Unlock the full potential of your projects with the right laser cutter power tailored to your specific applications. Whether you’re cutting through wood, metal, or plastic, understanding the power requirements is crucial for achieving precision and efficiency. Did you know that laser cutters can operate anywhere from 10W for paper to over 6000W for thick metals?
In this guide, OPMT Laser will illuminate the key factors that influence laser cutter power and how it impacts your results. You’ll learn about power measurement, the variables at play, and why selecting the appropriate wattage is vital for your success. Get ready to elevate your cutting and engraving skills as we break down everything you need to know!
How Does a Laser Cutter Work?
Laser cutting technology employs a highly focused beam of light to cut or engrave materials with exceptional precision. This method stands apart from traditional cutting techniques that utilize sharp blades. The term LASER is an acronym for Light Amplification by Stimulated Emission of Radiation, which encapsulates the fundamental principles behind this innovative process.

The Laser Generation Process
The laser beam is generated within a specialized tube filled with gases, typically carbon dioxide. When an electrical current passes through these gases, it excites the molecules, producing a powerful beam of light. This light is then directed through a series of mirrors that converge the beam into a single point at the laser head.
- Focused Beam Output: The laser head emits a concentrated beam capable of reaching extremely high temperatures, allowing it to melt or vaporize various materials, including metals.
Computer Numerical Control (CNC) Integration
Modern laser cutters are equipped with Computer Numerical Control (CNC) systems, enhancing their functionality and precision:
- Programming: Before cutting begins, operators input specific parameters into the CNC system, detailing the dimensions and desired patterns of the workpiece.
- Execution: Once programmed, the CNC directs the laser head to move accurately across the material, following predefined instructions to achieve precise cuts and engravings.
Applications and Advantages of Laser Cutting
Laser cutting technology is widely used across various industries due to its numerous advantages:
- High Precision: The ability to create intricate designs with remarkable accuracy makes laser cutting ideal for applications requiring detailed work.
- Speed and Efficiency: Laser cutters operate at impressive speeds, significantly reducing production times compared to conventional methods.
- Versatility: These machines can cut through a wide range of materials such as metal, wood, acrylic, and even fabric, making them suitable for diverse applications.
What Are the Factors That Affect the Power of Laser Cutters?
Understanding the factors that influence the effectiveness of laser cutters is essential for achieving optimal cutting results. The primary elements include wattage, beam quality, and wavelength. Each of these components plays a crucial role in determining how well a laser cutter can perform across different materials.
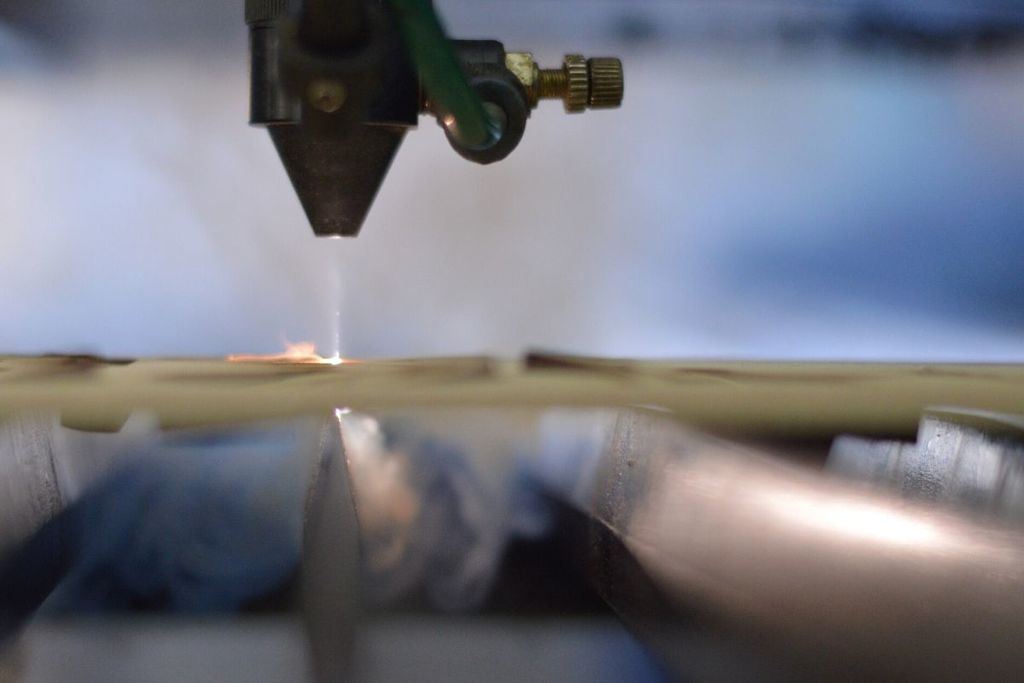
Wattage
The wattage of a laser cutter is a critical factor that dictates its cutting ability. Measured in watts (W), higher wattage allows for cutting thicker materials at increased speeds. For example, a 2000W laser cutter can efficiently slice through 1mm thick steel at rates of 25.0 to 31.0 m/min. However, with higher power comes the need for enhanced cooling systems and potentially higher operational costs.
