Laser galvanometers, also known as galvo systems, play a crucial role in modern manufacturing, enabling exceptional precision in laser beam control through mirror movement. If you’re curious about how industries achieve intricate laser marking and cutting with astonishing speed and accuracy, you’re not alone—over 70% of manufacturing processes now depend on these advanced technologies.
In this article, OPMT Laser will guide you through the types and applications of laser galvanometers, shedding light on their functionality and versatility. You’ll learn about the two main categories—closed-loop and open-loop galvanometers—and discover their wide-ranging uses in sectors such as manufacturing, biomedical imaging, and automation. Are you ready to unlock the potential of laser galvanometers? Let’s get started!
What are Laser Galvanometers?
Laser galvanometers, also known as galvo scanners, are precision optical devices that utilize mirrors to swiftly and accurately direct laser beams. These systems are crucial in various laser applications such as marking, engraving, and material processing. By rapidly manipulating the laser beam across a surface, galvanometers facilitate the creation of intricate designs and high-quality outputs, making them indispensable in sectors like manufacturing, medical devices, and entertainment.
What does laser galvanometers refer to?
A laser galvanometer is an electromechanical system that employs one or more mirrors to deflect a laser beam. The term “galvanometer” originates from its function of measuring electric current through mirror deflection. In laser applications, these devices are typically used in pairs to control the X and Y axes of the laser beam, enabling precise positioning and movement across a designated area. This capability supports applications such as laser marking, where logos or text can be permanently engraved onto various materials.
How does laser galvanometers work?
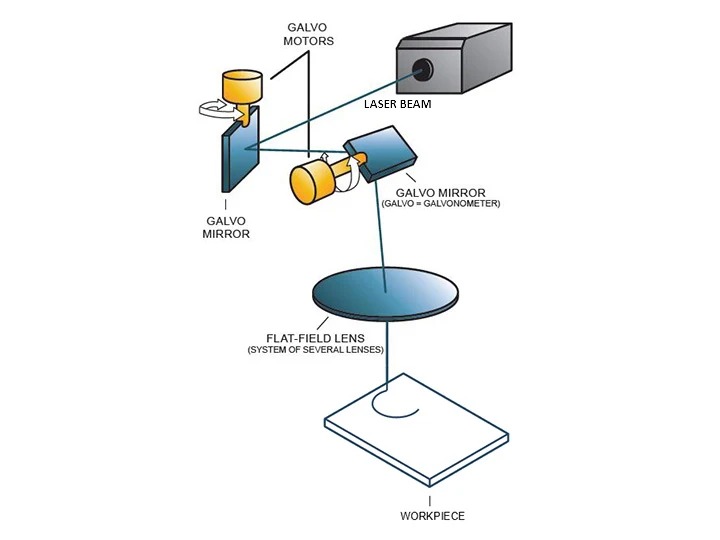
The operation of a laser galvanometer involves several key components:
- Galvanometer Motors: These motors convert electrical signals into mechanical movement. When voltage is applied, they rotate the mirrors at specific angles.
- Closed-Loop Control System: This system continuously monitors the position of the mirrors using sensors and adjusts the electrical input to maintain precise control over the beam’s direction.
- Mirrors: Typically mounted on the galvanometer motors, these mirrors reflect the laser beam onto the target surface. The angle of reflection changes according to the motor’s position, allowing for rapid scanning over a wide area.
This mechanism enables high-speed and high-precision applications by allowing quick adjustments to the laser’s focus and direction without requiring movement of the entire laser apparatus.
Types of Laser Galvanometers
When selecting a laser galvanometer, it’s crucial to understand the distinct categories available, primarily closed-loop and open-loop systems. Each type serves different operational needs and precision requirements.

Closed-Loop Galvanometers
Closed-loop galvanometers are equipped with feedback mechanisms that monitor the position of mirrors, ensuring precise control over their angles. By integrating position sensors, these systems deliver high accuracy and repeatability, making them suitable for applications that demand exceptional precision, such as laser engraving and cutting. The dynamic adjustment capabilities of closed-loop systems allow them to adapt in real-time, which is vital in high-speed environments where even minor deviations can compromise output quality.
