The landscape of precision manufacturing continues to evolve rapidly in 2025, with CNC laser welding technology reaching new heights of sophistication and capability. Recent industry projections indicate that laser welding now accounts for 40% of all joining processes in consumer electronics production, underscoring its growing dominance across multiple sectors. For manufacturers seeking to enhance their production capabilities, selecting the appropriate CNC laser welding machine represents a critical strategic decision with far-reaching implications for productivity, quality, and competitive advantage.
This comprehensive guide will navigate you through the essential considerations when evaluating CNC laser welding machines in today’s market. We’ll examine how to assess your specific production requirements, analyze crucial technical features, compare leading suppliers, calculate return on investment, and ensure your purchase remains viable as technology continues to advance. With laser welding machines ranging from $10,000 to well over $100,000 depending on specifications, making an informed choice is more important than ever.
Understanding Your CNC Laser Welding Needs
The first step in selecting the ideal CNC laser welding machine involves a thorough assessment of your specific manufacturing requirements. This foundation will guide all subsequent decisions and help narrow your options to those that genuinely align with your production goals.
Manufacturing Volume and Production Requirements
Your expected production volume significantly influences the type of laser welding system you should consider. High-volume manufacturing operations typically benefit from machines with higher power outputs and automation capabilities. The latest models in 2025 offer exceptional duty cycles, with advanced cooling systems enabling continuous operation even in challenging environments from -20°C to 60°C. This represents a marked improvement over older generations of laser welders that required frequent cooling periods.
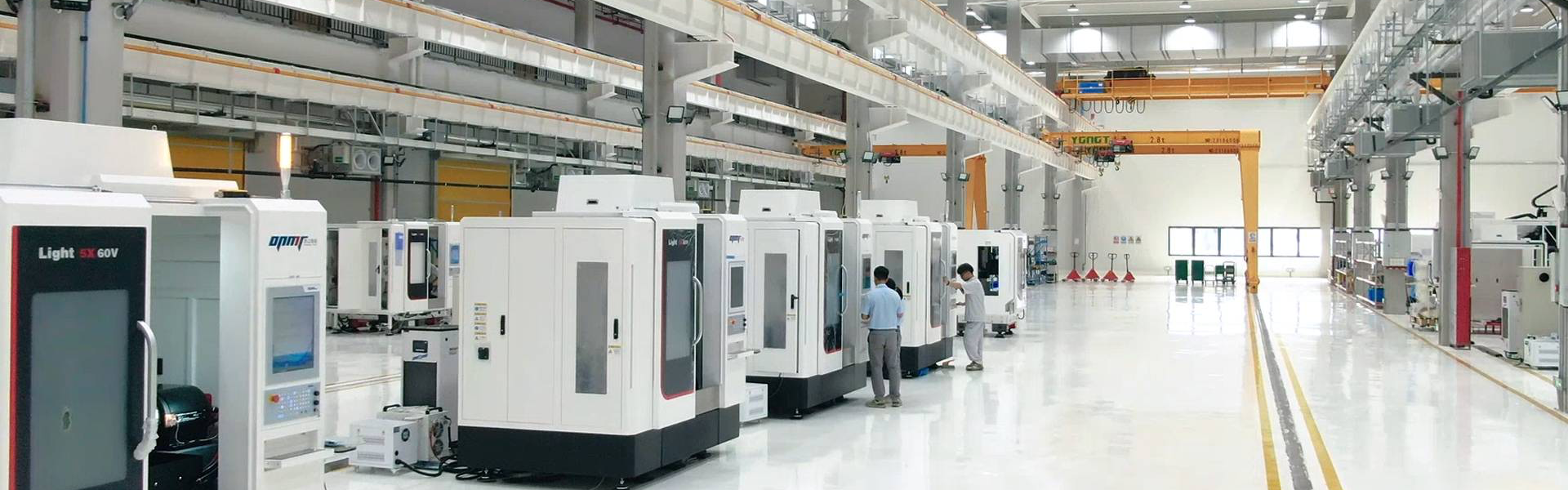
Manufacturing continuity is another crucial consideration. Modern high-performance systems like those offered by OPMT Laser can operate continuously for 24 hours, meeting demanding industrial production schedules without compromising performance. For enterprises with round-the-clock operations, this capability delivers significant advantages in throughput and reliability.