- Cutting Speed: Increased wattage directly correlates with faster cutting speeds, which is vital for high-volume production environments.
- Material Thickness: Different materials require different power levels to achieve clean cuts. Thicker materials necessitate higher wattage for effective cutting.
- Edge Quality: Higher wattage can lead to smoother edges and reduced burr formation, minimizing the need for secondary processing.
Beam Quality
Beam quality is another significant factor impacting laser cutting performance. It refers to how well the laser beam can be focused and controlled, typically measured by the M² factor; lower values indicate better beam quality.
- Precision: A high-quality beam allows for tighter focusing, resulting in more precise cuts and engravings. This precision is particularly important for intricate designs.
- Efficiency: Improved beam quality leads to reduced energy consumption and material waste, contributing to overall cost savings during operations.
- Kerf Width: A focused beam produces a narrower kerf width, which minimizes material loss and enhances cutting accuracy.
Wavelength
The wavelength of the laser light significantly affects how different materials absorb energy during the cutting process.
- Material Interaction: Different materials have varying absorption rates based on their wavelengths. CO2 lasers (10.6 µm) are effective for organic materials but less so for metals, which may require higher power levels due to lower absorption rates.
- Reflectivity: Metals tend to reflect longer wavelengths more than shorter ones. Therefore, fiber lasers (around 1 µm) are often preferred for cutting reflective metals like aluminum as they minimize reflection losses and provide better penetration capabilities.
- Heat Affected Zone (HAZ): The wavelength also influences the size of the heat-affected zone during cutting; shorter wavelengths generally produce smaller HAZs, leading to cleaner cuts with less thermal distortion.
What Are the Types of Laser Cutter Power?
Laser cutters are primarily classified into two types based on how the laser beam is generated: CO2 laser cutters and fiber laser cutters. Each type has unique power levels and functionalities tailored to different materials and applications. Understanding these distinctions is crucial for selecting the right laser cutter for your specific needs.
CO2 Laser Cutter Power
CO2 laser cutting machines utilize a mixture of gases, including carbon dioxide, helium, and nitrogen. These gases are energized through electrical discharge, resulting in a laser beam with a wavelength of 10.6 micrometers. This wavelength makes CO2 lasers particularly effective for cutting non-metal materials such as wood, acrylic, and textiles. Interestingly, high-powered CO2 lasers can also handle some metal cutting tasks.
Classification of CO2 Lasers by Power Consumption
CO2 lasers are categorized into three main groups based on their power consumption:
- Low-Powered CO2 Lasers: These machines consume less than 100 watts (some as low as 10 watts) and are ideal for small-scale applications like cutting paper and wood.
- Medium-Powered CO2 Lasers: Operating within the range of 1000 to 1500 watts, these lasers are perfect for engraving both metallic and non-metallic materials. OPMT Laser offers a medium-range CO2 laser cutter that operates at 1500 watts, providing precision for intricate engraving tasks.
- High-Powered CO2 Lasers: Consuming over 1500 watts, these machines excel in deep cuts requiring high precision. For example, OPMT Laser’s high-powered CO2 cutter operates at approximately 2500 watts, making it suitable for demanding industrial applications.
Fiber Laser Cutter Power
Fiber laser cutters, often referred to as solid-state lasers, use a doped fiber optic cable as the active medium for generating the laser beam. This technology has evolved significantly, allowing fiber lasers to cut reflective metals like aluminum and copper with remarkable efficiency. They typically operate at twice the speed of CO2 lasers while being versatile enough to handle various organic materials.
Types of Fiber Lasers Based on Operation
Fiber lasers can be classified into three primary types based on their operational characteristics:
- Continuous Wave (CW) Fiber Lasers: These emit a steady beam of light, making them suitable for high-speed cutting, welding, and drilling applications.
