Nylon ist seit seiner Einführung in den 1930er Jahren ein Eckpfeiler der Fertigung und seine Vielseitigkeit fasziniert die Industrie auch heute noch. Als Polyamidpolymere sind diese Materialien für die Herstellung von Kunststofffolien bis hin zu Metallbeschichtungen unverzichtbar, insbesondere in anspruchsvollen Branchen wie Öl und Gas. Wussten Sie, dass Nylon 12 (PA 12) für seine außergewöhnliche Festigkeit und sein geringes Gewicht bekannt ist und sich daher hervorragend für die additive Fertigung eignet?
Sie fragen sich vielleicht, wie dieses Material Ihre Projekte verbessern kann. In diesem Artikel werden wir die beeindruckenden Eigenschaften von PA 12, einschließlich seiner Feuchtigkeitsbeständigkeit und Wärmestabilität, aufdecken und gleichzeitig seine vielfältigen Anwendungen in verschiedenen Branchen untersuchen. Egal, ob Sie ein erfahrener Profi sind oder gerade erst anfangen, sich mit fortschrittlichen Materialien zu beschäftigen, Sie werden wertvolle Erkenntnisse gewinnen, die Ihnen helfen können, fundierte Entscheidungen für Ihr nächstes Projekt zu treffen. Machen Sie sich bereit zu entdecken, wie Nylon 12 Ihre Herstellungsprozesse verbessern kann!
Nylon 12 Eigenschaften
PA 12, allgemein als Nylon 12 bezeichnet, ist ein vielseitiger thermoplastischer Kunststoff, der für seine außergewöhnliche Zähigkeit, Zugfestigkeit und Schlagfestigkeit bekannt ist. Aufgrund seiner bemerkenswerten mechanischen Eigenschaften wird dieses Material häufig in verschiedenen Anwendungen eingesetzt, darunter Automobilkomponenten und 3D-Druck.
Hauptmerkmale von PA 12
- Zugfestigkeit: PA 12 weist eine beeindruckende Zugfestigkeit auf und eignet sich daher für anspruchsvolle Anwendungen, bei denen es vor allem auf Haltbarkeit ankommt.
- Chemische Beständigkeit: Dieses Polyamid weist eine hohe Beständigkeit gegenüber zahlreichen Chemikalien, Ölen und Lösungsmitteln auf und gewährleistet so eine lange Lebensdauer auch in anspruchsvollen Umgebungen.
- Thermische Stabilität: PA 12 behält seine strukturelle Integrität bei erhöhten Temperaturen und widersteht Hitze bis zu 185 °C ohne nennenswerte Verschlechterung.
Anwendungen von Nylon 12
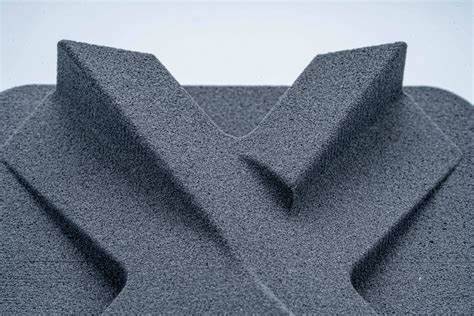
Aufgrund seiner vorteilhaften Eigenschaften wird Nylon 12 in zahlreichen Branchen eingesetzt. Zu den üblichen Anwendungen gehören:
- Automobilkomponenten: Wird für Zahnräder, Lager und andere wichtige Teile verwendet, die eine hohe Schlagfestigkeit erfordern.
- Teile für die Luft- und Raumfahrt: Leichte und dennoch langlebige Materialien sind in der Luft- und Raumfahrtbranche unverzichtbar, wo Leistung und Zuverlässigkeit an erster Stelle stehen.
- Funktionale Prototypen: In additiven Fertigungsverfahren wie Fused Deposition Modeling (FDM) und Multi Jet Fusion (MJF) dient PA 12 als effektiver Werkstoff zur Herstellung von Prototypen und Funktionsteilen.