Material Types and Thickness Considerations
Different materials respond uniquely to laser welding, necessitating specific machine capabilities based on your primary applications. Advanced CNC laser welding machines in 2025 can effectively join a diverse range of metals, including stainless steel, carbon steel, aluminum, titanium, and various alloys. The versatility extends to handling dissimilar metals, such as copper-nickel, nickel-titanium, and carbon steel-copper combinations.
Material thickness represents another critical factor in machine selection. Higher-powered laser welders are essential for thicker materials, with specifications typically ranging from 1500W models capable of welding stainless steel up to 3mm thick to 3000W systems that can handle materials up to 6mm in thickness. These parameters must align with your typical workpiece requirements to ensure optimal results.
Specific Application Requirements
Industry-specific applications demand tailored laser welding solutions. In the automotive sector, where laser welding machines are revolutionizing body assembly with 35% faster production speeds, precision and reliability are paramount. Aerospace applications benefit from systems capable of producing joints that are 50% stronger than those achieved through conventional methods, particularly for turbine components and structural elements.
For manufacturers in electronics, requirements often center on precision and minimal heat distortion, especially for applications like battery sealing where 99.9% leak-proof results are expected. Medical device production demands exceptional precision, with laser welding enabling a 40% size reduction in implantable devices compared to traditional joining methods. Understanding these industry-specific benchmarks helps in selecting machines with appropriate capabilities for your unique applications.
Consulting with manufacturing technology experts like those at OPMT Laser can provide valuable insights into how different laser welding systems perform across various applications. Their expertise in advanced manufacturing technologies can help align your specific operational needs with the most appropriate technical specifications.
Key Features to Consider in Modern Laser Welding Machines
When evaluating CNC laser welding machines for purchase in 2025, several critical technical features merit careful consideration. These aspects directly impact performance, reliability, and overall value.
Laser Source Type and Power
The laser source serves as the heart of any welding system, with fiber lasers emerging as the dominant technology in 2025 due to their superior efficiency, reliability, and performance characteristics. Premium fiber laser sources, such as those from JPT incorporated in top-tier systems, offer exceptional service life, minimal failure rates, and superior anti-reflection properties. These advantages translate to consistent performance in demanding production environments.
Power output remains a fundamental consideration, with contemporary machines typically ranging from 1500W to 3000W for industrial applications. Higher power correlates directly with increased welding depth capability and production speed. When selecting power specifications, it’s advisable to choose a system that exceeds your current requirements by 20-30% to accommodate future projects and avoid limitations as your production needs evolve.
Precision Control Systems and Interfaces
Advanced control systems differentiate premium laser welding machines from basic alternatives. State-of-the-art CNC controllers facilitate intuitive operation while maintaining exceptional precision. Modern interfaces reduce operator training requirements while ensuring consistent results across production runs. This accessibility proves particularly valuable in manufacturing environments experiencing workforce transitions or skill shortages.
The OPMT Laser L03A model, for instance, exemplifies the latest developments in control technology, offering sophisticated programming capabilities while maintaining an accessible user experience. These advanced interfaces enable precise parameter adjustments that optimize weld quality across different materials and thicknesses.
Cooling System Efficiency
Thermal management represents a critical aspect of laser welding performance and longevity. Industrial-grade water chillers have become standard in premium systems, with capacity matched to laser source power. Advanced cooling technologies, such as the patented “Quad Core” refrigerant direct cooling system featured in some leading models, enable 100% duty cycles even in challenging environmental conditions.