- Pulsed Fiber Lasers: These lasers produce short bursts of light, typically lasting from a few nanoseconds to microseconds. They are commonly used for marking and engraving tasks.
- MOPA (Master Oscillator Power Amplifier) Fiber Lasers: This subtype of pulsed fiber laser utilizes a master oscillator to generate laser pulses that are then amplified. MOPA lasers can achieve very high peak powers in the kilowatt range with short pulse durations, ideal for precision applications.
Understanding the types of laser cutter power is essential for making informed decisions when selecting a laser cutting solution. Whether you require a CO2 or fiber laser cutter, OPMT Laser provides innovative CNC systems and laser processing solutions tailored to meet diverse industrial needs. For more information on our products, explore our offerings like the Micro 3D Laser Cutter or the LP550V Laser Cutter.
How to Select the Optimal Laser Cutter Power for Your Applications
Choosing the right laser cutter power is essential for achieving efficient and high-quality results tailored to your specific applications. This guide will explore the various power ranges available in laser cutters, how to determine the appropriate power for different materials and thicknesses, and examples of applications along with their ideal laser cutter power.
Laser Cutter Power Ranges and Their Ideal Uses
Laser cutters are available in a wide range of power outputs, typically from 10W to over 6,000W. Here’s a breakdown of the power ranges and their ideal applications:
- 10W – 100W: Best suited for engraving and cutting thin materials such as paper, cardboard, and thin plastics. This range is ideal for intricate designs where precision is key.
- 100W – 500W: Suitable for cutting thicker materials like wood, acrylic, and metals up to 1/4 inch thick. This range offers a balance between speed and detail.
- 500W – 2000W: Designed for cutting thicker materials, including metals up to 1 inch thick. This power range allows for efficient processing of robust materials.
- 2000W – 6000W or more: These high-powered lasers are used in industrial applications for cutting thick metals over 1 inch or for large-scale manufacturing processes.
Determining the Right Power for Specific Materials and Thicknesses
Selecting the appropriate laser cutter power involves considering several factors such as material type, thickness, desired finish, and the specific capabilities of the laser cutter.
Thin Materials
For materials like paper, cardboard, and thin plastics, a laser cutter power between 20W to 100W is generally sufficient. Higher power levels may cause burning or melting of these delicate materials. CO2 laser cutters are typically recommended for these applications due to their effectiveness in handling non-metallic materials.
Thick Materials
When working with thicker materials such as metals, the required laser cutter power varies based on thickness:
- For materials up to 1/4 inch, a power range of 100W to 500W is suitable.
- For materials up to 1 inch, consider using lasers in the 500W to 2000W range.
For deep cuts in thick metals, fiber laser cutters are often the best solution due to their efficiency and precision.
Examples of Applications and Ideal Laser Cutter Power
Different industries utilize various types of laser cutters based on their specific needs:
- Small Business Laser Cutters: Typically require a power range of 20W to 500W, which is compact yet versatile enough for small-scale projects.
- Industrial Laser Cutters: Large manufacturing units that prioritize speed and precision often use higher-powered machines ranging from 500W to 10,000W. Fiber lasers are commonly employed in these settings due to their ability to handle complex tasks efficiently.
- Custom Laser Cutter Solutions: For DIY projects, a range of 20W to 500W is usually adequate. However, the exact choice depends on individual project requirements and material specifications.
Selecting the right laser cutter power is critical for optimizing performance across various applications. By understanding material types, thicknesses, and desired outcomes, you can make informed decisions that enhance efficiency and quality in your cutting projects. At OPMT Laser, we provide expert guidance to help you choose the ideal laser cutter tailored to your specific needs.
Understanding Laser Cutter Power and Speed
In laser cutting, two fundamental parameters are critical: power and cutting speed. Power refers to the energy output of the laser beam per unit time, while cutting speed indicates how quickly the laser moves across the material being cut.
The Interdependence of Power and Speed
While power and speed are technically independent variables, they are closely related in practice. Adjusting one often requires a corresponding change in the other to maintain optimal cutting performance. For example, a high-powered laser generates more energy per second. If this type of laser operates at a low cutting speed, it risks overheating and damaging the workpiece unless a deep cut is desired. Conversely, higher power typically necessitates higher cutting speeds to prevent excessive heat buildup.
