In der heutigen wettbewerbsintensiven Fertigungslandschaft ist die Integration der Automatisierung in CNC-Laserschweißen stellt einen transformativen Ansatz zur Steigerung von Produktivität, Präzision und Betriebseffizienz dar. Dieser umfassende Leitfaden untersucht, wie automatisierte Materialhandhabungssysteme den Laserschweißbetrieb revolutionieren und bietet Herstellern die notwendigen Einblicke, um diese Technologien effektiv umzusetzen.
Die Rolle der Automatisierung beim modernen CNC-Laserschweißen
Die Entwicklung der Laserschweißtechnologie hat Fertigungsprozesse branchenübergreifend grundlegend verändert. Die Automatisierung ist zum Eckpfeiler dieses Wandels geworden und hat die Leistungsfähigkeit von Laserschweißsystemen auf ein bisher ungeahntes Niveau gehoben.
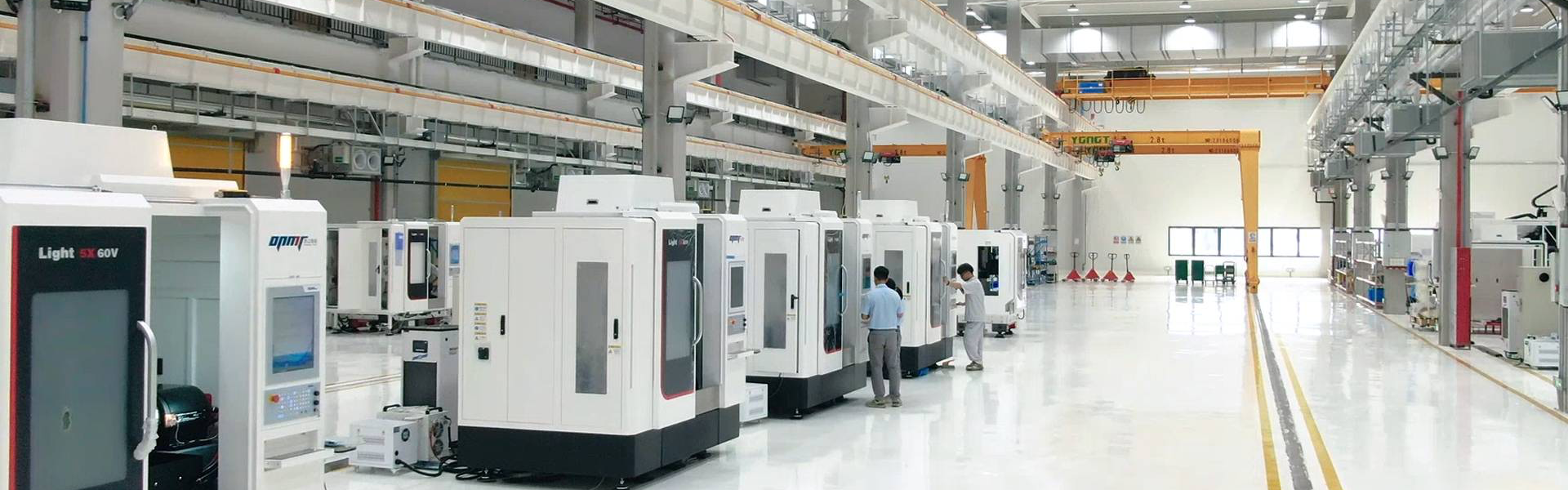
Wichtige Vorteile für die Einführung der Automatisierung
Die Automatisierung des Laserschweißens bietet zahlreiche Vorteile, die herkömmliche manuelle Verfahren nicht bieten können. Die Präzision eines fein fokussierten Laserstrahls ermöglicht eine exakte Kontrolle des Schweißbereichs und stellt sicher, dass nur das Zielmaterial beeinflusst wird. Dies reduziert die Wärmeeinflusszone deutlich und minimiert Verformungen. Mit automatisierten Systemen erzielen Hersteller gleichbleibend hochwertige Schweißnähte mit einer Wiederholgenauigkeit, die menschliche Bediener schlicht nicht erreichen können.