Das Verständnis der Unterschiede zwischen generischem PA 12 und proprietären Formen ist entscheidend für die Auswahl des richtigen Materials für bestimmte Anwendungen. Nachfolgend finden Sie einen Vergleich verschiedener Nylon 12-Typen:
Materialtyp | Verfahren | Hauptmerkmale |
---|---|---|
Generisches PA 12 | Spritzguss | Hohe Schlagfestigkeit und Abriebfestigkeit |
FDM Nylon 12™ | Fused Deposition Modeling (FDM) | Kostengünstig für Rapid Prototyping |
HP® PA 12 mit hoher Wiederverwendbarkeit | Multi Jet Fusion (MJF) | Verbesserte Wiederverwendbarkeit und Effizienz in der Produktion |
Durch die Nutzung dieser Eigenschaften und das Verständnis der einzigartigen Vorteile verschiedener Nylon 12-Varianten können Hersteller fundierte Entscheidungen treffen, die die Leistung und Langlebigkeit ihrer Produkte verbessern.
FDM Nylon 12™ Übersicht
FDM Nylon 12™ ist ein thermoplastisches Hochleistungsfilament, das hauptsächlich in FDM-Druckern von Stratasys verwendet wird. Dieses Material ist für seine außergewöhnliche Zugfestigkeit von 48 MPa bekannt und wird wegen seiner Flexibilität und Haltbarkeit geschätzt, wodurch es sich für die Herstellung robuster Komponenten eignet. Während des Druckvorgangs wird das Filament erhitzt und durch die Düse des Druckers extrudiert, was eine präzise Schichtabscheidung ermöglicht.
Stützstrukturen im FDM-Druck
Ähnlich wie bei anderen Fused Deposition Modeling (FDM)-Techniken erfordern Designs mit Überhängen die Einbindung von Stützstrukturen. Viele moderne FDM-Drucker sind mit dualen Extrusionsfunktionen ausgestattet – eine Düse für Nylon 12™ und eine andere für ein entfernbares Stützmaterial wie wasserlösliches PVA. Diese Funktion rationalisiert die Nachbearbeitung, indem sie das einfache Entfernen der Stützen nach Abschluss des Druckvorgangs ermöglicht.
Mechanische Spezifikationen
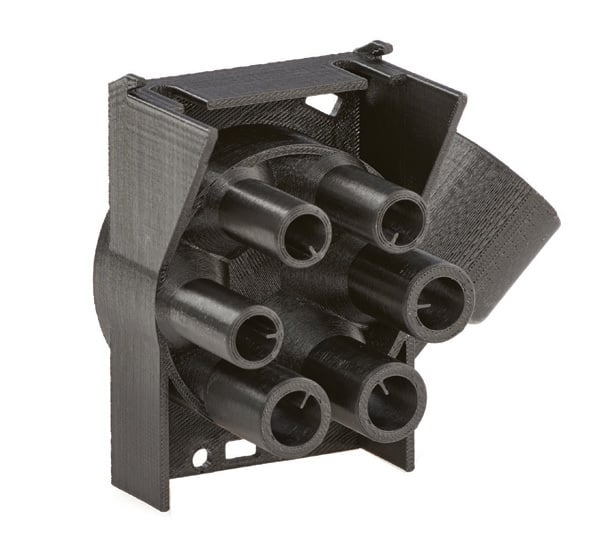
Die mechanischen Eigenschaften von HP PA 12 sind entscheidend für die Bewertung seiner Leistung in verschiedenen Anwendungen:
Eigentum | Wert |
---|---|
Zugfestigkeit (XY) | 48 MPa / 6960 psi |
Zugmodul (XY) | 1700 MPa / 247 ksi |
Bruchdehnung (XY) | 20% |
IZOD Schlagfestigkeit | 3,5 kJ/m² |
Wärmeableitung (XY) | 175 ºC / 347 ºF |
Diese Spezifikationen unterstreichen die Eignung von Nylon 12 für anspruchsvolle Anwendungen in unterschiedlichsten Branchen, einschließlich der Luft- und Raumfahrt sowie der Automobilbranche.
MJF und HP® 3D Polyamid 12 mit hoher Wiederverwendbarkeit
HP® 3D High Reusability Polyamide 12 (HP® PA 12) ist ein spezieller Thermoplast, der für die Verwendung mit der Multi Jet Fusion (MJF)-Technologie entwickelt wurde. Dieses Material wird für seine beeindruckenden mechanischen Eigenschaften geschätzt, darunter hohe Zugfestigkeit, Haltbarkeit und eine Wiederverwendbarkeitsrate von bis zu 80%, die den Abfall während der Produktion erheblich minimiert.