Optimizing Settings for Various Applications
To achieve the best results in laser cutting, it’s essential to optimize both power and speed settings based on the material type and thickness. Here are some guidelines:
- Thin Materials (e.g., paper, cardboard):
- Power: Low (10-30%)
- Speed: High (200-400 mm/s) to prevent burning.
- Thick Materials (e.g., metals):
- Power: High (80-100%)
- Speed: Low (0.1-2 mm/s) for clean cuts.
- Engraving Applications:
- Power: Low to Moderate (10-40%)
- Speed: High (100-300 mm/s) for shallow engravings.
- High-Quality Cutting:
- Power: Medium (50-80%)
- Speed: Moderate for a balance between precision and efficiency.
Key Considerations for Laser Cutting
When setting up a laser cutter, consider these factors:
- Material Characteristics: Different materials absorb laser energy differently, requiring specific adjustments in power and speed.
- Desired Cut Quality: For precision cuts, slower speeds with lower power may be necessary to achieve clean edges without burning.
- Testing and Calibration: Start with manufacturer-recommended settings for specific materials, and conduct test cuts to fine-tune parameters based on performance.
By understanding the intricate relationship between power and speed in laser cutting, operators can make informed adjustments to optimize their processes, ensuring high-quality results tailored to their specific applications.
What Is Laser Cutter Power Density?
Laser cutter power density is a key factor that determines the efficiency and effectiveness of laser cutting machines. It quantifies the amount of laser power delivered to a specific area of material being processed. This measurement is crucial because it directly influences both the speed and quality of the cuts made by the laser.
Mathematically, power density is defined as the ratio of laser power to the cross-sectional area or spot size of the laser beam, expressed in watts per square millimeter (W/mm²). The formula for calculating power density is:
$$
\text{Power Density} = \frac{\text{Power}}{\pi \times \left(\frac{\text{Spot Size}}{2}\right)^2}
$$
For instance, if a laser cutter operates at 500 watts with a spot size of 0.2 mm, the power density would be approximately 198,943 W/mm². This high power density indicates that the laser can effectively cut through materials with precision and speed.
Applications Requiring High Laser Cutter Power Density
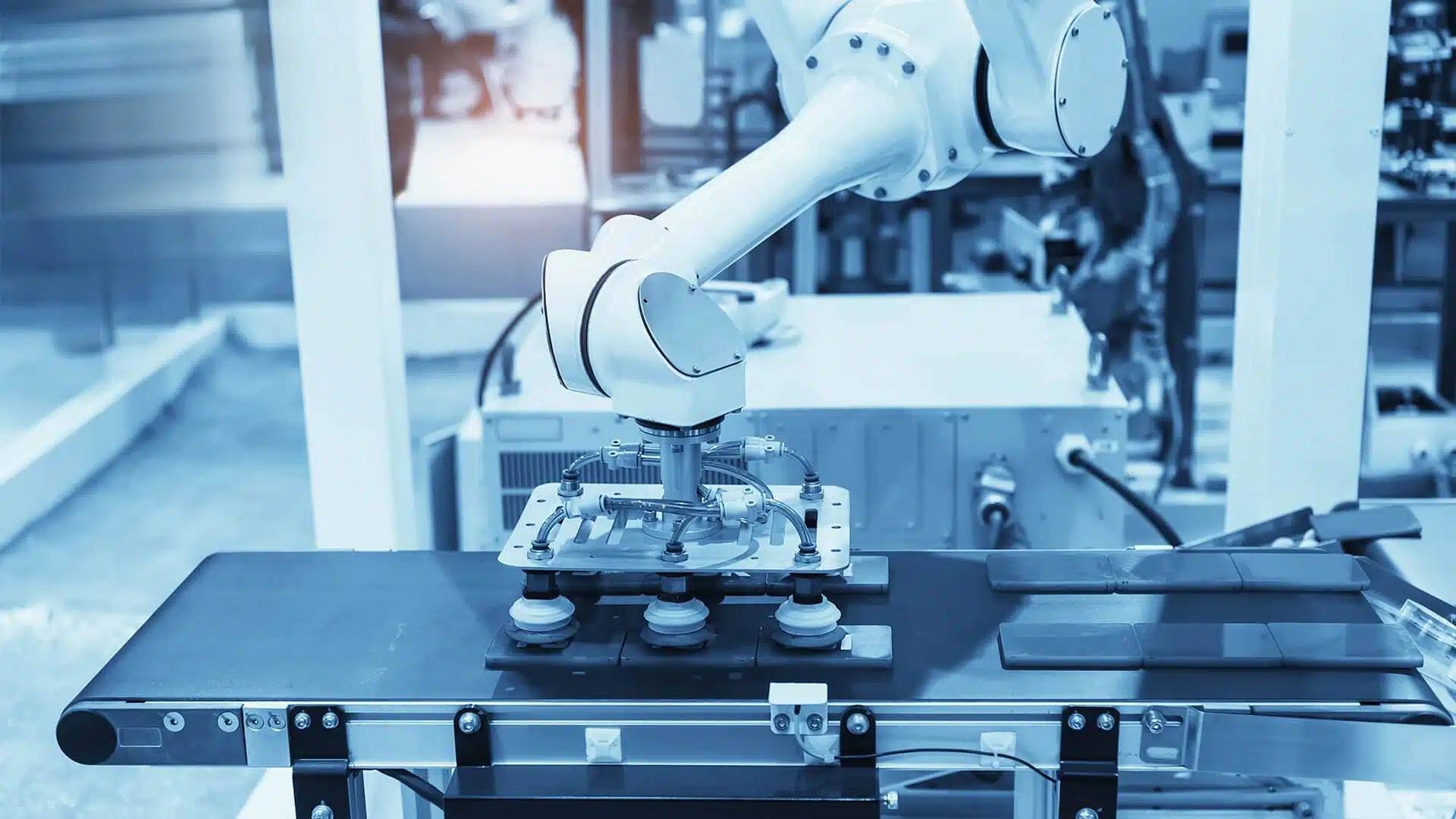
High laser cutter power density is essential in various applications where precision and quick processing are paramount. Here are some notable areas where this capability is utilized:
- Metal Cutting: Metals often require higher energy densities for effective cutting due to their strength. A higher power density allows the laser to melt and vaporize metal quickly, resulting in clean and precise cuts. Industries such as manufacturing heavily rely on this technology for producing components.