Ebenso beeindruckend ist die Geschwindigkeitssteigerung. Was früher beim manuellen Wolfram-Inertgasschweißen (WIG) 90 Minuten dauerte, lässt sich heute mit automatisierten Laserschweißsystemen in nur 10 Minuten erledigen. Diese drastische Verkürzung der Zykluszeit führt direkt zu höherem Durchsatz und verbesserter Produktivität.
Neben Geschwindigkeit und Präzision bieten automatisierte Laserschweißsysteme:
- Reduzierte Arbeitskosten durch minimierte menschliche Eingriffe
- Verbesserte Sicherheit durch Begrenzung der Belastung der Arbeiter mit gefährlichen Umgebungen
- Geringerer Materialabfall und Nacharbeitsbedarf
- Flexibilität bei der Verarbeitung verschiedener Materialien und Dicken
- Echtzeit-Überwachungsfunktionen zur Qualitätskontrolle
Entwicklung der Lasertechnologie
Der Übergang von herkömmlichen CO2-Lasern zu modernen Faserlasern hat maßgeblich zur Verbesserung der Automatisierungsmöglichkeiten beigetragen. Faserlaser liefern eine stabilere und gleichmäßigere Leistung, was für die Gewährleistung hochwertiger Schweißnähte unerlässlich ist. Sie sind schneller, präziser und wartungsärmer, was sie ideal für automatisierte Schweißprozesse macht.
Arten automatisierter Materialhandhabungssysteme für das Laserschweißen
Die Implementierung der richtigen Materialhandhabungslösung ist entscheidend für die Effizienz von CNC-Laserschweißvorgängen. Es gibt verschiedene Optionen, jede mit unterschiedlichen Vorteilen für bestimmte Anwendungen.
Robotersysteme
Roboter bilden den Grundstein für die moderne automatisierte Materialhandhabung beim Laserschweißen. Sie führen Aufgaben mit außergewöhnlicher Präzision und Wiederholgenauigkeit aus und steigern so die Produktionseffizienz deutlich. Zu den gängigsten Robotersystemen gehören:
- Sechsachsige Knickarmroboter: Bieten maximale Flexibilität für komplexe Schweißbahnen und -positionen
- SCARA-Roboter (Selective Compliance Assembly Robot Arm): Hervorragend geeignet für spezielle Anwendungen wie das Anklemmen von Laschen an Sammelschienen
- Kollaborative Roboter (Cobots): Sie wurden entwickelt, um mit Menschen zusammenzuarbeiten und wiederkehrende Aufgaben zu erledigen, während sich die Bediener auf komplexere Aspekte konzentrieren können.
Robotersysteme gewährleisten eine gleichbleibende Schweißqualität, indem sie Laserköpfe mit höchster Präzision positionieren und programmierten Bahnen präzise folgen. Sie sind besonders wertvoll in Produktionsumgebungen mit hohem Produktionsvolumen, in denen Tausende von Schweißnähten in gleichbleibender Qualität ausgeführt werden müssen.
Fördersysteme und Transfermechanismen
Automatisierte Fördersysteme gewährleisten einen reibungslosen Teilefluss durch den Schweißprozess. Diese Systeme können Folgendes umfassen:
- Lineartransfersysteme: Teile geradlinig durch die Schweißstation bewegen
- Rundschalttische: Positionieren Sie Teile in präzisen Winkeln für komplexe Schweißvorgänge
- Palettenwechselsysteme: Ermöglichen das Be- und Entladen bei gleichzeitigem, ununterbrochenem Schweißbetrieb
Diese Systeme optimieren den Arbeitsablauf, indem sie Ausfallzeiten zwischen den Vorgängen minimieren und ein gleichmäßiges Produktionstempo aufrechterhalten.
