Lab-grown diamond manufacturing has undergone a remarkable transformation in 2025, with 5-axis CNC laser technology emerging as the definitive solution for precision cutting challenges. Traditional processing methods like electrical discharge machining (EDM) and grinding frequently lead to quality degradation of cutting edges, affecting both accuracy and efficiency. OPMT Laser’s advanced 5-axis CNC systems have effectively addressed these limitations, achieving unprecedented precision levels of ±0.003 mm while maintaining stability at 0.001 mm—essential requirements for producing gem-quality lab-grown diamonds.
Why does this matter? The lab-grown diamond industry is projected to reach $29.5 billion by 2029, and manufacturers require solutions that eliminate the chips and cracks that frequently occur during traditional processing methods. These defects increase costs and production times, sometimes requiring complete blade replacement. Additionally, when processing large particles or polycrystalline diamond with poor conductivity, traditional EDM machines often experience wire skipping issues that make continued machining impossible.
The revolution in diamond cutting technology isn’t merely incremental—OPMT’s Light 5X series vertical machining centers deliver 200% faster processing speeds and 50% lower costs per unit compared to traditional EDM methods, fundamentally changing the economics of lab-grown diamond production. This advancement has proven particularly valuable for manufacturers seeking competitive advantages in the growing lab-grown diamond market, where precision directly impacts final gem quality and value.
Core Technologies Driving Modern Diamond Cutting Machines
Advanced 5-Axis CNC Systems
The foundation of modern diamond processing lies in sophisticated 5-axis CNC laser machines. OPMT’s Light 5X 40V exemplifies this technology, featuring highly dynamic 5-axis precision with linear drives. These machines utilize linear motors combined with roller guides for the X, Y, and Z axes, offering rapid response times and high positioning accuracy of 0.005 mm (5 microns).
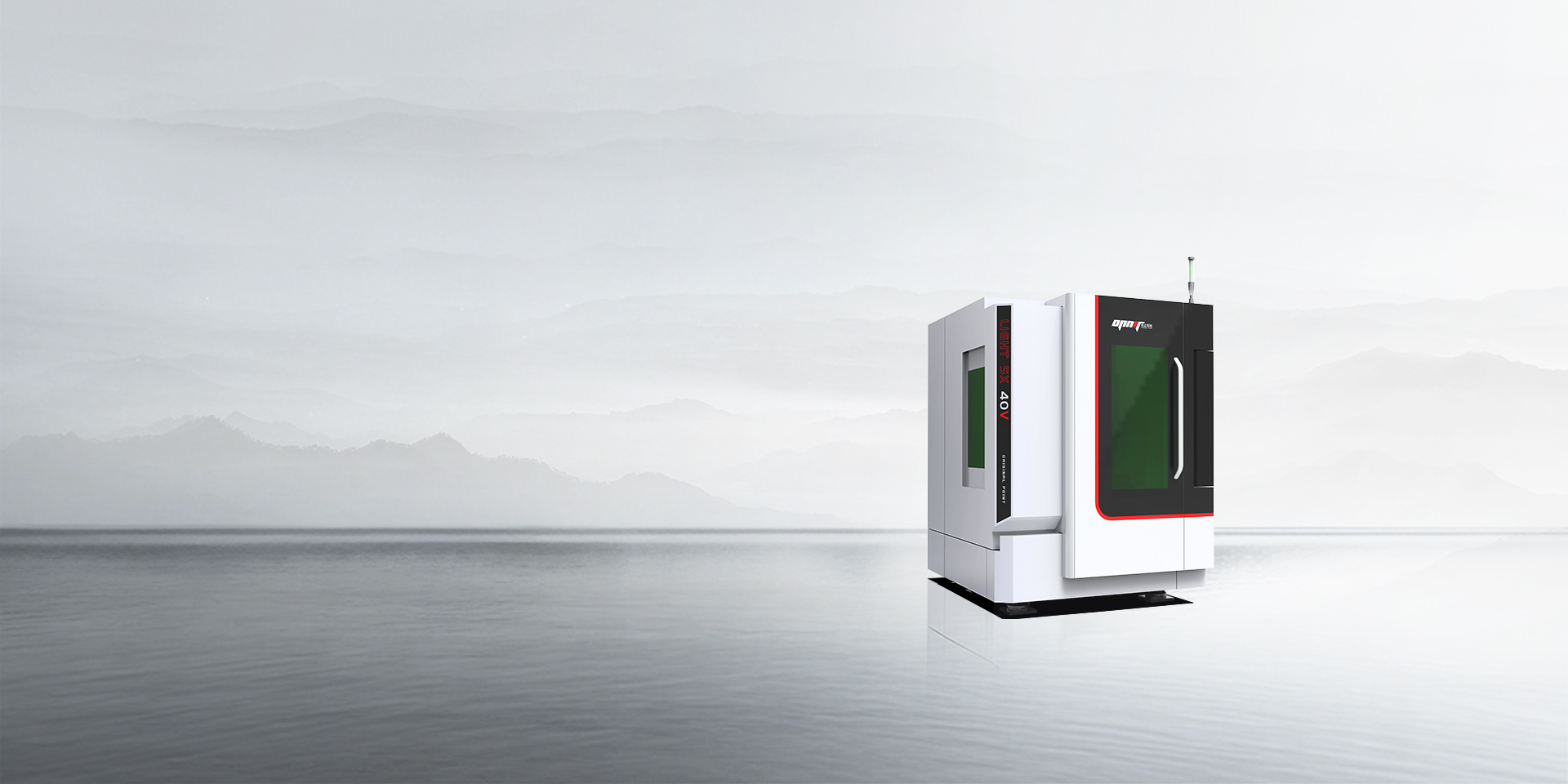
What makes these systems uniquely suited for lab-grown diamond processing? The key technological breakthroughs include:
- Highly dynamic linear axes: Using linear motors for fast dynamic response without direct contact, minimizing wear in drive systems