- Deep Cutting: For thick materials, lasers must penetrate deeply and swiftly to create clean cuts. High-powered lasers are specifically designed for these applications, ensuring efficiency and accuracy.
- Medical Device Manufacturing: In producing medical devices like stents and surgical instruments, high power density enables precise cutting and shaping of delicate materials. This precision is critical for ensuring the functionality and safety of medical devices.
By leveraging high power density, manufacturers can enhance productivity while maintaining high standards of quality in their products. OPMT Laser’s innovative CNC systems and laser processing solutions are designed to optimize these parameters, ensuring users achieve optimal results in their cutting applications. For more information on our advanced laser solutions, explore our product offerings such as Micro3D L530V and LP550V.
What Should You Consider When Choosing a Cutting Machine of Different Power?
When selecting a cutting machine with varying power, several critical factors come into play, including material type and thickness, cutting speed, and precision requirements. Understanding these elements ensures that you choose the right machine for your specific needs.
Material Type and Thickness
Different materials exhibit unique cutting properties, necessitating specific laser cutters and power levels. For instance, thicker materials demand higher-powered laser cutters, while thinner materials can be effectively processed with lower power options. It is crucial to select a laser-cutting machine that is tailored to the material type you intend to work with. For example, if your projects involve metal, consider specialized machines like the OPMT Laser LP550V designed explicitly for metal cutting.
Cutting Speed
The cutting speed refers to how quickly the laser cutter traverses the material being processed. While higher power may allow for increased speed, it is vital to balance this with the quality of the cut. A faster cutting speed can lead to reduced precision if not managed correctly. Therefore, understanding the optimal speed for your chosen material and desired finish is essential.
Precision Requirements
Precision is another significant factor when choosing a cutting machine. The level of detail required in your cuts will influence both the speed and power settings of your laser cutter. Typically, higher precision requires slower speeds and more power. Conversely, if your project tolerates lower precision, you may opt for faster speeds with less power. This balance is crucial for achieving the best results tailored to your specific applications.
Cost Considerations
Cost plays a vital role in establishing a laser-cutting setup. Generally, high-powered lasers come at a premium compared to lower-powered alternatives. Additionally, fiber laser machines often have a higher price point than CO2 models due to their advanced capabilities and efficiencies. When budgeting for your cutting machine, factor in not only the initial purchase price but also long-term operational costs associated with maintenance and consumables.