Integrationsfertige Pakete
Für Hersteller, die ihre Implementierung optimieren möchten, bieten integrierbare Laserschweißpakete erhebliche Vorteile. Diese umfassenden Lösungen umfassen typischerweise:
- Laser und Strahlführungssysteme
- Komponenten der industriellen Bildverarbeitung
- Werkzeuge zur Prozessüberwachung
- Hardware/Software zur Roboterintegration
- Benutzerfreundliche Bedienoberflächen
Diese Pakete reduzieren die Einrichtungszeit und die Entwicklungskosten für kundenspezifische Konfigurationen erheblich. Sie verfügen über erweiterte Überwachungsfunktionen durch maschinelles Sehen und Echtzeit-Prozessüberwachung, die eine präzise Laserstrahlausrichtung gewährleisten und Anomalien beim Schweißen erkennen.
Vergleich automatisierter Handhabungssysteme
Systemtyp | Beste Anwendungen | Vorteile | Einschränkungen |
---|---|---|---|
6-Achs-Roboter | Komplexe 3D-Schweißnähte, vielfältige Teilegeometrien | Maximale Flexibilität, großer Arbeitsbereich, hohe Präzision | Höhere Anschaffungskosten, komplexere Programmierung |
SCARA-Roboter | Wiederkehrende Aufgaben, planare Anwendungen | Schnelle Zykluszeiten, gute Präzision, geringere Kosten | Beschränkung auf einfachere Bewegungen, kleinerer Arbeitsbereich |
Cobots | Kleinserienproduktion, Umgebungen für die Zusammenarbeit von Menschen | Einfache Programmierung, flexibler Einsatz, Sicherheitsfunktionen | Geringere Nutzlastkapazität, langsamere Betriebsgeschwindigkeiten |
Fördersysteme | Großserienproduktion, linearer Teilefluss | Kontinuierlicher Betrieb, konsistentes Timing, skalierbar | Weniger flexibel bei unterschiedlichen Teiletypen, feste Pfade |
Bereit zur Integration | Neue Anwender, standardisierte Anwendungen | Schnellere Implementierung, geringere Integrationskomplexität | Möglicherweise sind Anpassungen für besondere Anforderungen erforderlich |
Implementierung von Robotersystemen: Best Practices und Herausforderungen
Die erfolgreiche Implementierung von Robotersystemen für die Materialhandhabung beim Laserschweißen erfordert eine sorgfältige Planung und die Berücksichtigung mehrerer Schlüsselfaktoren.
Best Practices für die Roboterintegration
Berücksichtigen Sie bei der Integration von Robotern in CNC-Laserschweißgeräte diese bewährten Ansätze:
- Führen Sie vor der Implementierung eine gründliche Prozessanalyse durch, um Engpässe und Automatisierungsmöglichkeiten zu identifizieren
- Wählen Sie Roboter mit der passenden Traglastkapazität, Reichweite und Präzision für Ihre spezifischen Schweißanwendungen
- Implementieren Sie umfassende Sicherheitsfunktionen, einschließlich Lasergehäusen der Klasse 1 für einen sicheren Betrieb
- Entwerfen Sie Vorrichtungen und Teilepräsentationssysteme, die eine konsistente Teilepositionierung gewährleisten
- Nutzen Sie Offline-Programmierfunktionen, um Produktionsausfallzeiten während der Einrichtung zu minimieren
- Investieren Sie in die Schulung von Bedienern und Wartungspersonal
Für eine optimale Integration müssen sowohl Hard- als auch Softwareaspekte berücksichtigt werden. Hersteller sollten Systeme mit benutzerfreundlichen Oberflächen bevorzugen, die eine einfache Programmierung und Anpassung der Schweißparameter über Touchscreen-Bedienelemente ermöglichen.
Häufige Integrationsherausforderungen und -lösungen
Trotz der Vorteile bringt die Implementierung robotergestützter Materialhandhabungssysteme mehrere Herausforderungen mit sich:
- Hohe Anfangsinvestition: Roboterschweißsysteme erfordern erhebliche Vorlaufkosten, einschließlich Installation und Schulung.