Open-Loop Galvanometers
Conversely, open-loop galvanometers lack feedback mechanisms, resulting in less precise movements. However, they are typically more cost-effective and well-suited for applications where absolute precision is not critical. Common uses for open-loop systems include basic marking tasks or barcode scanning, where speed and efficiency are prioritized over pinpoint accuracy. Despite their limitations in precision, open-loop galvanometers remain a popular choice for projects with budget constraints.
Feature | Closed-Loop Systems | Open-Loop Systems |
---|---|---|
Precision | High accuracy with feedback | Moderate accuracy without feedback |
Cost | Generally more expensive | More cost-effective |
Applications | Laser engraving, cutting | Basic marking, barcode scanning |
Feedback Mechanism | Yes | No |
Dynamic Adjustment | Yes | No |
Choosing between closed-loop and open-loop galvanometers depends on your specific application requirements. For projects that necessitate high precision and dynamic adjustments, closed-loop systems are the optimal choice. In contrast, open-loop systems offer a viable solution for less critical tasks where budget considerations are paramount. Understanding these distinctions will aid in making an informed decision tailored to your operational needs as of 2025.
Applications of Laser Galvanometers
Laser galvanometers, also known as galvo lasers, are vital instruments utilized across various sectors due to their precision and adaptability. Their diverse applications reflect their importance in contemporary manufacturing and technology.
Laser Marking and Engraving
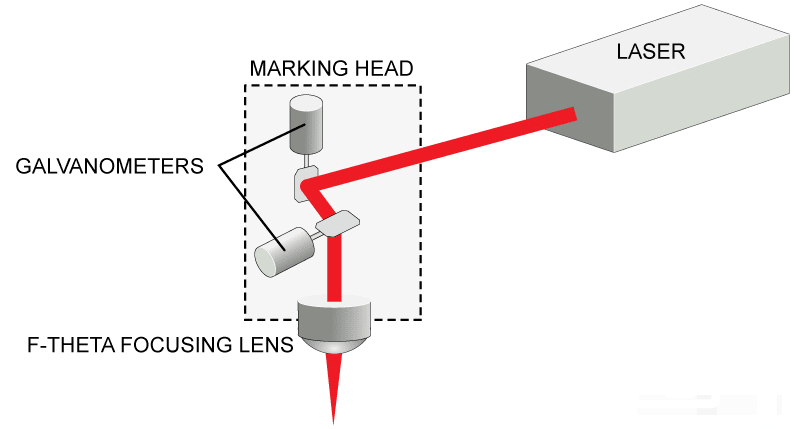
A primary use of laser galvanometers is in laser marking and engraving. These systems are widely employed for inscribing products with serial numbers, logos, and barcodes. The swift operation of galvo lasers makes them essential in high-volume production settings, particularly within the automotive and electronics industries. Their capability to produce permanent, high-quality markings without consumables enhances operational efficiency and reduces costs.
Material Processing
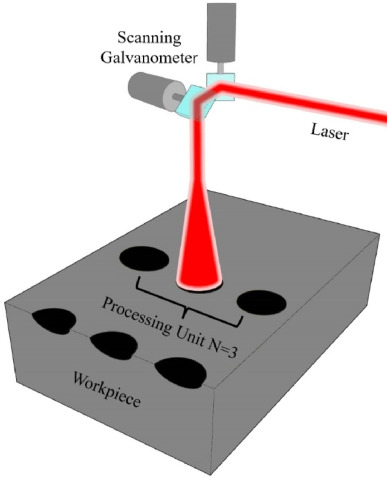
Galvo lasers are integral to material processing tasks such as laser cutting, welding, and drilling. By directing laser beams with remarkable accuracy, these systems facilitate intricate cutting patterns and efficient processing in various fields, including aerospace and medical device manufacturing. The versatility of galvo lasers allows them to work effectively with different materials, making them suitable for a wide range of applications.
