Environmental Challenges in Traditional Diamond Processing
Diamond tool manufacturing has long relied on processes that pose significant environmental hazards. Traditional methods like electrical discharge machining (EDM) and chemical etching generate substantial toxic waste, creating environmental compliance challenges for manufacturers in 2025. These conventional approaches utilize copper wheels, harsh chemicals, and coolants that produce hazardous byproducts requiring specialized disposal protocols.
Water consumption represents another critical concern, with grinding operations demanding extensive resources for cooling and debris removal. A typical EDM operation consumes approximately 4.5 kWh per hour of electricity-significantly higher than laser alternatives-while coolant systems require constant replenishment and maintenance. The cumulative environmental footprint extends beyond direct resource usage to include the extraction and transportation of raw materials for consumables like copper wheels that require frequent replacement.
Workplace safety considerations further compound these challenges. Traditional processing methods generate harmful particulates and vapors that necessitate comprehensive ventilation systems. Workers may be exposed to both immediate hazards and long-term health risks when operating EDM equipment, where chip formation and cracks during machining increase both safety concerns and material waste.
Sustainable Advantages of Laser-Based Processing
How can manufacturers address these environmental concerns while maintaining precision? OPMT Laser’s advanced 5-axis systems like the Light 5X 60V revolutionize diamond tool production through sustainable technology. These systems achieve zero chemical waste operations by eliminating cutting fluids and solvents entirely, dramatically reducing environmental impact while producing tools with sub-5μm precision.
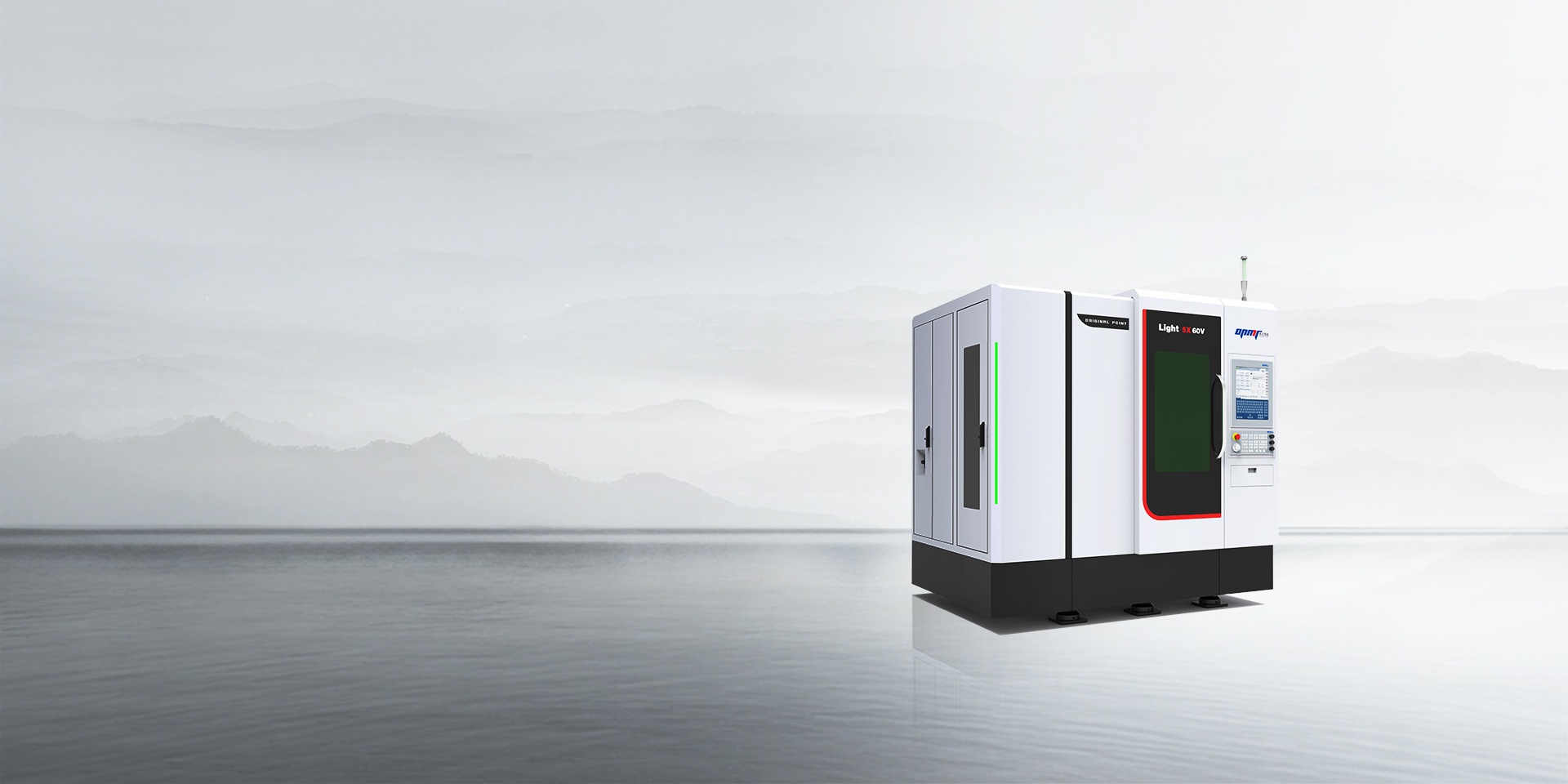
Resource efficiency stands as a primary advantage of laser processing technology. OPMT’s systems utilize linear motors and 100W ultrafast lasers that achieve impressive 3.0 mm/min cutting speeds while consuming just 23–25 KVA power-representing approximately 50% energy reduction compared to EDM machinery per production unit. The closed-loop cooling systems further minimize water usage, addressing a critical environmental concern in manufacturing operations.