- Lösung: Beginnen Sie mit einer Implementierung im kleineren Maßstab, die sich auf Teile mit hohem Volumen konzentriert, und erweitern Sie diese dann, wenn sich der ROI zeigt.
- Komplexe Einrichtung und Programmierung: Das Einrichten und Programmieren von Schweißrobotern erfordert spezielle Fähigkeiten und Kenntnisse.
- Lösung: Nutzen Sie Schweißkameras und Überwachungssysteme, um die Fehlersuche und Einrichtung zu vereinfachen, indem Sie klare Ansichten der Schweißqualität bereitstellen.
- Material- und Aufgabenbeschränkungen: Roboter haben möglicherweise Probleme mit komplexen Schweißnähten an unterschiedlichen Materialien oder in schwierigen Positionen.
- Lösung: Integrieren Sie fortschrittliche Bildverarbeitungssysteme und adaptive Programmierung, um die Flexibilität zu erhöhen.
- Wartungsanforderungen: Regelmäßige Wartung ist entscheidend, um eine langfristige Leistung sicherzustellen.
- Lösung: Implementieren Sie vorausschauende Wartungsprogramme mithilfe von IoT-Sensoren, um den Systemzustand zu überwachen und ungeplante Ausfallzeiten zu verhindern.
Wichtige Überlegungen zur Implementierung
Vor der Implementierung einer automatisierten Materialhandhabung für das Laserschweißen sollten Hersteller Folgendes prüfen:
- Produktionsvolumen und -mix: Höhere Volumina mit geringerer Vielfalt profitieren am meisten von der Vollautomatisierung
- Teileeigenschaften: Größe, Gewicht, Material und Komplexität beeinflussen die Handhabungsanforderungen
- Budgetbeschränkungen: Wägen Sie die anfängliche Investition gegen langfristige Betriebseinsparungen ab
- Verfügbare Grundfläche: Roboterzellen benötigen entsprechende Frei- und Sicherheitszonen