Selecting the right cutting machine involves careful consideration of various factors such as material type, thickness, cutting speed, precision requirements, and cost. By understanding these elements, you can make an informed decision that aligns with your operational needs and budget constraints. For more information on specific products that suit different applications, explore our offerings at OPMT Laser.
Common Misconceptions about Laser Cutter Power
More Power Is Always Better
One of the most common misconceptions is that higher power always leads to better cutting results. This is misleading. The effectiveness of a laser cutter is highly dependent on the material being processed. For example, using a high-powered fiber laser to cut paper or wood is unnecessary and inefficient—imagine trying to slice an apple with a saw instead of a knife. Selecting the right power level tailored to the specific material ensures optimal performance and cost-effectiveness. Understanding your project’s requirements is essential for making informed choices regarding laser cutter power.
Higher Power Means Faster Cutting Speeds
Another prevalent belief is that increased power directly translates to faster cutting speeds. However, this isn’t always accurate. While higher-powered lasers can achieve quicker cuts under certain conditions, the relationship between power and speed is not straightforward. It’s crucial to adjust the cutting speed based on the material type and thickness, as well as the desired finish quality. Sometimes, a lower power setting with an appropriate speed adjustment can yield better results without compromising efficiency.
High-Power Lasers Can Cut Any Material Thickness
Many users mistakenly think that high-powered lasers can cut through any thickness of material effortlessly. While powerful lasers are necessary for cutting thicker metals, they are not universally effective across all materials and thicknesses. Each laser cutter has specific limitations regarding the thickness it can handle effectively. For instance, a machine designed for cutting stainless steel may have a maximum thickness it can manage efficiently. Always consult the manufacturer’s guidelines or product manuals to determine the appropriate capabilities of your laser cutter.
What Should You Consider When Using Laser Cutters?
Laser cutters are powerful tools that offer precision and efficiency in cutting various materials. However, they also pose significant hazards if not used properly. Understanding the risks and implementing safety measures is crucial for anyone operating these machines.
Potential Hazards of Laser Cutting
- Eye Damage: The intense laser beam can cause severe eye injuries, including permanent blindness. Operators must wear appropriate laser safety glasses to protect against harmful radiation.
- Fire Risks: Laser cutters generate substantial heat, leading to a fire hazard, especially when cutting flammable materials. Operators should always monitor the machine during operation and keep the work area free of combustible materials.
- Skin and Respiratory Issues: The cutting process produces smoke and toxic fumes that can irritate the skin and respiratory system. Proper ventilation and the use of masks are essential to minimize exposure to harmful substances.
Safety Measures to Implement
To mitigate these risks, consider the following safety protocols:
- Establish Standard Operating Procedures (SOPs): Create detailed SOPs for each laser cutter model, ensuring that all operators are trained on safety equipment usage and emergency handling.
- Regular Equipment Maintenance: Ensure that all laser cutting machines are regularly maintained, including cleaning, calibration, and repairs of any worn or broken parts.
- Material Selection: Operators should carefully choose materials for cutting. Avoid using flammable or toxic materials that could release harmful fumes or increase fire risk.
- Protective Gear: All operators must wear appropriate personal protective equipment (PPE), including safety glasses, gloves, and masks, to safeguard against potential hazards.
Best Practices for Safe Operation
- Training: Ensure all operators receive comprehensive training on the machine’s operation and associated hazards. Regular refresher courses can reinforce safe practices.
- Supervision: Never leave a laser cutter unattended while in operation. Continuous supervision allows for immediate response in case of an emergency.
- Clean Workspace: Maintain a clean work environment by regularly removing debris and flammable materials from around the laser cutter.
- Emergency Preparedness: Keep a properly maintained fire extinguisher nearby and ensure all operators know how to use it effectively.
- Ventilation Systems: Install effective ventilation systems to remove harmful fumes generated during cutting operations. Regularly check that these systems are functioning correctly.
How to Maintain Laser Cutters: Essential Practices
Maintaining laser cutters is vital for ensuring their efficiency and longevity. Regular maintenance not only enhances performance but also minimizes downtime and repair costs. Here’s a detailed guide to keeping your laser cutting equipment in optimal condition.