- Closed-loop control: All linear axes adopt closed-loop grating scale detection for high positioning accuracy
- Linear rolling guide rails: Providing low friction coefficient and fast response
- Torque motors: High-precision torque motors for rotation axes (B and C axes)
The B-axis swing angle of 120° on the Light 5X 40V model enables complex geometric processing essential for intricate diamond cuts, while the Light 5X 60V offers enhanced capabilities with larger workpiece capacity up to 200 mm in diameter.
Revolutionary Laser Technologies
The choice of laser technology dramatically impacts diamond processing outcomes, with OPMT offering three distinct options:
Laser Type | Pulse Width | Primary Applications | Benefits for Diamond Processing |
---|---|---|---|
Nanosecond (ns) | 1-200 ns | Roughing operations | Cost-efficient bulk material removal at $50-80/hour operational cost |
Picosecond (ps) | 1-200 ps | Fine finishing | Reduced heat-affected zone (15-30μm in titanium) |
Femtosecond (fs) | <1 ps | Ultra-precision machining | Virtually no thermal damage (<5μm HAZ), extends tool lifespan 3× |
The femtosecond laser capability available on OPMT’s Micro3D L530V achieves remarkable 0.08μm surface roughness on precision components—a 10× improvement over conventional methods. This “cold processing” approach is particularly valuable for lab-grown diamonds, where thermal damage must be minimized to preserve optical and structural properties.
RTCP 5-Axis Linkage Technology
A critical advancement in diamond processing is RTCP (Rotation Tool Center Point) 5-axis linkage technology. This capability allows machines to maintain precise tool positioning relative to the workpiece while executing complex multi-axis movements essential for creating the intricate facets that define high-quality diamonds.
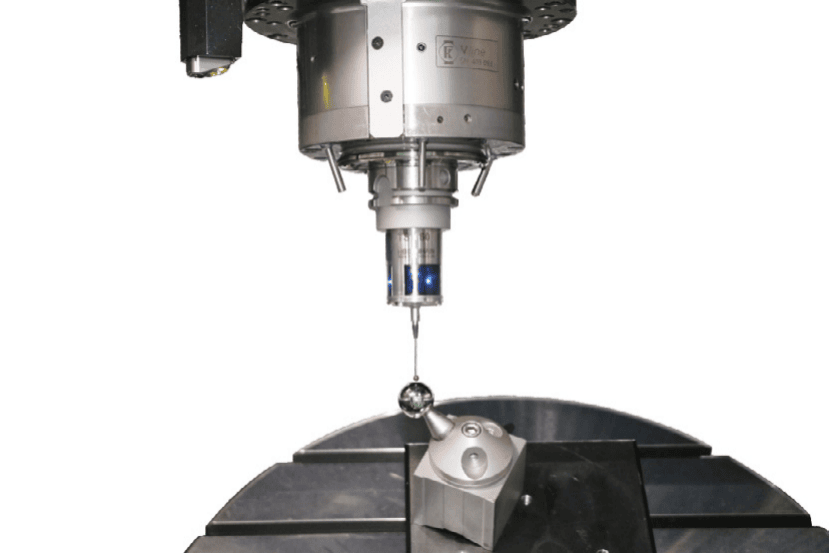
The NUM CNC control system in OPMT machines supports up to 32 axes/spindles per NCK (Numerical Control Kernel), with up to 200+ axes/spindles possible in a complete system. This open universal CNC system accommodates various operations including turning, milling, grinding, and laser processing within a single setup—dramatically reducing cumulative errors that occur when diamonds require multiple processing steps.