Effective cooling systems prevent overheating, extend component lifespan, and ensure consistent welding quality during extended operations. When evaluating cooling capabilities, consider not only the chiller specifications but also the overall thermal management design, including how cooling is integrated with critical components like the welding head.
Automation and Integration Capabilities
As manufacturing increasingly embraces Industry 4.0 principles, integration capabilities have become essential features in modern laser welding systems. Leading machines offer comprehensive connectivity options for incorporation into automated production lines, robotic systems, and centralized control networks. These integration capabilities facilitate real-time monitoring, data collection, and process optimization.
Advanced systems now feature intelligent monitoring capabilities, with CCD cameras and blue light illumination enhancing visibility and precision. These visual systems enable operators to monitor welding progress in real-time, ensuring quality and consistency. Additionally, compatibility with robotic automation opens possibilities for enhanced productivity and reduced labor costs, with collaborative robots (cobots) emerging as accessible automation solutions for businesses of all sizes.
Mobility and Physical Specifications
Practical considerations like machine footprint, weight, and mobility can significantly impact integration into your existing manufacturing environment. Contemporary laser welding systems vary considerably in size, from compact handheld units to large integrated workstations. Workspace dimensions and layout constraints should inform your selection process.
Working table dimensions typically range from 500×300×300mm in standard models, with customization options available for specific applications. For operations with limited floor space, compact systems like the OPMT Laser LP550V offer substantial capabilities within minimal footprints. Conversely, comprehensive manufacturing centers like the L100V model provide expanded workspace for larger components.
Safety Features and Compliance
Safety considerations have gained heightened importance in contemporary manufacturing environments. Premium laser welding systems incorporate multiple safety mechanisms, including closed-loop welding protection, gas pressure monitoring, temperature protection, and emergency stop overrides. These features not only protect operators but also prevent equipment damage and ensure regulatory compliance.
Modern systems feature fully shielded laser cables, drawer-structured protective lenses for easy replacement, and air curtain components that reduce contamination from dust and splash residues. Look for machines with comprehensive safety certifications relevant to your region, such as CE marking for European markets, to ensure compliance with applicable regulations.
Comparing Top CNC Laser Welding Machine Suppliers
The CNC laser welding machine market features numerous suppliers offering diverse solutions. Understanding the strengths, specializations, and market positions of leading manufacturers helps inform purchasing decisions.
OPMT Laser: Advanced Multi-Axis Solutions
OPMT Laser, a division of Guangdong Original Point Intelligent Technology Co., Ltd., has emerged as a leading innovator in advanced laser processing solutions. Established in 2015 and headquartered in Guangdong Province, China, the company specializes in sophisticated multi-axis CNC laser systems and cutting-edge welding technologies.