Advanced dust collection technology ensures workplace safety while preventing environmental contamination. Machines like the Micro3D L570V incorporate innovative dust pelletizing systems that capture 99.8% of particulate matter generated during processing. This comprehensive approach to waste management creates cleaner working environments while virtually eliminating airborne contaminants that would otherwise require extensive filtration and hazardous waste handling.
Economic Benefits Through Sustainability
Sustainability initiatives frequently deliver compelling financial returns, and laser-based diamond tool manufacturing exemplifies this principle. When comparing traditional EDM processes with OPMT’s laser technology, the economic advantages become immediately apparent. Comprehensive cost analyses reveal monthly consumables expenses of $ 4,190 for EDM operations versus just $ 1,956 for equivalent laser processing-representing a 53% reduction in ongoing operational costs.
Metric | Traditional EDM/Grinding | Laser Processing | Improvement |
---|---|---|---|
Consumables cost/month | $4,190 | $1,956 | 53% reduction |
Floor space requirements | 10 m² | 6 m² | 40% smaller footprint |
Processing time (typical part) | 24 hours | 8 hours | 3x faster production |
Facility requirements present another significant advantage. OPMT’s LightMUT 750V and similar systems require approximately 40% less floor space than traditional equipment, enabling more efficient facility utilization and reducing associated overhead costs like heating, cooling, and maintenance. This space efficiency translates directly to lower capital requirements when establishing or expanding manufacturing operations.
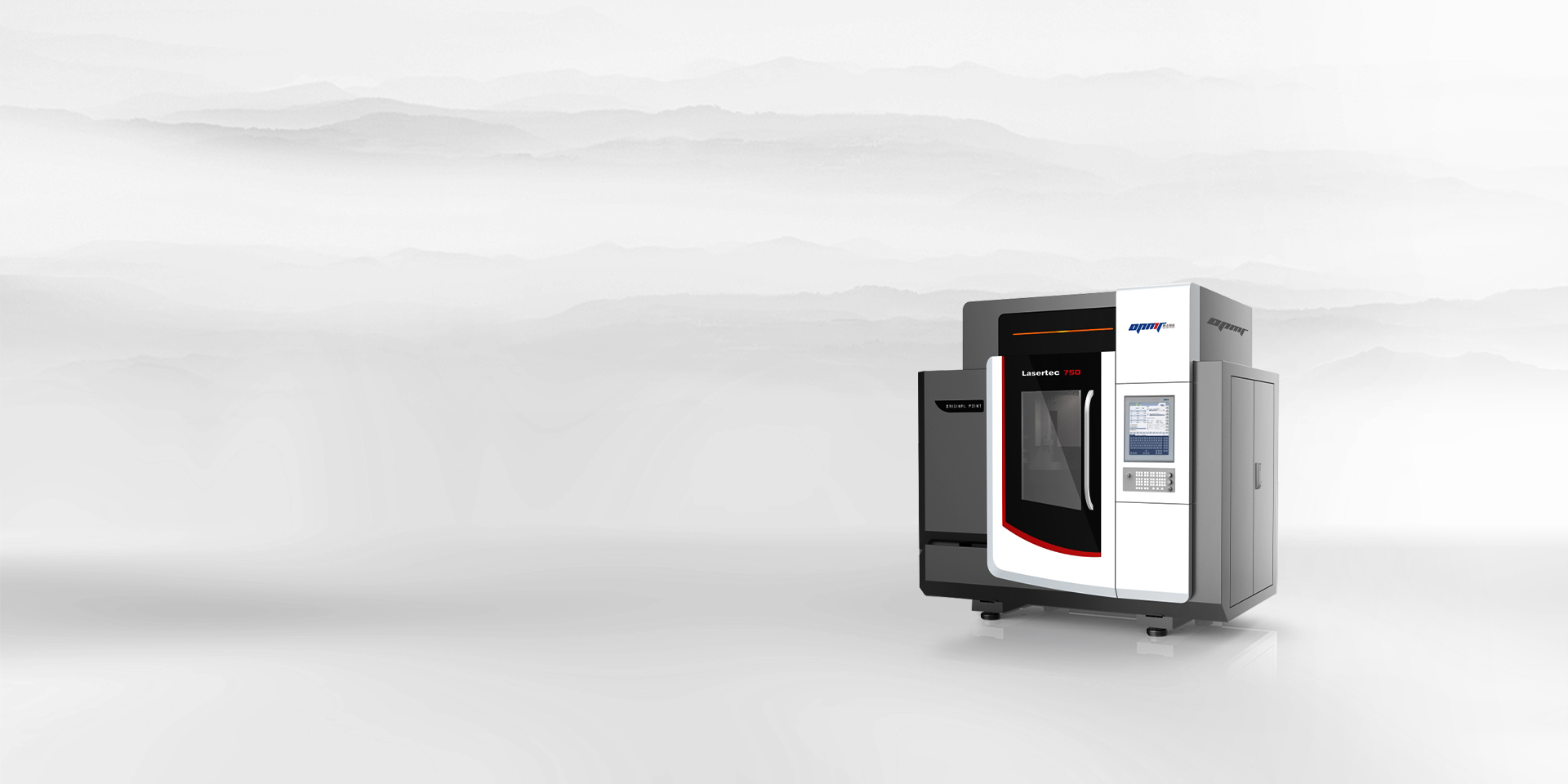