Biomedical Imaging
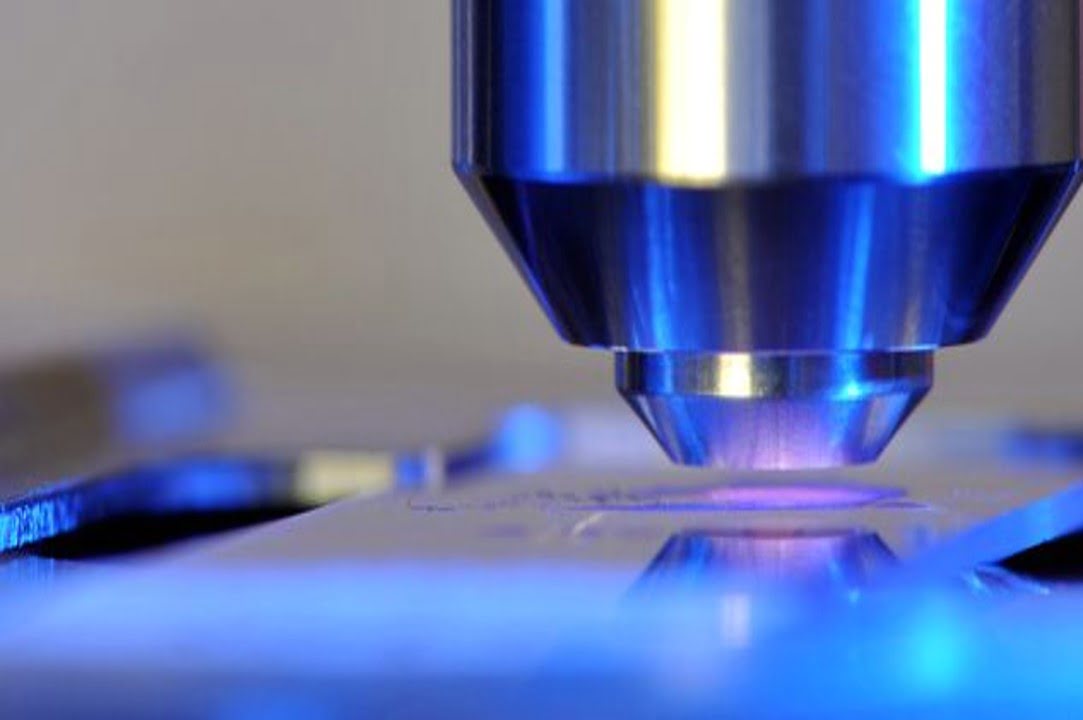
In the healthcare sector, laser galvanometers are utilized in advanced imaging techniques like confocal microscopy and Optical Coherence Tomography (OCT). These high-resolution imaging methods are crucial for diagnostics and research, enabling detailed examinations of biological tissues. The precision provided by galvo lasers ensures that medical professionals obtain accurate images for effective diagnosis.
3D Printing
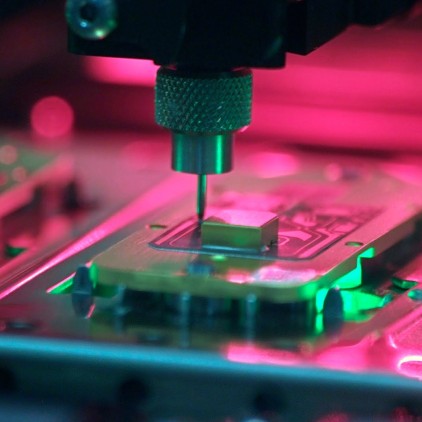
Galvo lasers significantly contribute to additive manufacturing processes. In 3D printing, they allow for rapid layer-by-layer construction by precisely controlling the laser’s focus and movement. This ability enables the creation of complex geometries efficiently, positioning galvo lasers as valuable assets in modern manufacturing workflows.