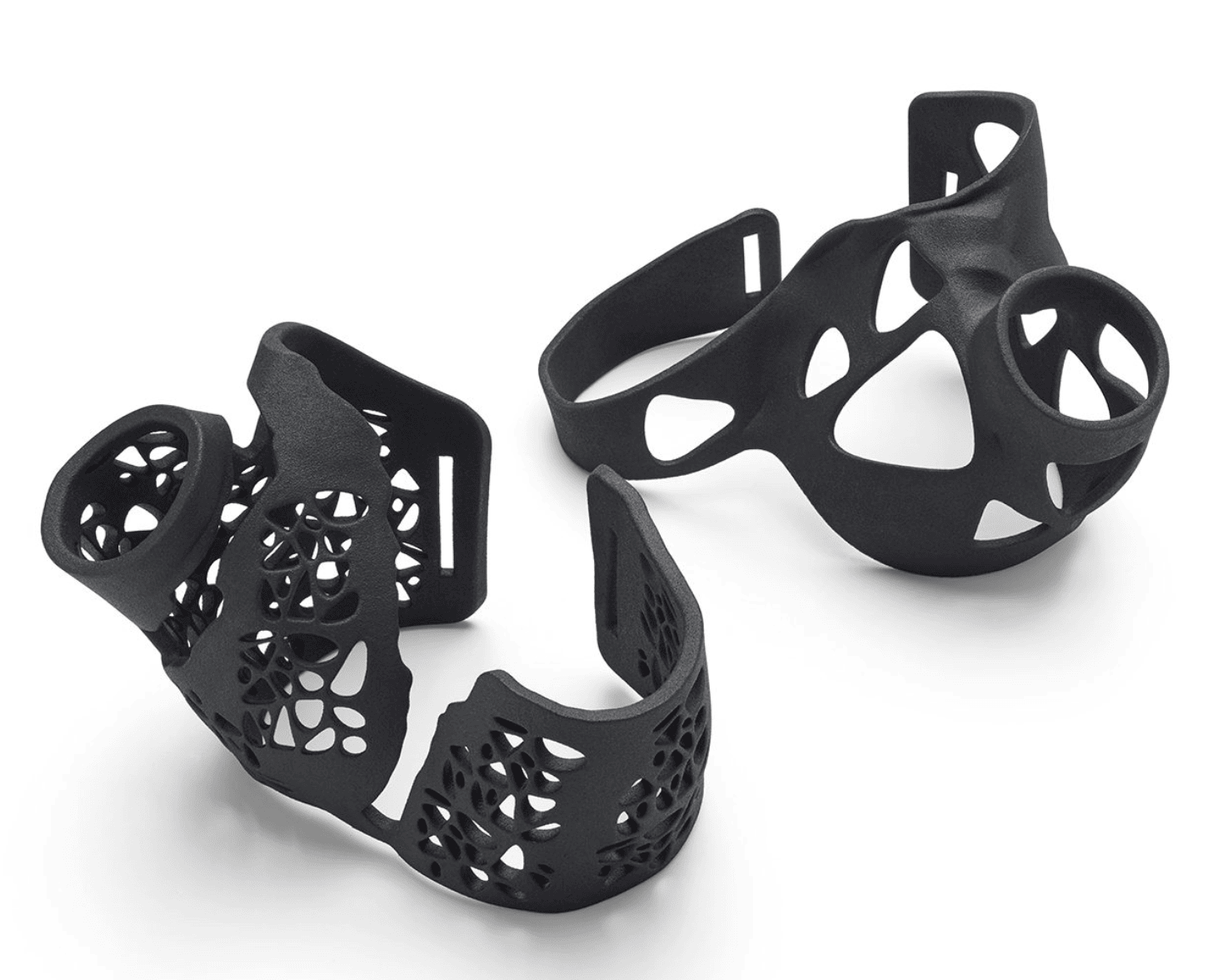
Kunden entscheiden sich häufig für das MJF-Verfahren, da es selbsttragend ist und Ingenieuren die Flexibilität bietet, komplexe Geometrien ohne herkömmliche Stützstrukturen zu entwerfen. Diese Funktion ermöglicht die Erstellung komplexer Baugruppen als Einzelteile, was die Fertigungseffizienz steigert und die Montagezeit verkürzt.
Nach dem Druckvorgang mit HP® MJF müssen die Teile vorsichtig aus dem Bett aus nicht verschmolzenem Pulver entnommen werden. Dieser wichtige Nachbearbeitungsschritt gewährleistet die Integrität des Endprodukts und sollte bei der Bewertung der Gesamtproduktionskosten berücksichtigt werden. Im Gegensatz zum Fused Deposition Modeling (FDM) erzeugt die MJF-Technologie nahezu isotrope Materialien, was zu minimalen Steifigkeitsunterschieden in verschiedenen Druckrichtungen führt.