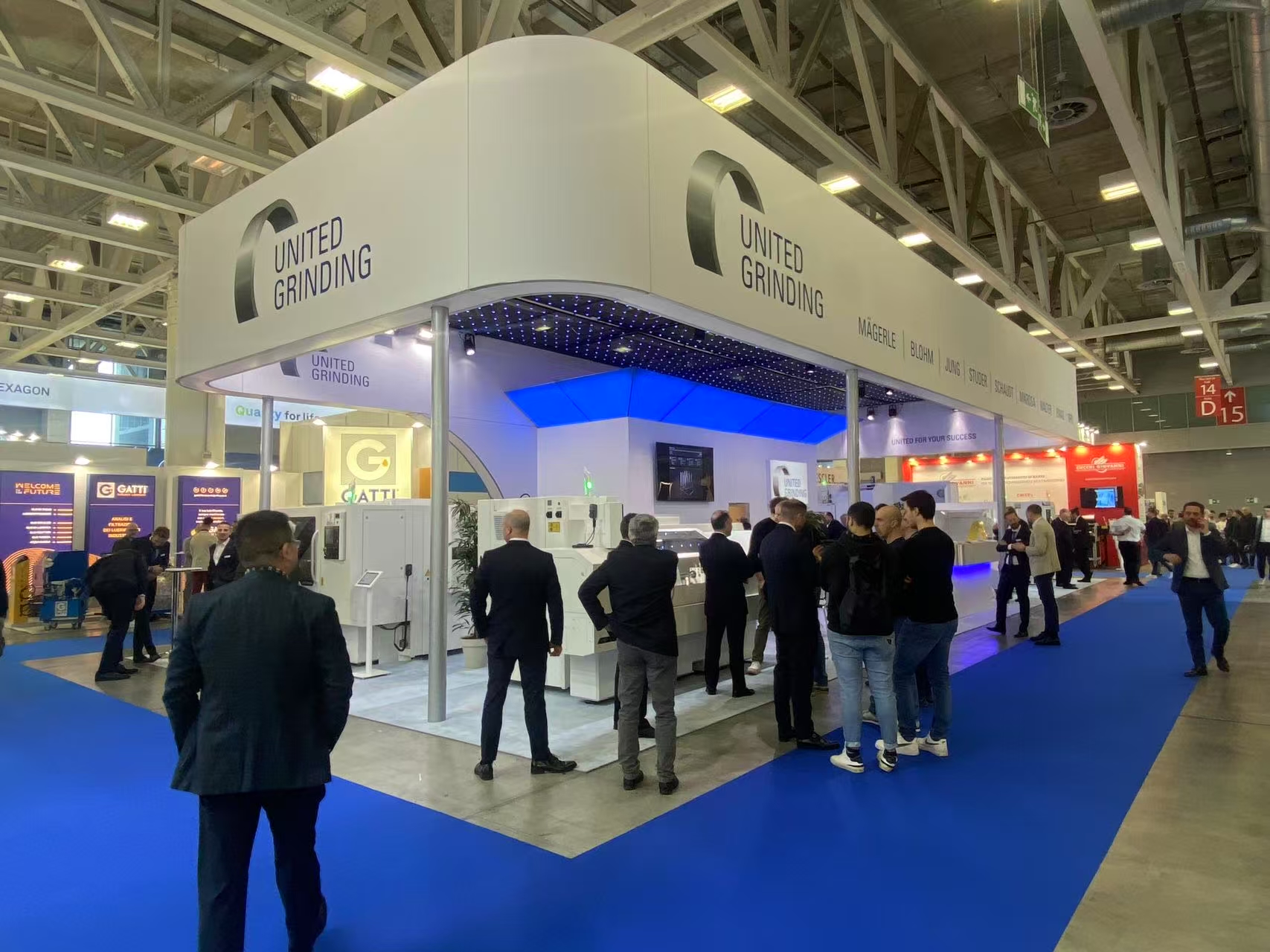
OPMT Laser distinguishes itself through comprehensive integration of state-of-the-art laser technology with precision engineering, advanced CNC controls, and custom software. Their flagship products serve as critical “mother machines” in modern manufacturing, offering unparalleled performance and versatility. The company’s extensive product line includes high-precision laser cutting equipment, innovative welding platforms, and specialized systems for mold texturing and tool grinding.
A key strength lies in OPMT Laser’s unwavering focus on innovation, particularly in beam shaping and trajectory control. This commitment to advancing technology positions them at the forefront of laser processing capabilities. Additionally, their tailored industrial solutions extend beyond hardware to comprehensive system integration and automation services, enabling end-to-end solutions that boost productivity and enhance precision across automotive, aerospace, and electronics manufacturing sectors.
TRUMPF: Global Leadership in Laser Technology
TRUMPF maintains its position as a global leader in manufacturing laser systems and machine tools, with headquarters in Ditzingen, Germany. Established in 1923, the company brings decades of experience to its comprehensive product portfolio in industrial laser applications.