Automation and Robotics
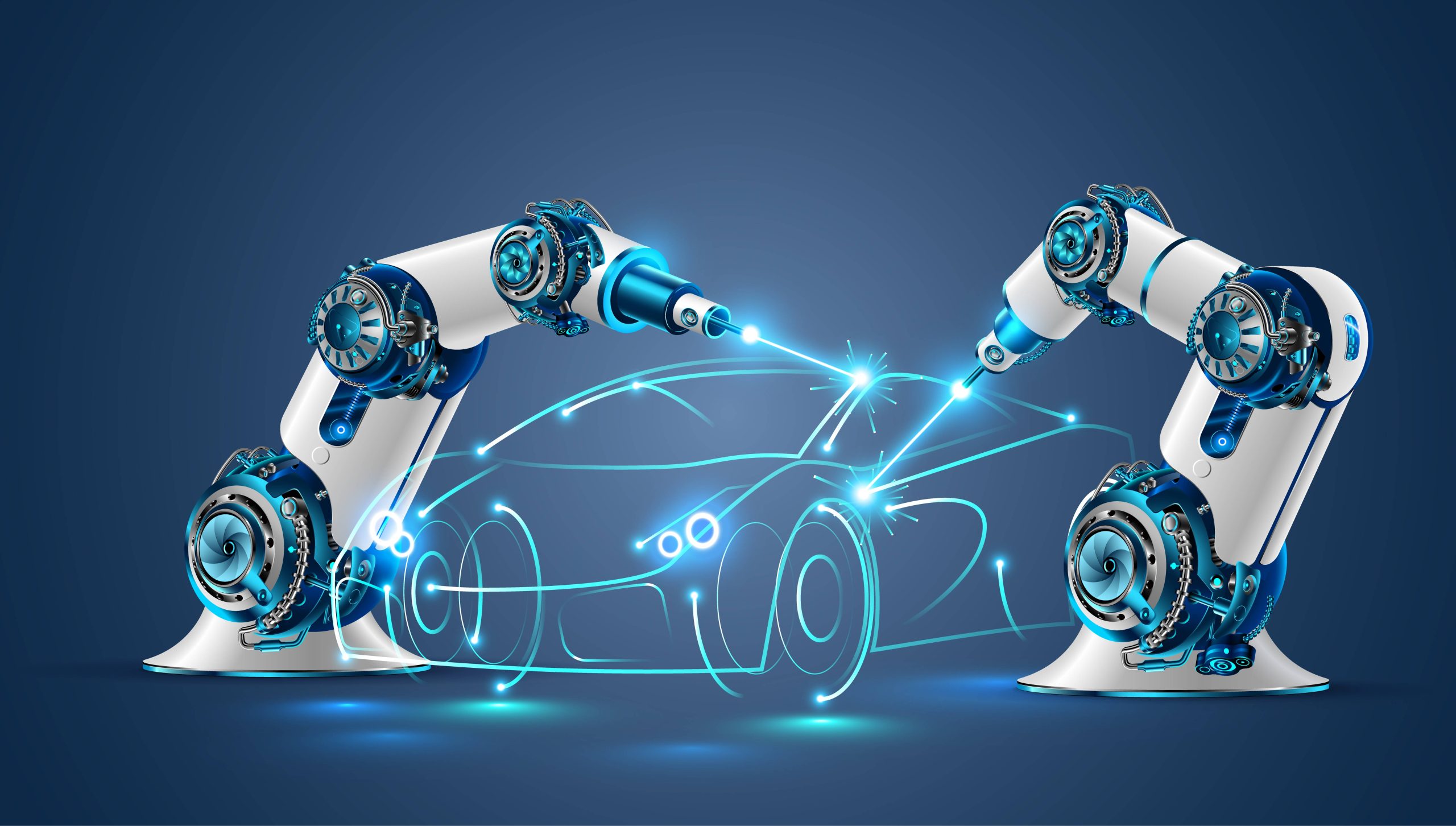
Incorporated into automated systems, laser galvanometers improve accuracy in tasks such as material handling and quality control. Their capacity for rapid repositioning of lasers enhances overall production efficiency. This integration is particularly advantageous in industries where speed and precision are essential for maintaining competitive advantages.
