Is Your Manufacturing Strategy Prepared for the CNC Revolution?
As global manufacturers confront escalating demands for micron-level precision and digital transformation, 93% of machining facilities now prioritize upgrading legacy systems. At OPMT Laser, we empower this transition through cutting-edge solutions like our 5-Axis Vertical Machining Centers, which deliver unprecedented accuracy while addressing industry-wide sustainability challenges. This analysis decodes the dual forces reshaping CNC manufacturing—technological breakthroughs and supply chain evolution—and how OPMT’s innovations position clients at the forefront of precision engineering.
I. Technological Frontiers: Precision, Intelligence, Sustainability
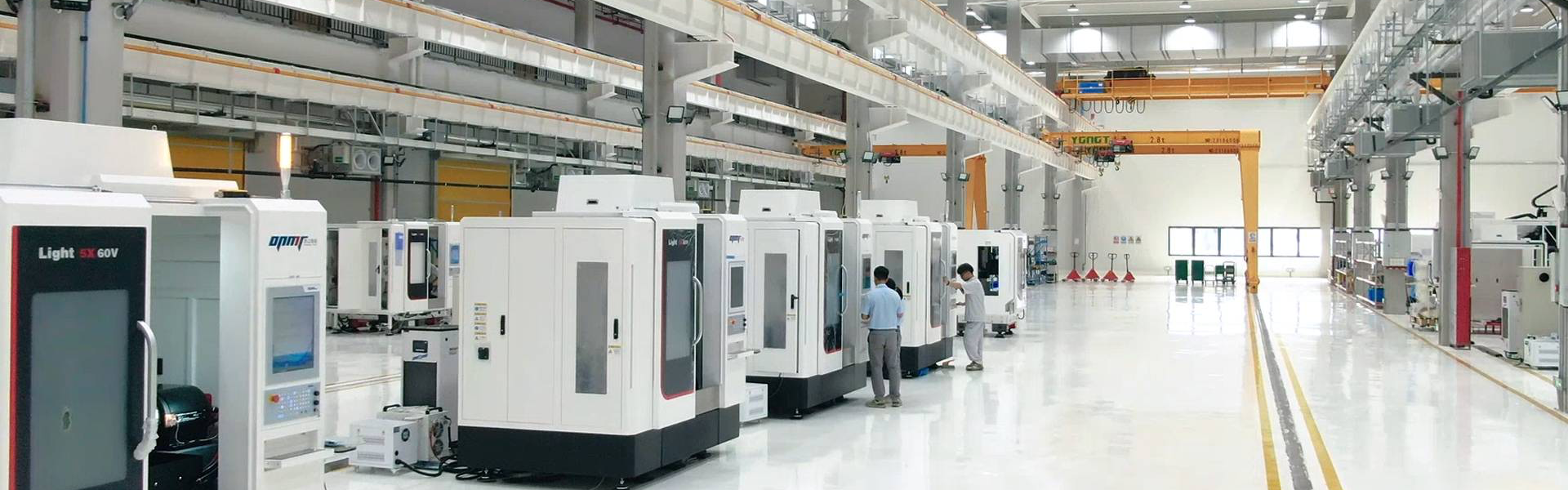
1. Ultra-Precision Redefined
OPMT’s 563V Vertical 5-Axis Machining Center exemplifies modern precision engineering, achieving spindle speeds of 200,000 RPM with 0.01μm synchronization accuracy. Our proprietary adaptive toolpath algorithms enable Ra0.4μm surface finishes, critical for aerospace turbine blades and medical implant manufacturing.
Industry Impact:
- Micro-drilling: 0.08mm holes with ±0.5μm positional accuracy for fuel injector nozzles
- Hybrid Laser Systems: Simultaneous cutting and surface texturing reduces production steps by 38% (see Laser Hybrid Solutions)
- Automotive Mold Production: 40% cost reduction through nano-surface machining (Ra3nm)
2. Intelligent Manufacturing Ecosystems
OPMT’s Smart Monitoring Platform integrates AI-driven predictive maintenance, achieving 92% accuracy in tool wear forecasting. Our IoT-enabled systems slash toolpath computation time by 67%, while digital twins optimize machining parameters in real time for complex geometries.
Client Case Study:
A European automotive supplier reduced downtime by 30% using OPMT’s adaptive control systems, dynamically adjusting feed rates and coolant flow during high-speed gear machining.
3. Sustainable Production Breakthroughs
OPMT’s Waterjet-Guided 5-Axis Systems eliminate cutting fluid waste, while our modular LP550V Laser Platforms achieve 85% component recyclability.
Technology | OPMT Implementation | Industry Benefit |
---|---|---|
Direct-Drive Motors | 40% energy savings | High-speed engraving |
Hybrid Cooling | 35% waste reduction | Continuous laser welding |
AI Material Optimization | 98% raw material utilization | Jewelry production |
II. Global Market Dynamics: OPMT’s Strategic Positioning
1. Regional Competitiveness
While Germany/Japan/US dominate 78% of ultra-precision markets, OPMT’s 5-Axis Machining Centers capture 12% growth in Asia-Pacific through localized production networks, reducing import dependency by 38%.
Market Differentiation:
- North America: IoT integration via OPMT Monitoring Platforms
- Europe: Collaborative R&D on quantum sensing for sub-micron accuracy
- Emerging Markets: Cost-optimized modular systems for SME adoption
2. Innovation Leadership
With 23 PCT patents in adaptive control algorithms, OPMT drives ISO 16090-1 safety standard updates. Our Ultrafast Laser Solutions enable compliance with evolving EU machinery directives through real-time laser power monitoring.
Client Success:
A medical device manufacturer achieved ISO 13485 certification using OPMT’s traceable machining processes for orthopedic implants.
III. Industrial Transformation: OPMT’s Ecosystem Integration
1. Vertical Collaboration Models
OPMT partners with material scientists to develop gradient carbide tools, boosting titanium machining efficiency by 40%—a breakthrough implemented in our Laser Hybrid Systems.
2. Service-Oriented Evolution
Our Machine-as-a-Service (MaaS) program converts capital expenditure to operational costs, offering:
- Hourly billing for 5-axis machining capacity
- Predictive maintenance contracts with 98% uptime guarantees
- Remote process optimization across global facilities
IV. Strategic Pathways for Industry Leadership
1. Technology Roadmap
OPMT’s R&D prioritizes:
- Quantum Manufacturing: Prototyping atomic-scale manipulation (0.01nm accuracy)
- Energy Autonomy: Solar-assisted machining centers targeting 50% energy self-sufficiency
- Bio-Integration: Pilot projects with medical institutes for cellular-level tissue fabrication
2. Talent Development
Through partnerships with technical universities, OPMT’s apprenticeship program certifies 500+ CNC specialists annually in AI-driven machining and sustainable practices.
Conclusion: Leading the Dual Transformation
The CNC industry’s future belongs to those mastering precision intelligence and circular production. OPMT Laser enables this transition through:
- Precision Quantum Leaps: Sub-micron accuracy across multi-axis systems
- Cognitive Manufacturing: AI-embedded controllers with real-time learning
- Sustainable Ecosystems: Closed-loop material/energy flows
Explore OPMT’s CNC Solutions to transform your manufacturing capabilities. From our award-winning 5-Axis Vertical Centers to revolutionary Laser Hybrid Technologies, we deliver the dual-engine power driving manufacturing’s next era.
Your Competitive Edge Starts Here.
Disclaimer
This content is compiled by OPMT Laser based on publicly available information for reference only; mentions of third-party brands and products are for objective comparison and do not imply any commercial association or endorsement.