Their laser welding systems excel in precision welding, efficiency, and adaptability across automotive, aerospace, and general manufacturing sectors. TRUMPF’s product lineup features cutting-edge solutions like the TruLaser Weld 5000, offering deep penetration welding, heat conduction welding, and FusionLine technology for gap-bridging joins. The company’s focus on complete laser-based manufacturing packages, including laser sources, beam delivery systems, and processing optics, establishes them as a one-stop solution provider for industrial laser welding requirements.
Han’s Laser: Extensive Production Capabilities
Han’s Laser, founded in 1996 and headquartered in Shenzhen, China, represents another significant player in the global laser equipment market. With production facilities spanning over 800,000 square meters, the company offers an impressive range exceeding 200 machine models, including advanced laser welding systems utilizing YAG, fiber, and semiconductor laser technologies.
A distinguishing characteristic of Han’s Laser lies in their substantial investment in research and development, with a significant portion of their workforce dedicated to innovation. This commitment has resulted in over 6,900 intellectual property rights, including pioneering ultraviolet laser patents. Their high-precision welding solutions excel in efficiency and cost-effectiveness across automotive, electronics, and medical device sectors.
Coherent: Specialized Industry Solutions
Coherent, established in 1971 and headquartered in Saxonburg, Pennsylvania, focuses on industrial lasers and precision manufacturing solutions. Their comprehensive suite of welding systems serves medical, automotive, electronics, and aerospace sectors.
Notable products include the ExactWeld 410, which exemplifies Coherent’s commitment to precision in medical device fabrication. This system features advanced Laser Framework software that streamlines process validation through intuitive machine vision and real-time monitoring. Additionally, their ARM FL20D fiber laser, with 20 kW output and dual ring beam configuration, accelerates welding speeds for challenging materials like cast aluminum.
Coherent distinguishes itself through exceptional customer support, maintaining 22 application labs across 11 countries for collaborative problem-solving. With over 50 global service centers and 650 expert engineers, the company ensures responsive maintenance and around-the-clock assistance worldwide.
Emerging Considerations in Supplier Selection
When comparing suppliers, consider factors beyond technical specifications. Service infrastructure, including local support availability, response times, and spare parts accessibility, significantly impacts long-term ownership experience. Training programs, application expertise, and willingness to provide test runs with your specific materials can indicate supplier commitment to customer success.
Additionally, evaluate software capabilities, as these increasingly determine system usability and integration potential. User-friendly interfaces, comprehensive parameter libraries, and remote diagnostic capabilities enhance productivity and reduce downtime. Some suppliers offer mobile applications for remote monitoring and adjustment, as seen with Strata’s Bluetooth app that enables real-time welding parameter adjustments without stopping production.
ROI Analysis: Justifying Your Investment
Calculating return on investment represents a critical step in the CNC laser welding machine acquisition process. This analysis quantifies financial benefits relative to costs, providing objective justification for the substantial capital expenditure these systems represent.
Understanding Total Cost of Ownership
Comprehensive cost evaluation extends well beyond the initial purchase price to encompass all expenses associated with acquiring, operating, and maintaining a laser welding system throughout its service life. Initial investment includes machine purchase, installation, facility modifications, and operator training. Operating costs encompass energy consumption, maintenance requirements, consumables, and labor expenses.
For laser welding machines specifically, consumable costs typically prove significantly lower than traditional welding methods, as these systems generally eliminate the need for filler materials in many applications. Energy efficiency varies substantially between models, with modern fiber laser systems offering electrical-to-optical conversion rates exceeding 30%, considerably higher than older technologies.
Maintenance requirements represent another significant consideration in total ownership cost. Advanced systems from manufacturers like OPMT Laser are designed for operational reliability, with modular components facilitating efficient servicing and minimizing downtime. Consider manufacturer-recommended maintenance schedules and associated costs when calculating comprehensive ownership expenses.