Case Study: Achieving ±0.003 mm Tolerances in Jewelry-Grade Diamonds
Technical Implementation and Performance
The ability to achieve ±0.003 mm tolerances represents a breakthrough in lab-grown diamond processing. OPMT’s L320V vertical laser machining center demonstrates this capability through several technical innovations:
- Natural marble machine structure for stability, rigidity, and accuracy retention
- Linear motor-driven axes for fast response and high precision
- Positioning accuracy of 0.005 mm and repeat positioning accuracy of 0.003 mm
- Processing capabilities for tools with diameters between 80-300 mm
When comparing actual production scenarios, the advantages become clear. For a trapezoidal flat tooth saw blade (diameter 500 mm, 120 teeth), average processing time using traditional EDM is 24 hours, whereas with laser CNC machining, this reduces to only 8 hours—representing a 3× improvement in production efficiency.
Economic and Environmental Impact
The economic comparison between traditional EDM processing and 5-axis laser cutting reveals substantial benefits:
Application | EDM Machines | 5-Axis Laser CNC | Savings |
---|---|---|---|
Floor space required | 10 m² | 6 m² | 40% reduction |
Electricity consumption | 4.5 kWh/hour | 2.5 kWh/hour | 44% reduction |
Total monthly cost | 4,190 Yuan | 1,956 Yuan | 53% reduction |
Beyond direct cost advantages, laser-based diamond processing offers significant environmental benefits by eliminating the need for cutting fluids and reducing energy consumption by 25%. For manufacturers focused on sustainable production methods, this represents a compelling advantage that aligns with increasing consumer demand for environmentally responsible luxury goods.
Industry Standards and Certification Requirements
Quality and Environmental Management Systems
The precision diamond manufacturing industry adheres to rigorous standards, particularly for applications in aerospace, automotive, and medical sectors. OPMT machines have obtained multiple certifications essential for manufacturers serving these high-standards industries:
- RoHS certification for restriction of hazardous substances
- ISO 14001 environmental management system certification
- ISO 45001 occupational health and safety management system certification
These certifications ensure that diamond processing operations meet international standards for quality, environmental impact, and workplace safety—increasingly important considerations for jewelry manufacturers targeting environmentally conscious consumers in 2025.
Safety Features and Operational Excellence
Modern laser diamond processing equipment incorporates numerous safety features designed to protect operators while maximizing productivity:
- Dedicated protective glass: Prevents burns from laser light sources while facilitating process monitoring
- Laser CNC machine tool safety lock devices: Improve operator and maintenance personnel safety
- Ergonomic structural design: Operator adjustment space within 1.6 m from the ground for comfortable operation
Each OPMT machine undergoes extensive testing to maintain high precision and reliability, including X, Y, Z-axis parallelism accuracy detection, B, C-axis parallelism accuracy detection, precision line parallelism accuracy detection, ballbar testing, alignment laser verification, rotary axis calibration, laser beam profiler analysis, and laser interferometer measurement.
Future Trends: AI-Driven CNC Systems for Custom Diamond Designs
Intelligent Manufacturing Integration
As the lab-grown diamond industry continues to evolve, AI-driven systems are transforming production capabilities. OPMT Laser’s approach of combining high-end CNC systems with laser technology points toward increasingly integrated intelligent manufacturing solutions under their vision of “making manufacturing smarter and intelligent manufacturing easier”.
How is this manifesting in real-world applications? The 2025 innovation in OPMT’s Light 5X 40V incorporates AI-error correction that reduces scrap rates to less than 1%—a dramatic improvement over traditional manual calibration errors that cause 8–12% scrap rates in conventional diamond processing. This translates to a 95% first-pass success rate, critical for maximizing yield when working with valuable lab-grown diamond materials.
Advanced Software and Measurement Integration
User-friendly software platforms are becoming integral to diamond processing workflows, with systems that simplify the transition from design to finished product:
- GTR cutting tools software: Facilitates transition from EDM to laser machining with minimal training required
- 3D machining path planning CAM software: Enables importation of existing EDM projects, automatic 3D measurement of PCD surfaces, automatic program generation, and 3D simulation directly at the machine
The integration of measurement technologies directly into processing machines further enhances precision, with ZOLLER presetting and measuring machines for tool verification, laser microscopy for surface analysis, and high-precision probes for automatic correction of positioning errors.
In 2025, the trend toward greater customization is evident in both machine design and application flexibility, with modular construction allowing for system scaling to different models, flexible machining of various ultrahard materials (PCD, PCBN, CVD), and quick switching between different processing tasks. This enables manufacturers to adapt rapidly to changing market demands, particularly important in the fashion-driven jewelry industry.
For manufacturers considering investment in advanced diamond processing technology, OPMT’s nanosecond vs. picosecond vs. femtosecond laser guide provides detailed comparison information to help determine the optimal configuration based on specific precision requirements, production volume, and material types.
Disclaimer
This content is compiled by OPMT Laser based on publicly available information for reference only; mentions of third-party brands and products are for objective comparison and do not imply any commercial association or endorsement.