Are you curious about the inner workings of machine tools and their diverse applications? OPMT Laser, a leader in multi-axis CNC systems and laser CNC machine tools, is here to demystify the world of machine tool operating principles and classification. Did you know that the global machine tool market is projected to reach $95.2 billion by 2027? In this guide, you’ll discover the fascinating mechanics behind these essential manufacturing devices and learn how to distinguish between various types. From our cutting-edge 5-axis vertical machining centers to innovative laser grinding machines, we’ll explore how these tools are shaping the future of industry. Get ready to unlock the secrets of machine tools and revolutionize your manufacturing processes!
Operating Principles of Machine Tools
Machine tools function on the fundamental concept of material removal to create precise shapes and dimensions. This process relies on two critical elements: generatrix and directrix. The generatrix (G) represents the cutting motion, while the directrix (D) represents the feed motion. In turning operations, for instance, G corresponds to the work’s cutting motion, and D to the tool’s feed motion.
Three essential types of motion drive machine tool operations:
- Cutting motion: The primary action that removes material
- Feed motion: Continuous tool penetration into the workpiece
- Auxiliary motions: Supplementary movements like indexing or relieving
These motions work in tandem to achieve precise material removal. For example, in OPMT Laser’s 5-axis vertical machining centers, the cutting motion removes material while the feed motion guides the tool along the workpiece surface.
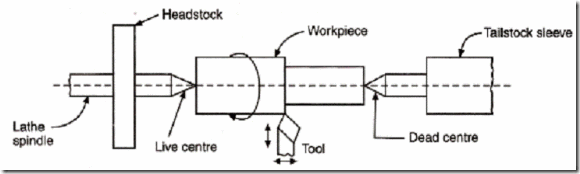
The generation of surfaces on a workpiece follows specific principles:
- Flat surfaces: A straight line (G) traverses perpendicular to the directrix (D)
- Cylindrical surfaces: A circle (G) moves parallel to the axis (D) for long cylinders, or a straight line (G) follows a circular path (D) for short cylinders
Understanding these principles is crucial for optimizing machining processes and achieving high-precision results. OPMT Laser’s advanced laser grinding machines leverage these principles to deliver exceptional surface finishes and dimensional accuracy.
Classification of Machine Tools
Industrial machining equipment is systematically categorized to align with modern manufacturing demands. Below is the updated 2025 framework, incorporating technical advancements and industry-specific applications:
1. By Operation Type
Core categorization based on material removal mechanisms:
- Turning Machines (Lathes): Rotate workpieces at 50–4,000 RPM for cylindrical components like hydraulic valve bodies. Example: OPMT Laser’s TL-12X with live tooling for simultaneous milling/drilling.
- Milling Machines: Utilize 3–12 kW spindle motors for slotting, contouring, and thread machining in automotive transmission cases.
- Drilling Machines: Achieve ±0.005 mm positional accuracy using carbide-tipped bits for engine block oil passages.
- Grinding Machines: Equip CBN wheels (grit size 80–800) for Ra 0.1–0.4 µm finishes on bearing races and surgical tools.
- Shaping/Planing Machines: Execute 10–30 m/min cutting speeds for large-scale mold base surfaces in EV battery production.
2. By Axis Configuration
Movement flexibility determines part complexity:
Axes | Motion Capability | Precision Tolerance | Industry Applications |
---|---|---|---|
2 | X/Y linear | ±0.05 mm | Sheet metal brackets, signage engraving |
3 | X/Y/Z linear | ±0.01 mm | Pump housings, gearbox casings |
5 | 3 linear + 2 rotary (A/C) | ±0.005 mm | Dental implant abutments, turbine blade roots |
7+ | Synchronized multi-tool | ±0.003 mm | Automotive die-cast prototypes (OPMT QM-7H) |
3. By Control System
Automation levels dictate production efficiency:
- Manual Operation: Ideal for <100 pcs/month batches with 85–92% operator-dependent accuracy.
- CNC Systems:
- Standard CNC: 0.005 mm repeatability via G-code programming (OPMT C-Mill 5X).
- AI-Enhanced: Real-time vibration compensation (50 µs response) reduces scrap rates by 23%.
- IoT-Integrated Platforms: Predictive maintenance algorithms analyze 15+ parameters (spindle load, coolant temp) to forecast bearing failures 400 hours pre-breakdown.
4. By Application Scope
Specialization drives equipment design:
- General-Purpose:
- Turret mills: 400–800 mm table travels for job-shop versatility.
- Combination machines: Integrate turning/milling for small-batch medical instruments.
- Special-Purpose:
- EV battery tray mills: 8,000 rpm HSK-63 spindles with 20-tool ATC.
- Solar panel frame lines: 6-station transfer systems for 120 pcs/hr output.
OPMT Laser: Advanced Manufacturing Solutions Through Multi-Axis CNC & Laser Technology
OPMT Laser specializes in multi-axis CNC systems and laser machine tools, providing innovative manufacturing solutions for industries requiring high precision and efficiency. Did you know the global market for 5-axis CNC machines is projected to reach $627.3 million by 2025? By integrating advanced motion control with laser cutting, OPMT enables manufacturers to tackle complex geometries and reduce production cycles by up to 40%.