Quantifying Productivity Benefits
The exceptional speed of laser welding relative to conventional methods delivers substantial productivity advantages. Contemporary systems operate at speeds up to 10 times faster than traditional TIG welding, dramatically reducing cycle times and increasing production capacity. This speed advantage translates directly to labor cost reductions and enhanced throughput.
Quality improvements further contribute to ROI through reduced rework and scrap rates. The precision of modern laser welding produces stronger, more consistent joins with minimal distortion. This precision reduces post-processing requirements, as finished welds typically require little to no secondary processing—eliminating time-consuming grinding, buffing, or chemical cleaning operations.
Material efficiency gains provide additional cost benefits. Laser welding’s precision minimizes waste through more efficient material utilization. Additionally, the controlled heat input reduces distortion and preserves material properties, allowing the use of thinner base materials in many applications without compromising structural integrity.
Calculating ROI Using Standard Formulas
The standard ROI formula provides a straightforward method for evaluating investment efficiency:
ROI (%) = [(Net Profit from Investment – Cost of Investment) / Cost of Investment] × 100
For laser welding machines, net profit encompasses increased revenue from enhanced production capacity, reduced labor costs through higher throughput and automation, materials savings from reduced waste, decreased rework expenses due to improved quality, and lower consumable costs compared to traditional welding methods.
Consider a practical example: A manufacturer investing $150,000 in a fiber laser welding system achieves $200,000 in annual benefits through increased production and cost savings, yielding a net profit of $50,000. The ROI calculation would be:
ROI (%) = [($50,000) / $150,000] × 100 = 33.33%
This figure indicates that the investment generates a 33.33% return annually, allowing for complete cost recovery in approximately three years. This timeline aligns with industry expectations for advanced manufacturing equipment ROI.
Intangible Benefits Contributing to Value
Beyond quantifiable financial returns, laser welding machines deliver intangible benefits that contribute significantly to overall value. Enhanced product quality and consistency strengthen customer satisfaction and market reputation. The ability to handle complex geometries and join dissimilar materials enables product innovation and design flexibility that may create competitive advantages.
Workplace safety improvements represent another meaningful consideration. Laser welding produces fewer fumes than traditional methods, creating healthier work environments and potentially reducing associated regulatory compliance costs. Additionally, the reduced need for manual post-processing minimizes repetitive strain injuries and related workforce health issues.
Environmental benefits, including reduced energy consumption, decreased material waste, and lower emissions, align with sustainability initiatives and may contribute to regulatory compliance. These environmental advantages are increasingly valued by customers and stakeholders, potentially enhancing market position and brand perception.
Future-Proofing Your Purchase: Scalability and Upgrades
Technology investment decisions in 2025 must consider not only current requirements but also future developments and evolving production needs. Selecting laser welding equipment with appropriate upgradeability and expansion capabilities helps protect your investment against premature obsolescence.
Anticipating Technology Advancements
The laser welding industry continues to evolve rapidly, with several key trends shaping future developments. Automation capabilities represent a significant area of advancement, with machine learning algorithms increasingly enabling adaptive control during welding processes. These systems adjust laser parameters in real-time based on material characteristics and welding conditions, ensuring optimal results across varying production scenarios.
The incorporation of ultrafast lasers with femtosecond and picosecond pulse durations is expanding applications for heat-sensitive materials. These advanced laser sources produce minimal heat-affected zones, enabling welding of previously incompatible materials. Similarly, green lasers are gaining prominence for their effectiveness with reflective materials like copper, brass, and gold, opening new possibilities in electronics manufacturing and other specialized applications.
Predictive maintenance capabilities enhanced by artificial intelligence represent another significant advancement. These systems monitor equipment performance and predict potential failures before they occur, minimizing unplanned downtime and optimizing service intervals. When evaluating systems, consider the manufacturer’s roadmap for incorporating these emerging technologies through updates and upgrades.