Regulatory compliance advantages provide less obvious but equally valuable economic benefits. By eliminating hazardous chemical waste, manufacturers avoid increasingly stringent disposal regulations and associated costs. OPMT’s laser systems align perfectly with ISO 14001 environmental management standards, reducing administrative burden while enhancing corporate sustainability credentials that increasingly influence purchasing decisions in 2025’s environmentally conscious marketplace.
Case Study: Manufacturing Transformation Results
A leading automotive tool manufacturer demonstrates the real-world impact of transitioning to sustainable laser processing. After implementing OPMT’s Light 5X 60V into their production workflow, they documented remarkable environmental and operational improvements that validate the technology’s potential.

Environmental metrics tell a compelling story of transformation. The manufacturer eliminated approximately 12 tons of chemical waste annually while reducing energy consumption by 30% through the implementation of closed-loop cooling systems. Water usage for processing declined significantly, aligning with increasingly stringent water conservation requirements that affect industrial operations in 2025.
Production efficiency gains proved equally impressive. PCD tool processing times decreased from 50 minutes using traditional methods to just 4 minutes 26 seconds with laser technology, while maintaining exceptional edge passivation accuracy of 0.00412 mm. This dramatic productivity improvement enabled the manufacturer to increase throughput by 22% without expanding facility size or workforce.
The financial analysis confirms laser technology’s compelling ROI proposition. The manufacturer documented $195,000 in annual savings from consumable reductions alone, while increased throughput generated additional revenue opportunities. Complete return on investment was achieved in just 14 months, creating a sustainable competitive advantage both environmentally and economically. For manufacturers considering similar transitions, OPMT’s PCD laser cutting solutions provide detailed implementation guidance based on successful case studies.
Disclaimer
This content is compiled by OPMT Laser based on publicly available information for reference only; mentions of third-party brands and products are for objective comparison and do not imply any commercial association or endorsement.