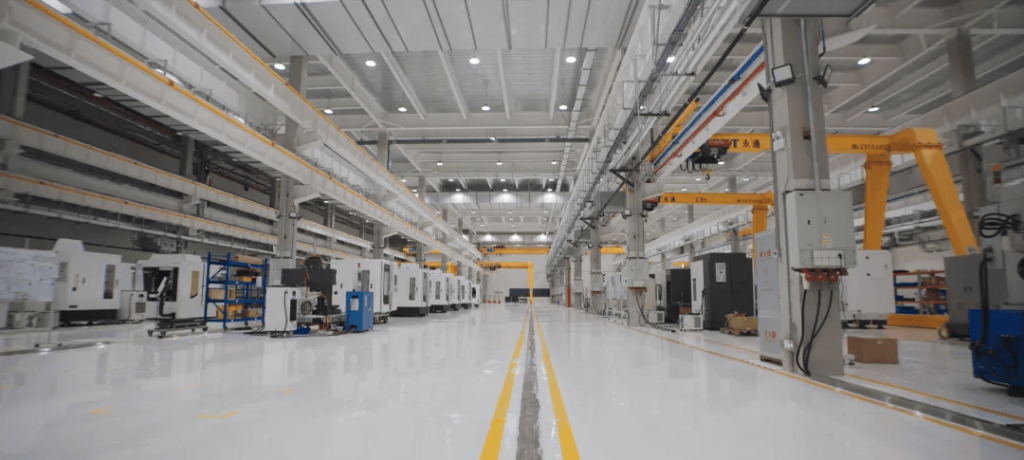
Importance of Regular Maintenance
Why is maintenance crucial for laser cutters? Consistent upkeep helps prevent unexpected breakdowns, ensuring that your operations run smoothly. By adhering to a structured maintenance routine, you can significantly extend the lifespan of your equipment and improve cutting quality.
Key Maintenance Practices
- Clean Lenses and Mirrors Frequently: The lenses and mirrors of laser cutters are susceptible to dust and debris, which can impair performance. Regularly clean these components using a soft cloth and a gentle cleaning solution. This simple task can dramatically enhance the quality of your cuts.
- Inspect Optical Components for Damage: Regular inspections of optical components are essential. Look for signs of wear or damage, such as scratches or discoloration on mirrors and lenses. If any issues are found, replace the damaged parts immediately to maintain cutting precision.
- Ensure Proper Alignment: Misalignment can lead to inaccurate cuts and wasted materials. Regularly check and adjust the alignment of your laser cutter to ensure that the beam focuses correctly on the material being processed.
- Conduct Routine Maintenance Checks: Establish a Standard Operating Procedure (SOP) for routine checks. Schedule professional inspections at regular intervals to assess all machine components, replacing worn parts as necessary. This proactive approach can prevent larger issues down the line.
Additional Best Practices
- Lubricate Moving Parts: Proper lubrication of moving components is crucial for smooth operation. Ensure that all bearings, rails, and gears are adequately lubricated according to the manufacturer’s guidelines.
- Monitor Cooling Systems: A well-functioning cooling system is vital for maintaining optimal operating temperatures during cutting processes. Regularly check coolant levels and inspect for leaks to ensure effective cooling.
- Keep the Work Area Clean: A tidy workspace helps prevent contamination of your laser cutter. Regularly remove debris from around the machine to maintain a safe and efficient working environment.
Maintenance Schedule Overview
To effectively manage maintenance tasks, consider implementing a structured schedule:
- Daily Tasks:
- Clean lenses and mirrors.
- Remove debris from the cutting bed.
- Check coolant levels.
- Weekly Tasks:
- Inspect optical components.
- Lubricate moving parts.
- Verify alignment.
- Monthly Tasks:
- Replace filters in cooling systems.
- Conduct thorough internal cleaning.
- Schedule professional maintenance if required.
- Annual Tasks:
- Perform a comprehensive inspection by a qualified technician.
- Replace major components showing signs of wear.
Emerging Trends in Laser Cutter Power
Laser technology has transformed the manufacturing landscape over the past few decades, continuously evolving to meet modern demands. As industries embrace innovation, laser-cutting machinery is becoming more advanced, enhancing efficiency and precision in various applications. This article highlights the latest trends that are shaping the future of laser cutter power, with a focus on OPMT Laser’s commitment to providing innovative CNC systems and laser processing solutions.
