Evolution of Lab-Grown Diamond Manufacturing
Have you witnessed how dramatically the synthetic diamond industry has transformed in recent years? Lab-grown diamonds, produced through High-Pressure High-Temperature (HPHT) and Chemical Vapor Deposition (CVD) methods, have revolutionized the diamond market with their sustainable production and identical physical properties to natural diamonds. HPHT excels in producing industrial-grade diamonds for cutting tools, while CVD enables larger, high-purity crystals ideal for electronics and optics applications. With the lab-grown diamond industry projected to reach $29.5 billion by 2029, manufacturers are seeking more efficient processing technologies to meet growing demand.
Traditional diamond processing methods face significant challenges. Electrolytic grinding and Electrical Discharge Machining (EDM) struggle with precision, especially when working with complex geometries and non-conductive CVD materials. These limitations have spurred innovation in processing technology, including shorter growth cycles and higher-quality production through automated systems. Furthermore, modern diamond manufacturing facilities are increasingly adopting renewable energy systems to minimize their environmental footprint, aligning with the growing consumer demand for sustainable luxury products.
Technical Limitations of Conventional EDM Processing
Why do traditional EDM methods fall short when processing lab-grown diamonds? EDM’s dependency on electrical conductivity creates serious wire skipping issues when machining polycrystalline diamonds with inconsistent conductivity patterns. This unreliable performance leads to incomplete cuts and frequent workpiece rejection, particularly problematic when processing valuable lab-grown diamond materials. Moreover, the thermal stress generated during EDM processing induces micro-cracks and edge chipping, reducing tool lifespan by up to 30% and compromising the structural integrity of the finished product.
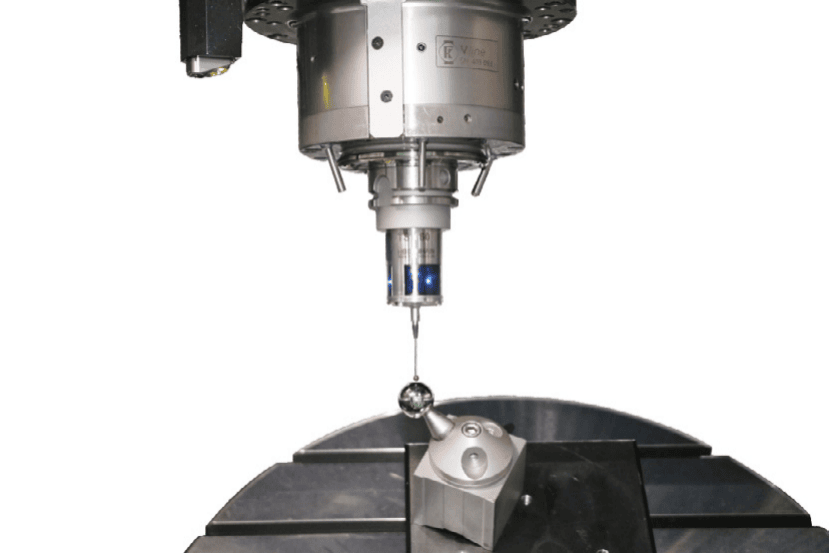
The efficiency constraints of conventional EDM are equally concerning for manufacturers. With an average processing speed of only 1.5 mm/min for diamond materials, EDM becomes economically unviable for large-curvature surfaces or intricate contours. Additionally, when processing large particles or polycrystalline diamond with poor conductivity, traditional EDM machines often experience wire skipping issues that make continued machining impossible, resulting in production delays and increased costs. These limitations have created an urgent need for alternative processing technologies that can deliver both precision and efficiency for lab-grown diamond manufacturing.
Advanced 5-Axis Laser Solutions for Diamond Processing
How are 5-axis laser systems transforming diamond processing? OPMT Laser’s advanced machining centers, including the Micro3D L530V five-axis femtosecond laser system, deliver unparalleled precision with consistent accuracy of ≤0.003 mm for edge profiles and relief angles. This remarkable precision enables manufacturers to achieve complex geometries and intricate details that were previously impossible with conventional methods. The system’s RTCP (Rotational Tool Center Point) functionality enables simultaneous 5-axis machining of complex geometries, including undercuts and negative chamfers, essential for creating the perfect facets that define high-quality diamonds.