Modularity and Upgrade Pathways
Truly future-proof laser welding systems offer modular architectures that facilitate component upgrades without requiring complete system replacement. Look for machines designed with standardized interfaces and modular subsystems that can be individually upgraded as technology advances or requirements change.
Some manufacturers offer performance upgrade packages that enhance existing systems through laser source upgrades, control system updates, or accessory additions. These pathways provide cost-effective means of extending equipment capabilities without full replacement costs. Inquire specifically about manufacturers’ histories of supporting existing customers with upgrade options for previously purchased systems.
Integration capabilities with emerging technologies like additive manufacturing represent another important consideration. The boundary between additive processes and laser welding continues to blur, with technologies like Wire Laser Additive Manufacturing (WLAM) and Laser Metal Deposition with wire (LMD-w) gaining prominence across various industries. Systems designed with flexible configurations may accommodate these emerging applications through appropriate upgrades.
Scalability for Changing Production Volumes
Production requirements invariably evolve over time, making scalability a crucial consideration in equipment selection. Some laser welding systems offer modular workholding solutions that accommodate different component sizes and production volumes. These flexible configurations adapt to changing requirements without necessitating additional capital investment.
Automation compatibility ensures systems can evolve from manual operation to semi-automated or fully automated workflows as production volumes increase. Machines with standardized interfaces for robotic integration provide clear pathways to higher throughput as demand grows. The emerging trend toward collaborative robots in welding operations offers particularly accessible automation options, with easier programming and adaptability making them suitable for smaller operations transitioning toward higher production volumes.
Software scalability represents an equally important consideration. Systems with adaptable software architectures accommodate additional capabilities through programming updates rather than hardware changes. Look for manufacturers with established histories of providing software updates that enhance functionality and compatibility with evolving production management systems.
Supplier Longevity and Support Commitment
Perhaps the most fundamental aspect of future-proofing your investment lies in selecting suppliers with demonstrated longevity and support commitment. Established manufacturers with proven histories of supporting installed equipment through technological transitions provide greater assurance of continued relevance.
Service infrastructure longevity deserves particular attention. Suppliers maintaining comprehensive spare parts inventories for older systems demonstrate commitment to supporting existing customers. Similarly, those offering retrofit packages to bring older systems in line with current capabilities show dedication to maintaining equipment relevance throughout its service life.
Technical training programs represent another indicator of long-term support. Manufacturers providing comprehensive operator and maintenance training, along with ongoing educational resources as technology evolves, demonstrate commitment to customer success. These resources ensure your team can maximize equipment utility throughout its operational lifespan.
Conclusion: Making an Informed Decision
Selecting the optimal CNC laser welding machine for your manufacturing operation in 2025 requires careful consideration of numerous factors, from technical specifications and supplier capabilities to financial analysis and future adaptability. The most successful acquisitions result from thorough evaluation processes that align equipment capabilities precisely with both current requirements and anticipated future needs.
The transformative impact of laser welding technology across manufacturing sectors continues to accelerate, with applications expanding beyond traditional boundaries. Systems offering the flexibility to adapt to these evolving opportunities provide the greatest long-term value. By thoroughly assessing your specific production requirements, evaluating critical technical features, comparing leading suppliers, calculating comprehensive ROI, and considering future adaptability, you position your operation to capitalize fully on the precision, efficiency, and versatility that modern laser welding technology offers.
For manufacturers seeking additional guidance in navigating these complex considerations, OPMT Laser offers comprehensive consultation services tailored to specific production requirements. Their expertise in advanced laser processing solutions helps align equipment capabilities precisely with manufacturing objectives, ensuring optimal investment outcomes. As laser welding technology continues its rapid evolution, informed equipment selection remains fundamental to manufacturing competitiveness and success.
Disclaimer
This content is compiled by OPMT Laser based on publicly available information for reference only; mentions of third-party brands and products are for objective comparison and do not imply any commercial association or endorsement.