In the ever-evolving landscape of manufacturing technology, a groundbreaking innovation is reshaping the production of carbide inserts: femtosecond laser processing. This cutting-edge technique is not just an incremental improvement; it’s a quantum leap in precision engineering that promises to redefine the boundaries of tool performance and durability.
The Science Behind the Precision
Femtosecond laser processing harnesses the power of ultrashort pulse lasers to achieve unprecedented levels of accuracy in material manipulation. At its core, this technology relies on two fundamental mechanisms:
- Light transmission
- Light explosion
During the process, computer-controlled femtosecond laser pulses are focused with pinpoint accuracy on the surface or within the material. This triggers a light explosion effect, enabling precise material removal at a scale previously thought impossible.
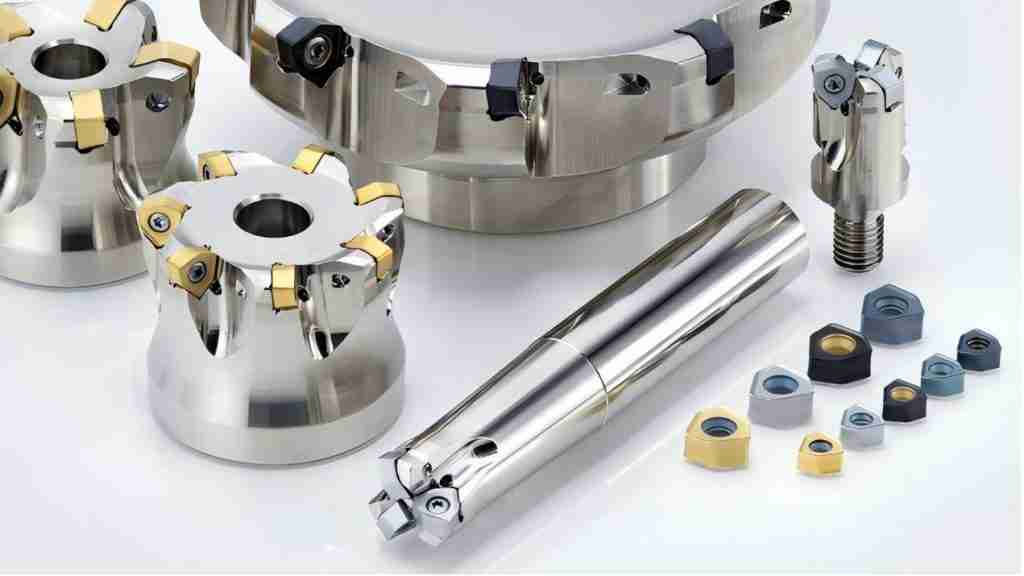
Carbide Inserts: The Unsung Heroes of Manufacturing
Before delving deeper into the processing technology, it’s crucial to understand the significance of carbide inserts themselves. These small but mighty components are the workhorses of the manufacturing industry, boasting an impressive array of properties:
- High hardness
- Exceptional wear resistance
- Impressive strength and toughness
- Heat and corrosion resistance
What sets carbide inserts apart is their ability to maintain these properties even under extreme temperatures, making them indispensable in modern manufacturing processes.
Femtosecond Laser Processing: A Game-Changer for Carbide Inserts
Surface Texturing: Microscopic Enhancements, Macroscopic Impact
One of the most exciting applications of femtosecond laser processing is surface texturing. By creating intricate microstructures on carbide insert surfaces, manufacturers can:
- Improve wetting characteristics
- Enhance heat transfer and cooling
- Optimize lubrication conditions
- Reduce chip accumulation and scaling
- Lower friction coefficients
These microscopic enhancements translate to significant improvements in cutting performance and tool longevity. Simulations and real-world tests have consistently shown that micro-textured inserts experience reduced stress concentration, lower cutting temperatures, and decreased wear.
High-Precision Cutting: Pushing the Boundaries of Accuracy
The stability and precision of femtosecond lasers enable cutting accuracies at the micron or even nanometer level. This capability opens up new possibilities for high-precision applications across industries. Moreover, the technology allows for fine-tuning of tool surfaces, removing burrs and improving surface roughness, further enhancing tool quality and performance.
The OPMT Micro3DL530V: Precision Engineered for Excellence
At the forefront of this technological revolution stands the Micro3DL530V, a five-axis femtosecond laser machining center developed by OPMT. This state-of-the-art system represents the pinnacle of precision engineering, offering a suite of capabilities that set it apart in the field of carbide insert manufacturing.
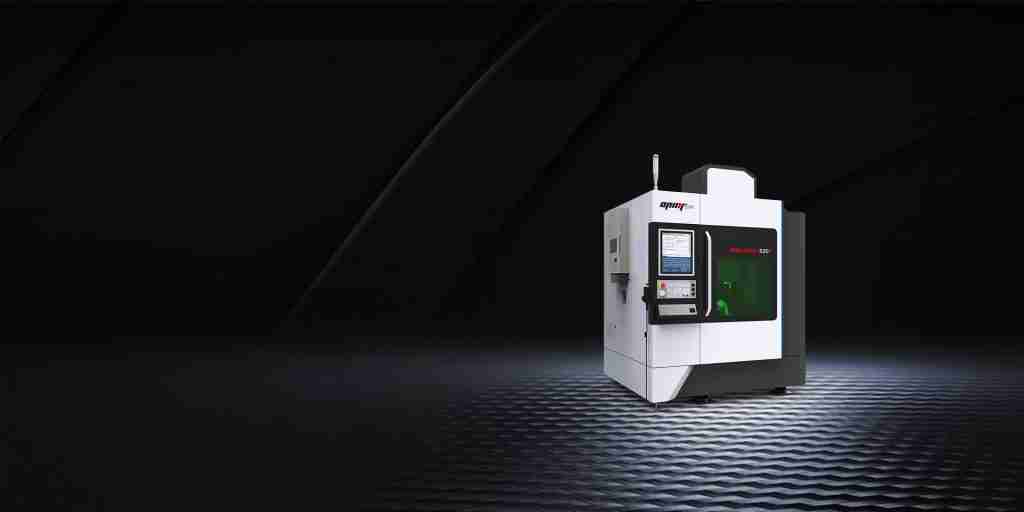
Key Advantages of the Micro3DL530V:
- Ultra-high precision: Achieves nano-level processing capabilities
- Non-contact processing: Minimizes mechanical stress on materials
- Minimal heat-affected zone: Reduces thermal damage for superior results
- Unparalleled flexibility: Adapts to a wide range of materials and applications
- Environmentally friendly: Operates with minimal pollution or waste
- Complex surface texturing: Capable of creating intricate patterns and structures
The Micro3DL530V’s versatility extends beyond carbide inserts, making it an invaluable tool for processing a variety of materials including ceramics, CBN, PCD, and diamond.
The Future of Precision Manufacturing
As industries continue to demand higher precision, longer-lasting tools, and more efficient manufacturing processes, the role of femtosecond laser processing in carbide insert production is set to grow exponentially. The technology’s ability to create complex surface textures, achieve nanometer-level accuracy, and improve tool performance positions it as a cornerstone of next-generation manufacturing.
The OPMT Micro3DL530V stands at the vanguard of this technological revolution, offering manufacturers the means to push the boundaries of what’s possible in precision tooling. As we look to the future, it’s clear that femtosecond laser processing will play a pivotal role in shaping the landscape of advanced manufacturing, driving innovation and efficiency across industries.
In an era where precision is paramount, femtosecond laser processing of carbide inserts isn’t just an advancement—it’s a necessity for staying competitive in the global manufacturing arena.