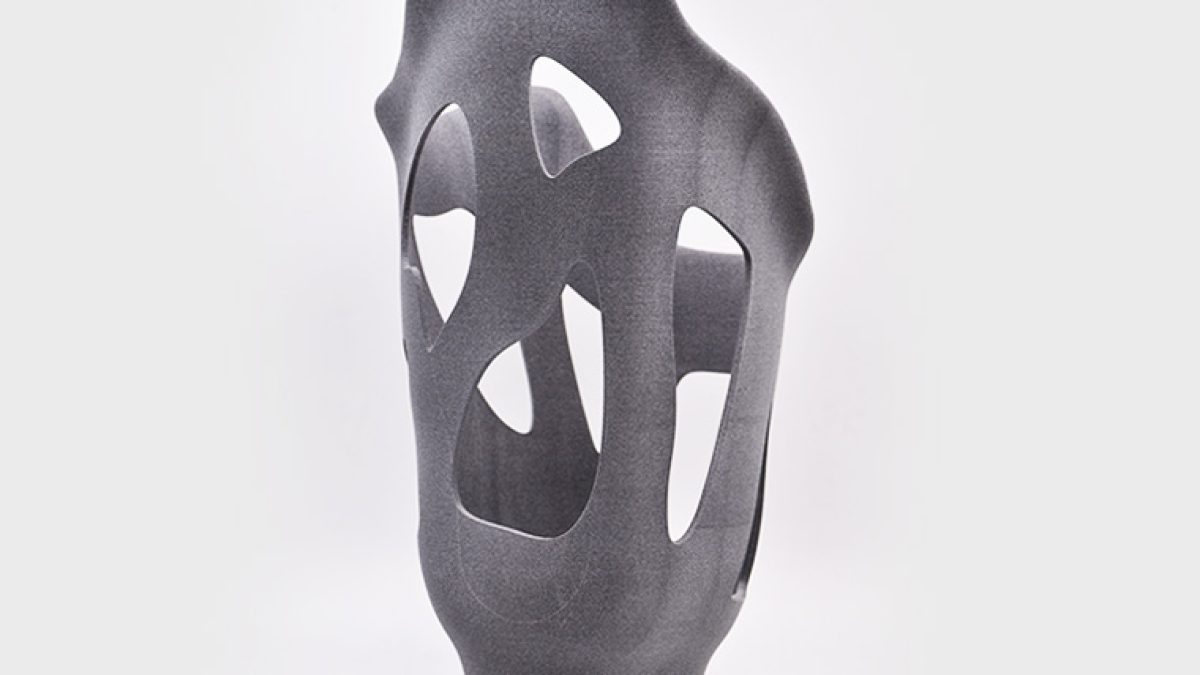
Design and Operational Insights
When utilizing HP® PA 12, designers benefit from fewer restrictions compared to traditional materials. Key design considerations include incorporating vents for internal cavities to prevent powder entrapment during the printing process. Post-processing begins with the removal of excess powder, typically achieved through air blasting or media blasting before surface finishing. While HP® PA 12 is available in a standard gray hue, it can also be dyed or painted to meet specific aesthetic requirements, offering versatility for various applications.
Economic and Environmental Impact
The adoption of HP® PA 12 aligns with sustainable manufacturing practices, as it boasts one of the highest reusability ratios among similar materials—up to 85%. This feature not only contributes to a circular economy but also enhances production efficiency by reducing overall material costs. As industries increasingly prioritize sustainability, HP® PA 12 stands out as a cost-effective solution that meets both environmental and operational demands in modern manufacturing.
By focusing on these aspects, HP® PA 12 not only supports eco-friendly initiatives but also provides manufacturers with a reliable and economically viable material choice for diverse applications in the evolving landscape of additive manufacturing.