- Integration mit bestehenden Systemen: Sicherstellung der Kompatibilität mit vor- und nachgelagerten Prozessen
Fallstudien: Produktivitätssteigerung durch Automatisierung
Reale Implementierungen demonstrieren die konkreten Vorteile der automatisierten Materialhandhabung bei Laserschweißvorgängen.
Herstellung von Automobilkomponenten
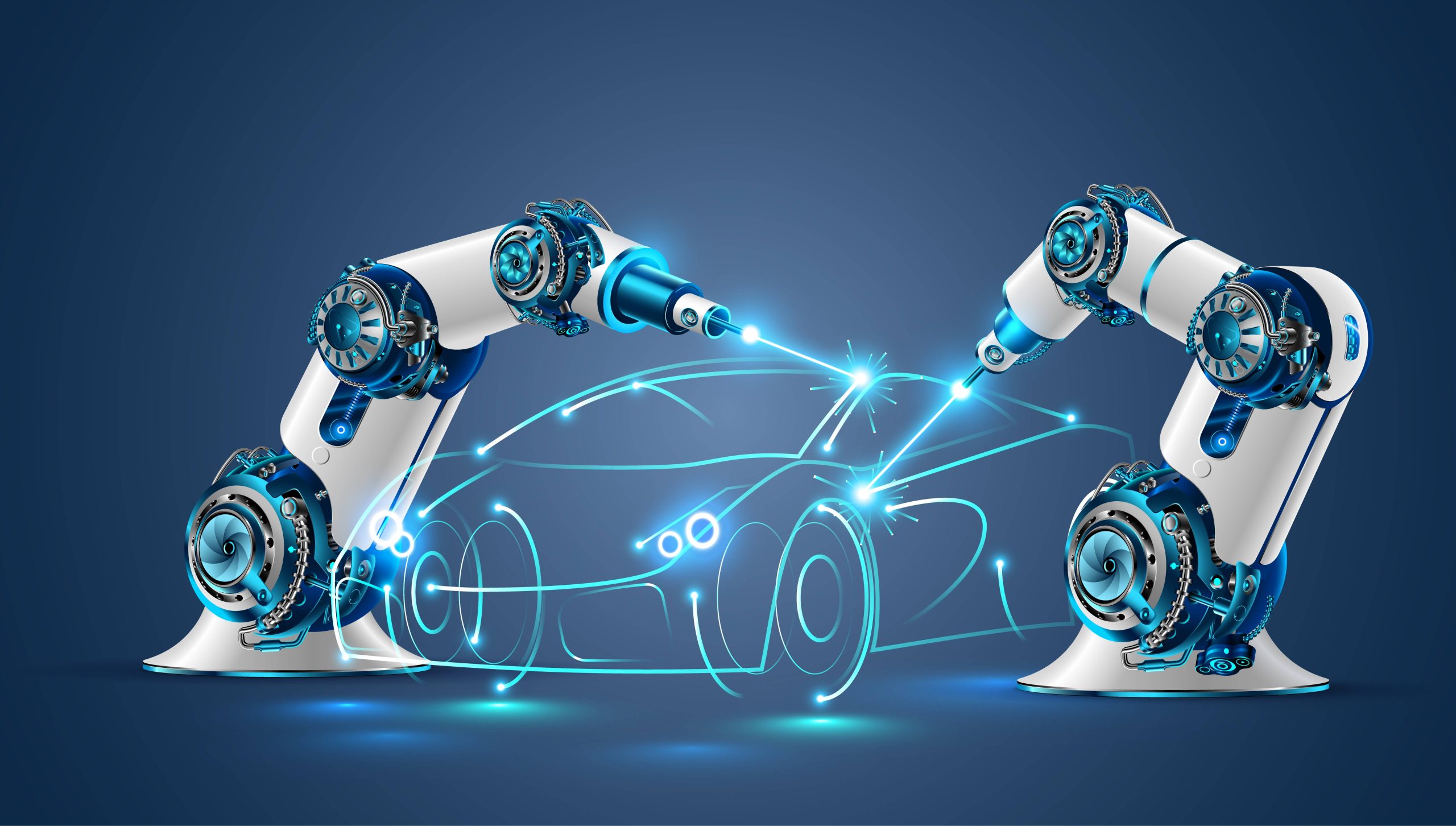
Ein führender Automobilzulieferer integrierte erfolgreich eine robotergestützte Laserschweißanlage für Sitzlehnenkomponenten. Die Anlage umfasste:
- FANUC 2000i Roboter
- IPG 4Kw Faserlaser
- HighYag RLSK Scanoptik
- PRECITEC LWM Schweißüberwachungssystem
Dieses integrierte System erzeugt 148 Schweißnähte in nur 45 Sekunden. Eine umfassende Schweißnahtprüfung stellt sicher, dass jede Schweißnaht strenge Qualitätsstandards erfüllt. Das System gewährleistet eine präzise Teileausrichtung, ermöglicht schnelle Umrüstungen und bietet die Flexibilität, verschiedene Modelle und Baugruppen zu verarbeiten.
Transformation der EV-Batterieproduktion
OPMT Laser entwickelte gemeinsam mit einem Kunden aus der Elektrofahrzeugbranche ein automatisiertes Laserschweißsystem zum Verbinden von Kupfersammelschienen mit Batterielaschen. Das sechsachsige Robotersystem gewährleistet gleichmäßige und wiederholbare Schweißnähte, verbessert die Sicherheit durch die Laserklasse 1 und steigert die Effizienz durch eine maßgeschneiderte Mensch-Maschine-Schnittstelle (HMI).
Das System unterstützt die Produktion mehrerer Teilenummern in einem einzigen Zyklus und bietet Funktionen zur Fernfehlerbehebung. Diese Integration verbessert die Konsistenz, Wiederholbarkeit und Effizienz des Schweißprozesses deutlich.