Da in der Industrie auch im Jahr 2025 Nachhaltigkeit und Effizienz immer mehr im Vordergrund stehen, bleibt HP® PA 12 die erste Wahl für Hersteller, die nach zuverlässigen und umweltfreundlichen Lösungen in der additiven Fertigung suchen.
Warum HP verwenden?® PA 12
HP® PA 12 ist ein Hochwertiges Material für Anwendungen, die eine Balance erfordern von Kraft und Präzision. Dieses Polyamid weist nahezu isotrope mechanische Eigenschaften auf und ermöglicht so komplexe Designs mit hervorragender Oberflächenqualität. SyBridge verwendet HP® PA 12 zur Herstellung von Komponenten mit hoher Dichte und geringer Porosität, was es ideal für verschiedene Anwendungen macht, darunter Texturierung, Färbung, Prägung und Gravur. Seine Dichte ähnelt stark der von herkömmlichen Spritzgussmaterialien wie ABS und gewährleistet eine mechanische Leistung, die strengen Standards entspricht, insbesondere in der medizinischer Bereich wo Biokompatibilität entscheidend ist.
Als kostengünstige Alternative Für Kleinserienproduktionen macht HP® PA 12 keine Kompromisse bei der Qualität. Seine einfache Sterilisation verbessert seine Eignung für medizinische Anwendungen, bei denen Sicherheit an erster Stelle steht. Durch die Nutzung seiner einzigartigen Eigenschaften können Branchen erhebliche Fortschritte erzielen in Produktdesign und Funktionalität, um den sich entwickelnden Marktanforderungen im Jahr 2025 und darüber hinaus gerecht zu werden.
Beliebte Anwendungen
HP® PA 12 ist für seine Langlebigkeit bekannt und daher die ideale Wahl für Anwendungen, bei denen flexible Materialien erforderlich sind, die auch bei wiederholtem Gebrauch bruch- und rissfest sind. Einige weit verbreitete Anwendungen enthalten:
- Schnappverschlüsse
- Gehäuse
- Befestigungsmaterial für Outdoor-Gehäuse
- Gewindeeinsätze
- Vibrationsbelastete Teile
- Kinetische Komponenten
- Vorrichtungen und Halterungen
Die Dichte von HP® PA 12 ist vergleichbar mit herkömmlichen Kunststoffen wie ABS. Seine Flexibilität ermöglicht es Designern jedoch, starke und dennoch leichte Komponenten zu schaffen durch Design für die additive Fertigung (DFAM). Diese Fähigkeit ermöglicht die Herstellung von Teilen, die nicht nur strenge Industriestandards erfüllen, sondern auch eine außergewöhnliche Ermüdungsbeständigkeit aufweisen – und ist damit die perfekte Lösung für anspruchsvolle Branchen wie die Luft- und Raumfahrt- und Automobilindustrie.
Nachhaltigkeits- und Kostenüberlegungen zu HP PA 12
HP® PA 12 wurde entwickelt, um den Abfall deutlich zu reduzieren, indem es die Wiederverwendung von Restpulver aus früheren Bauten ermöglicht. Diese innovative Materialzusammensetzung ermöglicht den Einsatz von 20% neues Pulver neben 80% Recyclingpulver in jedem Produktionszyklus. Durch das Recycling von HP® PA 12 minimieren Hersteller nicht nur den Materialabfall, sondern bleiben auch kosteneffizient und können so wettbewerbsfähige Preise für hochwertige Materialien sicherstellen.