Comparison of PA 12 with other polyamides
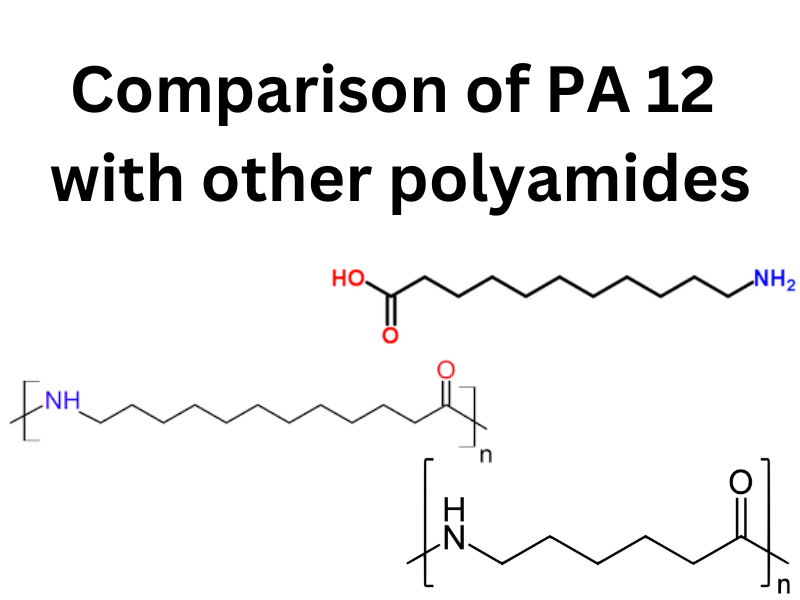
Comparison of Nylon (PA) 12 and Nylon (PA) 6
When comparing Nylon 12 (PA 12) and Nylon 6 (PA 6), key differences in their properties become evident. Both are polyamides with similar amide linkages, but they differ in monomer composition: PA 12 is derived from laurolactam, while PA 6 comes from caprolactam. This results in PA 12 having a higher carbon atom count in its repeating units, leading to superior tensile strength and impact resistance, making it suitable for demanding applications.
In terms of chemical resistance, PA 12 excels against solvents, oils, and fuels, ideal for automotive and industrial use, while PA 6 offers decent resistance but may falter in aggressive environments. Furthermore, PA 12 maintains its mechanical properties and dimensional stability at elevated temperatures, showcasing better thermal stability than PA 6. Both materials exhibit low moisture absorption rates, enhancing their stability in humid conditions. Overall, while both polyamides share advantages like good mechanical properties and chemical resistance, Nylon 12 stands out due to its enhanced strength, durability, and thermal performance.
Comparison of Nylon (PA) 11 and Nylon (PA) 12
Examining the differences between Nylon 11 (PA 11) and Nylon 12 (PA 12) reveals distinct characteristics that impact their applications. Both are polyamides with amide linkages but differ in monomer sources: PA 11 comes from 11-aminoundecanoic acid, while PA 12 is derived from laurolactam. This leads to PA 12 having a higher carbon count in its repeating units, resulting in superior tensile strength and impact resistance, making it ideal for applications requiring durability and wear resistance.
Both materials exhibit good chemical resistance to various solvents and oils, suitable for automotive and industrial sectors. However, PA 12 outperforms PA 11 in aggressive chemical environments. Additionally, PA 12 maintains its mechanical integrity at elevated temperatures, showcasing better thermal stability compared to PA 11. Both types have low moisture absorption rates, ensuring dimensional stability in humid conditions. Overall, while both Nylon 11 and Nylon 12 offer advantages as polyamides, Nylon 12‘s enhanced mechanical properties and thermal stability make it the preferred choice for demanding applications where strength and durability are essential.
When to Expect Your Part
HP® PA 12 typically operates within a standard lead time of five to seven business days for production. For expedited orders or smaller builds, OPMT Laser can complete prints in as few as three business days. Generally, MJF technology allows for the printing of up to 251 cubic inches per hour; therefore, a fully packed HP® print volume may require approximately 17 hours of build time.
Post-printing cooling is an essential factor to consider, as it can range from three to 50 hours depending on the size of the build. Smaller parts with less powder tend to cool more quickly. Fortunately, HP® has implemented a secondary post-processing station that can rapidly cool any part within ten hours if necessary.
If you are interested in challenging traditional design limitations to create innovative products, we encourage you to explore the capabilities of HP® PA 12. Reach out to our team today to discover how we can help bring your product vision to fruition efficiently and effectively.
Disclaimer
This content is compiled by OPMT Laser based on publicly available information for reference only; mentions of third-party brands and products are for objective comparison and do not imply any commercial association or endorsement.