Qualitätswerkzeug- und Reparatur (QTR) Produktionsverbesserung
QTR, ein Unternehmen für Bearbeitung und Fertigung, führte zuvor manuelles Wolfram-Inertgasschweißen (WIG) mit einer Zykluszeit von 90 Minuten pro Bauteil durch. Nach der Implementierung des Cobot-Laserschweißens reduzierte sich die Zykluszeit auf nur 10 Minuten pro Bauteil – eine Verkürzung um 891 TP3T. Neben der drastischen Zeitersparnis beseitigte das Unternehmen weitere Probleme wie Verformungen, die zuvor beim WIG-Verfahren auftraten, und musste die Teile nach dem Schweißen nicht mehr reinigen.
Verbesserung der Elektromotorbaugruppe
Bei der Montage von Elektromotoren ist die Gewährleistung der Integrität und Qualität geschweißter Haarnadeln von entscheidender Bedeutung. Ein Hersteller implementierte den ZScan 360 von Senswork, ein fortschrittliches 3D-Inspektionssystem mit künstlicher Intelligenz (KI), um den Laserschweißprozess für Statoren zu überwachen.
Das System erfasst hochauflösende Daten von Schweißpunkten und nutzt Deep-Learning-Algorithmen, um die Schweißqualität in Echtzeit zu bewerten. Diese Implementierung erhöhte Präzision und Sicherheit im Schweißprozess, steigerte die Effizienz durch Automatisierung des Prüfprozesses und führte zu erheblichen Kosteneinsparungen durch die Minimierung von Defekten und Nacharbeitsbedarf.
Zukunftstrends: KI und IoT im Materialtransport
Die Zukunft der automatisierten Materialhandhabung beim CNC-Laserschweißen liegt in der Integration von künstlicher Intelligenz und Internet-of-Things-Technologien, die eine weitere Revolutionierung der Fertigungsprozesse versprechen.
KI-gesteuerte Optimierung
Künstliche Intelligenz revolutioniert die Automatisierung der Materialhandhabung, indem sie Arbeitsabläufe optimiert und Wartungsbedarf vorhersagt. KI-Implementierungen beim Laserschweißen umfassen:
- Routenoptimierung: KI ermittelt dynamisch die effizientesten Wege für fahrerlose Transportfahrzeuge und Roboter in Fertigungsumgebungen
- Aufgabenplanung: Modelle des maschinellen Lernens weisen Ressourcen in Echtzeit basierend auf Nachfrageschwankungen zu
- Qualitätsanalyse: Computer-Vision-Systeme analysieren die Schweißqualität, identifizieren Defekte und verbessern die Genauigkeit
- Anomalieerkennung: KI überwacht Sensordaten, um Unregelmäßigkeiten in der Geräteleistung zu erkennen, bevor es zu Ausfällen kommt
Diese KI-Systeme lernen kontinuierlich aus Betriebsdaten, verbessern ihre Leistung ständig und passen sich an veränderte Bedingungen an. Wie eine Branchenquelle feststellt: „KI verleiht der Fertigung ein neues Maß an Intelligenz und Anpassungsfähigkeit“ und verändert die Art und Weise, wie Aufgaben in Schweißereien ausgeführt werden, grundlegend.
IoT-Integration für Echtzeitüberwachung
IoT-Technologien verändern die Materialhandhabung beim Laserschweißen durch umfassende Überwachung und Systemoptimierung. Zu den IoT-Anwendungen gehören:
- Echtzeit-Parameterüberwachung: Sensoren überwachen Schneidparameter, Laserleistung, Linsenzustand und Temperaturen
- Drahtlose Kommunikation: Ermöglicht nahtlose Datenübertragung ohne physische Verbindungen
- Zentralisierte Datenerfassung: Informationen von mehreren Maschinen fließen an zentrale Analysesysteme
- Fernzugriff: Bediener können Systeme von überall aus überwachen und steuern, was Sicherheit und Komfort verbessert
Durch IoT können Maschinenbediener Schneid- und Schweißparameter in Echtzeit beobachten und erhalten bei auftretenden Problemen rechtzeitig Warnungen. Diese Funktion ermöglicht notwendige Anpassungen zur Qualitätssicherung und verbessert gleichzeitig die Sicherheit am Arbeitsplatz, da die physische Anwesenheit der Bediener während des Betriebs reduziert wird.