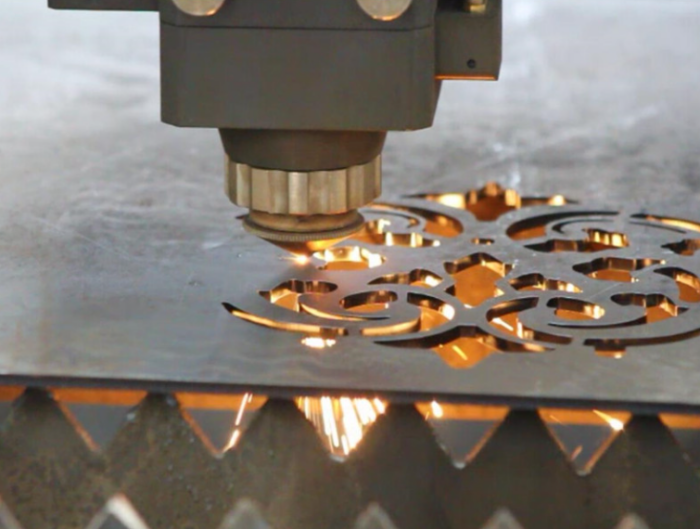
Integration with Automation Systems
The integration of automation systems in laser cutting is revolutionizing the industry. By incorporating robotics, laser cutters can now execute precise cuts with minimal human intervention. This advancement not only streamlines production but also reduces labor costs. For instance, automated laser-cutting solutions developed by OPMT Laser allow manufacturers to program specific shapes and designs efficiently, enhancing overall productivity.
Advanced Control and Monitoring Features
Modern laser cutters are equipped with advanced control and monitoring features that significantly improve operational efficiency. Real-time monitoring capabilities enable operators to track critical data remotely, ensuring optimal performance at all times. Additionally, cloud connectivity and intelligent material detection facilitate immediate adjustments during the cutting process. These innovations empower manufacturers to maintain high-quality standards while minimizing downtime.
Integration with CAD Software
The seamless integration of laser cutters with Computer-Aided Design (CAD) software is another trend gaining traction. This integration allows designers to create intricate designs that can be sent directly to the laser cutter, saving time and increasing accuracy. With tools like OPMT Laser’s cutting-edge systems, manufacturers can streamline their workflow from design to production, ensuring that every detail is executed flawlessly.
Adoption of Ultrafast Lasers
Ultrafast lasers are emerging as a game-changer in the industry due to their ability to deliver high precision with minimal heat-affected zones. These lasers are particularly advantageous for applications that require intricate cuts in sensitive materials. By reducing thermal impact, ultrafast lasers ensure cleaner cuts and less material wastage, aligning with sustainability goals in manufacturing.
Hybrid Laser Cutting Systems
The development of hybrid laser cutting systems is enhancing flexibility in manufacturing processes. By combining different types of lasers—such as fiber and CO2—these systems optimize performance based on material type and thickness. This adaptability allows manufacturers to tackle a broader range of applications while maximizing efficiency and quality.
Increased Energy Efficiency
As environmental concerns rise, energy efficiency is becoming a priority for laser cutting technology. Modern fiber lasers consume significantly less energy than traditional CO2 lasers while providing superior cutting speeds. This shift not only reduces operational costs but also contributes to global sustainability efforts by minimizing the carbon footprint of manufacturing processes.
AI-Powered Optimization
Artificial Intelligence (AI) is playing a pivotal role in optimizing laser cutting operations. AI algorithms can analyze material characteristics and adjust cutting parameters in real-time, enhancing productivity while reducing waste. By leveraging AI technology, manufacturers can achieve higher levels of efficiency and precision in their cutting processes.
By staying at the forefront of these emerging trends, OPMT Laser continues to provide innovative solutions that meet the evolving needs of the manufacturing industry. Explore our range of products like the LP550V or Micro3D-L570V to discover how we can elevate your production capabilities today!
Conclusion
Selecting the right laser cutter power for your specific applications is essential for achieving outstanding results. You may be grappling with the complexities of material types, thicknesses, and precision requirements, but understanding these factors can significantly enhance your cutting experience. Did you know that laser cutters can operate anywhere from 10W for delicate materials to over 6000W for heavy-duty tasks?
At OPMT Laser, we promise to guide you through this process, offering a diverse range of laser cutting machines tailored to meet your needs—from CO2 to fiber lasers. Our expertise ensures you make informed choices that align with your project requirements.
Explore our offerings and discover how OPMT Laser can elevate your cutting capabilities today!
Disclaimer
This content is compiled by OPMT Laser based on publicly available information for reference only; mentions of third-party brands and products are for objective comparison and do not imply any commercial association or endorsement.