Feature | Traditional EDM | OPMT 5-Axis Laser | Improvement |
---|---|---|---|
Processing Speed | 1.5 mm/min | 3.0 mm/min | 100% faster |
Accuracy | ≥0.015 mm | ≤0.005 mm | 3x better |
Material Flexibility | Conductive only | All materials | Expanded capability |
Heat Affected Zone | Significant | Minimal (<5μm with femtosecond) | Superior quality |
The non-contact nature of laser processing eliminates tool wear and handles non-conductive materials like pure CVD diamonds without edge degradation. This capability is particularly valuable when working with the Light 5X 40V vertical machining center, which processes PCD tools at speeds up to 3.0 mm/min, reducing cycle times by 50–70% compared to EDM. Additionally, the femtosecond laser technology available on select OPMT systems achieves remarkable 0.08μm surface roughness on precision components-a tenfold improvement over conventional methods. This “cold processing” approach is particularly valuable for preserving the optical and structural properties of lab-grown diamonds.
Cost-Efficiency Analysis: Laser vs. Traditional Methods
What makes 5-axis laser technology economically superior for diamond processing? A comprehensive comparison between laser systems and traditional EDM reveals substantial cost savings across multiple metrics. Operational expenses are reduced by 53%, with monthly costs of ¥1,956 for laser systems compared to ¥4,190 for EDM, driven by lower energy consumption (2.5 kWh/h vs. 4.5 kWh/h) and elimination of consumables like copper wheels. These savings significantly impact the total cost of ownership over the machine’s lifespan.
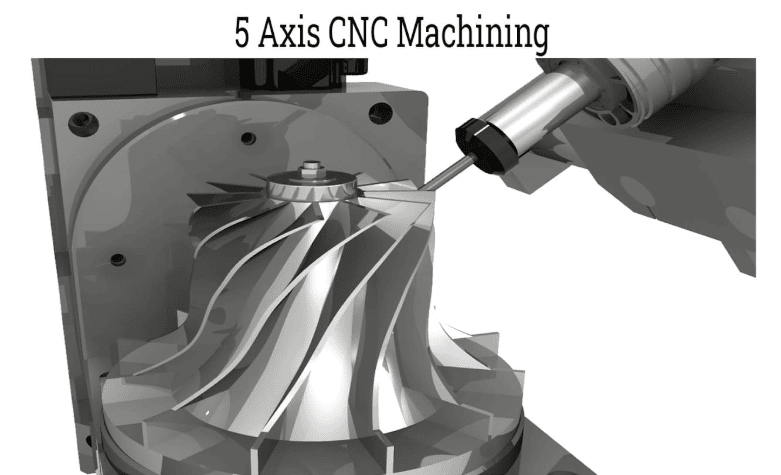
Production throughput sees dramatic improvements with 5-axis laser technology. For example, laser machines complete a 500-mm diameter saw blade in just 8 hours versus 24 hours for EDM, effectively tripling output capacity. The quality improvements are equally impressive, with laser-processed tools exhibiting ≤0.005 mm profile deviations compared to ≥0.015 mm for EDM, extending service life by 40%. Beyond direct financial benefits, laser-based diamond processing offers significant environmental advantages by eliminating cutting fluids and reducing floor space requirements by 40% (6 m² vs. 10 m²).
A manufacturer of PCD contour cutters for 3C electronics achieved 0.00465 mm passivation accuracy using an OPMT Laser system, eliminating post-processing steps and reducing per-unit costs by 32%. This case study demonstrates how the investment in advanced 5-axis laser technology delivers tangible returns through improved precision, enhanced productivity, and significant cost reduction. For businesses looking to maintain competitive advantages in the rapidly growing lab-grown diamond market, where precision directly impacts final gem quality and value, OPMT Laser’s solutions provide the technological edge necessary for success.
Disclaimer
This content is compiled by OPMT Laser based on publicly available information for reference only; mentions of third-party brands and products are for objective comparison and do not imply any commercial association or endorsement.