Vorausschauende Wartung durch Datenanalyse
Erweiterte Datenanalysen ermöglichen prädiktive Wartungsansätze, die Ausfallzeiten minimieren und die Lebensdauer der Geräte verlängern:
- Modelle zur Fehlervorhersage: Algorithmen für maschinelles Lernen analysieren historische Daten, um den Wartungsbedarf vorherzusagen
- Automatisierte Diagnose: KI-gestützte Diagnose identifiziert die Ursachen von Störungen
- Zustandsüberwachung: Kontinuierliche Beurteilung des Gerätezustands durch Sensordatenanalyse
Diese Funktionen stellen sicher, dass die Wartung auf Grundlage des tatsächlichen Gerätezustands und nicht nach festen Zeitplänen erfolgt. Dadurch werden ungeplante Ausfallzeiten erheblich reduziert und die Lebensdauer der Komponenten verlängert.
Neue Technologien am Horizont
Mehrere neue Technologien versprechen eine weitere Transformation der automatisierten Materialhandhabung beim Laserschweißen:
- Kollaborative Roboter (Cobots): Entwickelt, um Seite an Seite mit Menschen zu arbeiten und die Präzision der KI mit menschlichen Problemlösungsfähigkeiten zu kombinieren
- Fortschrittliche Faserlasersysteme: Verbesserte Laserquellen und Strahlführungstechnologien steigern die Gesamtleistung
- Echtzeit-Überwachungs- und Steuerungssysteme: Durch den Einsatz von Sensoren und Datenanalysen können Schweißprozesse kontinuierlich überwacht und sofortige Anpassungen vorgenommen werden
- 3D-Druck mit Schweißen: Integration der additiven Fertigung mit Schweißprozessen zur Herstellung komplexer Strukturen und kundenspezifischer Teile
Mit zunehmender Weiterentwicklung dieser Technologien werden sie ein noch höheres Maß an Präzision, Effizienz und Flexibilität bei CNC-Laserschweißvorgängen ermöglichen.
Abschluss
Die automatisierte Materialhandhabung hat das CNC-Laserschweißen grundlegend verändert und ein beispielloses Maß an Präzision, Effizienz und Konsistenz ermöglicht. Von Robotersystemen, die wiederholbare Qualität gewährleisten, bis hin zu KI- und IoT-Technologien, die Abläufe in Echtzeit optimieren, verändern diese Innovationen Fertigungsprozesse branchenübergreifend.
Bei der Implementierung dieser Technologien ist es für Hersteller entscheidend, die verfügbaren Optionen, Best Practices, potenziellen Herausforderungen und zukünftigen Trends zu verstehen. Durch die sorgfältige Auswahl der richtigen automatisierten Materialhandhabungslösungen und die Umsetzung bewährter Integrationsstrategien können Unternehmen erhebliche Produktivitätssteigerungen erzielen und gleichzeitig höchste Qualitätsstandards einhalten.
In einer Fertigungslandschaft, die immer höhere Effizienz und Präzision erfordert, stellt die automatisierte Materialhandhabung beim CNC-Laserschweißen einen entscheidenden Wettbewerbsvorteil dar. Unternehmen, die diese Technologien nutzen, positionieren sich an der Spitze der Innovation und sind bereit, die Herausforderungen der heutigen Produktionsumgebung zu meistern und sich gleichzeitig auf die Chancen von morgen vorzubereiten.
Haftungsausschluss
Dieser Inhalt wurde von OPMT Laser auf Grundlage öffentlich verfügbarer Informationen zusammengestellt und dient ausschließlich zu Referenzzwecken. Die Erwähnung von Marken und Produkten Dritter dient dem objektiven Vergleich und stellt keine kommerzielle Verbindung oder Billigung dar.