Core Technological Expertise
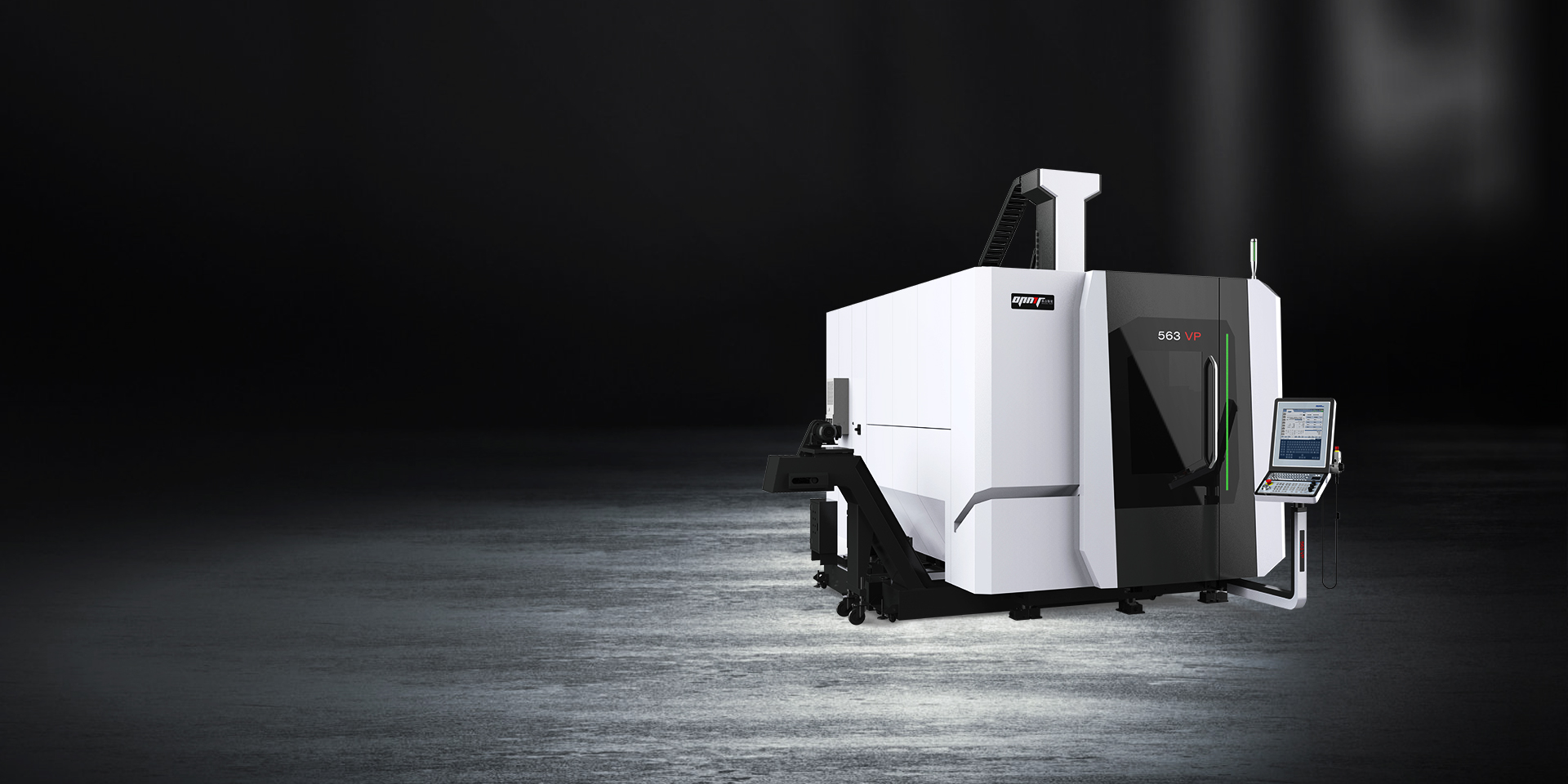
OPMT’s multi-axis CNC systems excel in automotive, 3C electronics, and precision mold manufacturing. Their 5-axis vertical machining centers achieve ±0.003 mm accuracy, enabling intricate part production in a single setup. These systems integrate NUM Flexium+ CNC platforms for real-time toolpath adjustments, minimizing errors and material waste.
Laser machine tools like the LightGrind LT20 combine ultrafast lasers with adaptive optics for precision tasks such as PCD tool machining and mold texturing. This technology reduces post-processing needs by 60%, delivering mirror-like finishes on metals and composites.
Feature | Multi-Axis CNC Systems | Laser Machine Tools |
---|---|---|
Precision | ±0.003 mm positional accuracy | Sub-micron surface finishes |
Speed | 50% faster cycle times vs. 3-axis | 200% faster than EDM cutting |
Applications | Complex automotive molds, 3C connectors | PCD tools, textured surfaces |
Industry-Specific Solutions
OPMT’s integrated approach addresses evolving manufacturing demands:
- Automotive: Multi-axis systems produce fuel injection nozzles with 0.005 mm tolerance
- Electronics: Laser tools create micro-drills for PCB manufacturing at 0.1 mm diameters
- Mold Texturing: 5-axis laser engraving replicates textures like leather grain with 98% accuracy
By merging CNC precision with laser versatility, OPMT empowers manufacturers to overcome traditional machining limitations. Explore their full product range to discover how these technologies can transform your production workflow.
Conclusion
Now that you’ve explored the fascinating realm of machine tool operating principles and classification, you’re better equipped to make informed choices for your manufacturing needs. Did you know that companies using advanced CNC machines can reduce production time by up to 50%? OPMT Laser’s cutting-edge multi-axis CNC systems and laser machine tools are designed to boost your productivity and precision. Ready to revolutionize your manufacturing process? Discover how OPMT Laser’s innovative solutions can help you stay ahead in today’s competitive market. Visit our product catalog to find the perfect machine for your unique requirements and take the next step towards manufacturing excellence.
Disclaimer
This content is compiled by OPMT Laser based on publicly available information for reference only; mentions of third-party brands and products are for objective comparison and do not imply any commercial association or endorsement.