Entertainment
In the entertainment sector, galvanometers direct lasers to create captivating patterns and effects during light shows and visual displays. This application highlights the versatility of galvo lasers beyond conventional industrial uses, emphasizing their role in enhancing audience experiences at events.
Research Applications
Galvo lasers are also employed in scientific research for tasks such as spectroscopy and fluorescence imaging. Their ability to manipulate light with precision enables researchers to conduct experiments requiring high accuracy and control over light interactions with materials.
Laser galvanometers play a crucial role across numerous applications in various industries. Their speed, precision, and adaptability make them indispensable tools in laser marking, material processing, biomedical imaging, 3D printing, automation, entertainment, and scientific research. As technology progresses into 2025 and beyond, the range of applications for galvo lasers is expected to expand further, solidifying their significance in advancing industrial capabilities.
Key Benefits of Laser Galvanometers
Exceptional Speed
Laser galvanometers are celebrated for their remarkable speed, achieving operational velocities of up to 4000 mm/s. This capability allows them to surpass traditional laser systems, drastically reducing processing times for tasks such as engraving and marking. In high-volume production settings, this speed translates into significant time savings, enabling manufacturers to boost productivity and profitability.
Unmatched Precision
The precision offered by laser galvanometers is another critical advantage. With angular resolutions as fine as 15 µrad (0.0008°), they excel in applications requiring meticulous detail, such as intricate engravings and markings. This level of accuracy minimizes errors and material waste, making it essential for industries where quality control is paramount.
Versatility in Material Processing
Galvo lasers demonstrate exceptional versatility, effectively processing a variety of materials including metals, plastics, and ceramics. This adaptability makes them suitable for diverse applications ranging from cutting and welding to engraving. Their ability to handle different materials without compromising quality enhances their utility across various sectors.
Lower Maintenance Requirements
A significant benefit of laser galvanometers is their reduced maintenance needs. Unlike conventional laser systems that rely on numerous mechanical components like belts and pulleys, galvo systems feature fewer moving parts. This design leads to lower maintenance costs and increased reliability over time, allowing businesses to minimize downtime and maximize operational efficiency.
The advantages of laser galvanometers—high speed, precision, versatility across materials, and reduced maintenance—position them as vital tools in modern manufacturing processes. Their ability to enhance productivity while ensuring high-quality results makes them a preferred choice for businesses aiming to optimize their operations in 2025 and beyond.
Limitations of Laser Galvanometers
Despite their effectiveness, certain limitations exist with laser galvanometers:
- Cost: High-quality galvo systems can be more expensive compared to simpler alternatives.
- Complexity: The technology requires sophisticated control systems and calibration processes to ensure accuracy.
- Limited Working Area: The effective working area is constrained by the size of the mirrors and the range of motion of the galvanometer motors.
Conclusion
The adaptability of laser galvanometers effectively addresses the challenges you face in precision applications. With their ability to control laser beams with exceptional speed and accuracy, these systems can enhance productivity and quality in sectors such as manufacturing and biomedical imaging. In fact, industries leveraging laser technology have reported productivity boosts of up to 30%.
As technology evolves, the potential applications for laser galvanometers will expand, paving the way for innovative solutions in automation and engineering. Are you excited to see how these cutting-edge devices can elevate your projects? Explore OPMT Laser’s offerings to unlock new possibilities and take your work to the next level!
Disclaimer
This content is compiled by OPMT Laser based on publicly available information for reference only; mentions of third-party brands and products are for objective comparison and do not imply any commercial association or endorsement.