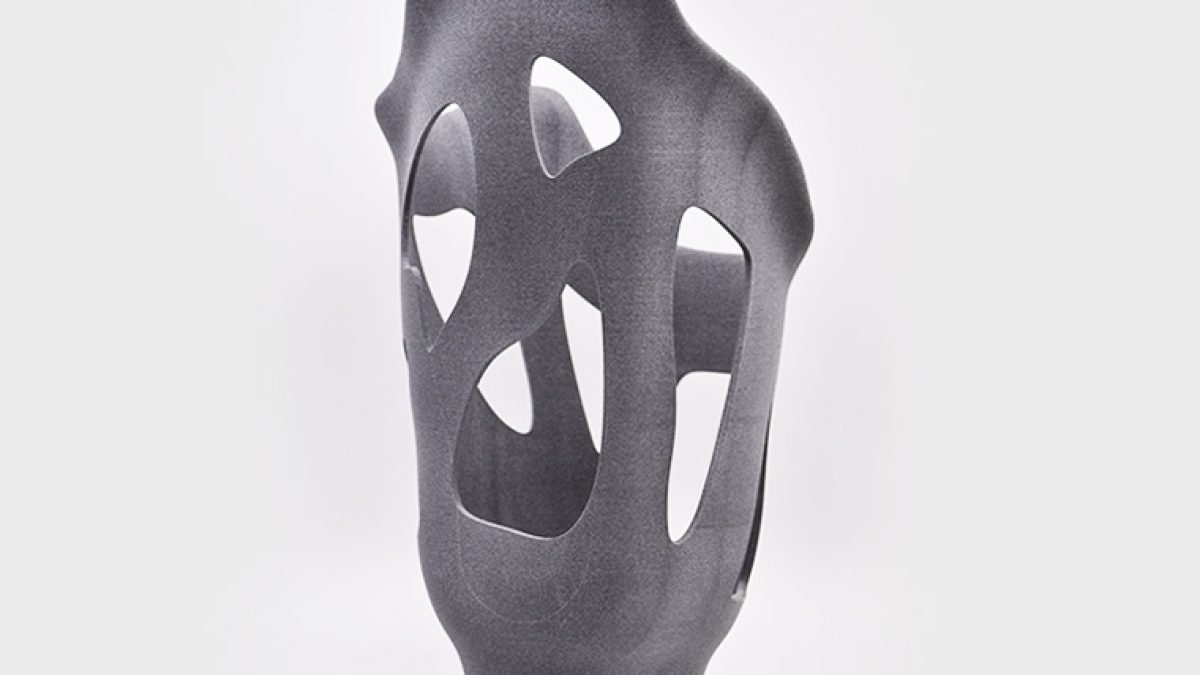
Einblicke in Design und Betrieb
Bei der Verwendung von HP® PA 12 profitieren Designer von weniger Einschränkungen im Vergleich zu herkömmlichen Materialien. Zu den wichtigsten Designüberlegungen gehört die Integration von Belüftungsöffnungen für innere Hohlräume, um das Einschließen von Pulver während des Druckvorgangs zu verhindern. Die Nachbearbeitung beginnt mit der Entfernung von überschüssigem Pulver, was normalerweise durch Luft- oder Medienstrahlen vor der Oberflächenbearbeitung erreicht wird. HP® PA 12 ist zwar in einem standardmäßigen Grauton erhältlich, kann aber auch gefärbt oder lackiert werden, um bestimmten ästhetischen Anforderungen gerecht zu werden, und bietet so Vielseitigkeit für verschiedene Anwendungen.
Wirtschaftliche und ökologische Auswirkungen
Die Einführung von HP® PA 12 steht im Einklang mit nachhaltigen Herstellungsverfahren, da es eine der höchsten Wiederverwendbarkeitsquoten unter ähnlichen Materialien aufweist – bis zu 85%. Diese Eigenschaft trägt nicht nur zu einer Kreislaufwirtschaft bei, sondern steigert auch die Produktionseffizienz durch die Senkung der Gesamtmaterialkosten. Da die Industrie zunehmend Wert auf Nachhaltigkeit legt, zeichnet sich HP® PA 12 als kostengünstige Lösung aus, die sowohl den ökologischen als auch den betrieblichen Anforderungen der modernen Fertigung gerecht wird.
Durch die Konzentration auf diese Aspekte unterstützt HP® PA 12 nicht nur umweltfreundliche Initiativen, sondern bietet Herstellern auch eine zuverlässige und wirtschaftlich tragfähige Materialauswahl für verschiedene Anwendungen in der sich entwickelnden Landschaft der additiven Fertigung.
Vergleich von PA 12 mit anderen Polyamiden

Vergleich von Nylon (PA) 12 und Nylon (PA) 6
Beim Vergleich Nylon 12 (PA 12) Und Nylon 6 (PA 6)werden wesentliche Unterschiede in ihren Eigenschaften deutlich. Beide sind Polyamide mit ähnlichen Amidbindungen, unterscheiden sich jedoch in der Monomerzusammensetzung: PA 12 wird abgeleitet von Laurinlactam, während PA 6 aus Caprolactam. Dies führt dazu, dass PA 12 eine höhere Kohlenstoffatomzahl in seinen Wiederholungseinheiten aufweist, was zu einer besseren Zugfestigkeit Und Schlagfestigkeit, wodurch es für anspruchsvolle Anwendungen geeignet ist.
Bezüglich chemische BeständigkeitPA 12 ist beständig gegen Lösungsmittel, Öle und Kraftstoffe und damit ideal für den Einsatz in der Automobil- und Industrieindustrie, während PA 6 eine angemessene Beständigkeit bietet, in aggressiven Umgebungen jedoch nachlassen kann. Darüber hinaus behält PA 12 seine mechanischen Eigenschaften und Dimensionsstabilität bei erhöhten Temperaturen bei und weist eine bessere thermische Stabilität als PA 6. Beide Materialien weisen eine geringe Feuchtigkeitsaufnahme auf, was ihre Stabilität in feuchten Umgebungen verbessert. Obwohl beide Polyamide Vorteile wie gute mechanische Eigenschaften und chemische Beständigkeit aufweisen, zeichnet sich Nylon 12 durch seine verbesserte Festigkeit, Haltbarkeit und thermische Leistung aus.
Vergleich von Nylon (PA) 11 und Nylon (PA) 12
Die Unterschiede zwischen Nylon 11 (PA 11) Und Nylon 12 (PA 12) weist unterschiedliche Eigenschaften auf, die sich auf ihre Anwendungen auswirken. Beide sind Polyamide mit Amidbindungen, unterscheiden sich jedoch in den Monomerquellen: PA 11 stammt aus 11-Aminoundecansäure, während PA 12 abgeleitet ist von Laurinlactam. Dies führt dazu, dass PA 12 eine höhere Kohlenstoffzahl in seinen Wiederholungseinheiten aufweist, was zu einer besseren Zugfestigkeit Und Schlagfestigkeit, wodurch es sich ideal für Anwendungen eignet, die Haltbarkeit und Verschleißfestigkeit erfordern.
Beide Materialien weisen gute chemische Beständigkeit gegen verschiedene Lösungsmittel und Öle, geeignet für den Automobil- und Industriesektor. PA 12 übertrifft PA 11 jedoch in aggressiven chemischen Umgebungen. Darüber hinaus behält PA 12 seine mechanische Integrität bei erhöhten Temperaturen bei und weist eine bessere thermische Stabilität im Vergleich zu PA 11. Beide Typen haben eine geringe Feuchtigkeitsaufnahme, was die Dimensionsstabilität unter feuchten Bedingungen gewährleistet. Insgesamt bieten sowohl Nylon 11 als auch Nylon 12 Vorteile als Polyamide, Nylon 12Die verbesserten mechanischen Eigenschaften und die thermische Stabilität machen es zur bevorzugten Wahl für anspruchsvolle Anwendungen, bei denen Festigkeit und Haltbarkeit von entscheidender Bedeutung sind.
Wann Sie mit Ihrem Anteil rechnen können
HP® PA 12 hat normalerweise eine Standardvorlaufzeit von fünf bis sieben Werktagen für die Produktion. Bei Eilaufträgen oder kleineren Bauten kann OPMT Laser Drucke in nur drei Werktagen fertigstellen. Im Allgemeinen ermöglicht die MJF-Technologie den Druck von bis zu 251 Kubikzoll pro Stunde; daher kann ein vollständig gepacktes HP®-Druckvolumen etwa 17 Stunden Bauzeit erfordern.
Die Abkühlung nach dem Drucken ist ein wesentlicher zu berücksichtigender Faktor, da sie je nach Größe des Bauteils zwischen drei und 50 Stunden dauern kann. Kleinere Teile mit weniger Pulver neigen dazu, schneller abzukühlen. Glücklicherweise hat HP® eine sekundäre Nachbearbeitungsstation implementiert, die jedes Teil bei Bedarf innerhalb von zehn Stunden schnell abkühlen kann.
Wenn Sie daran interessiert sind, traditionelle Designbeschränkungen aufzubrechen, um innovative Produkte zu entwickeln, empfehlen wir Ihnen, die Möglichkeiten von HP® PA 12 zu erkunden. Kontaktieren Sie unser Team noch heute um herauszufinden, wie wir Ihnen helfen können, Ihre Produktvision effizient und effektiv zu verwirklichen.
Haftungsausschluss
Dieser Inhalt wurde von OPMT Laser auf Grundlage öffentlich verfügbarer Informationen zusammengestellt und dient ausschließlich zu Referenzzwecken. Die Erwähnung von Marken und Produkten Dritter dient dem objektiven Vergleich und stellt keine kommerzielle Verbindung oder Billigung dar.