In today’s competitive manufacturing landscape, the integration of automation in CNC laser welding represents a transformative approach to boosting productivity, precision, and operational efficiency. This comprehensive guide explores how automated material handling systems are revolutionizing laser welding operations, providing manufacturers with the insights needed to implement these technologies effectively.
The Role of Automation in Modern CNC Laser Welding
The evolution of laser welding technology has fundamentally changed manufacturing processes across industries. Automation has become the cornerstone of this transformation, elevating the capabilities of laser welding systems to unprecedented levels.
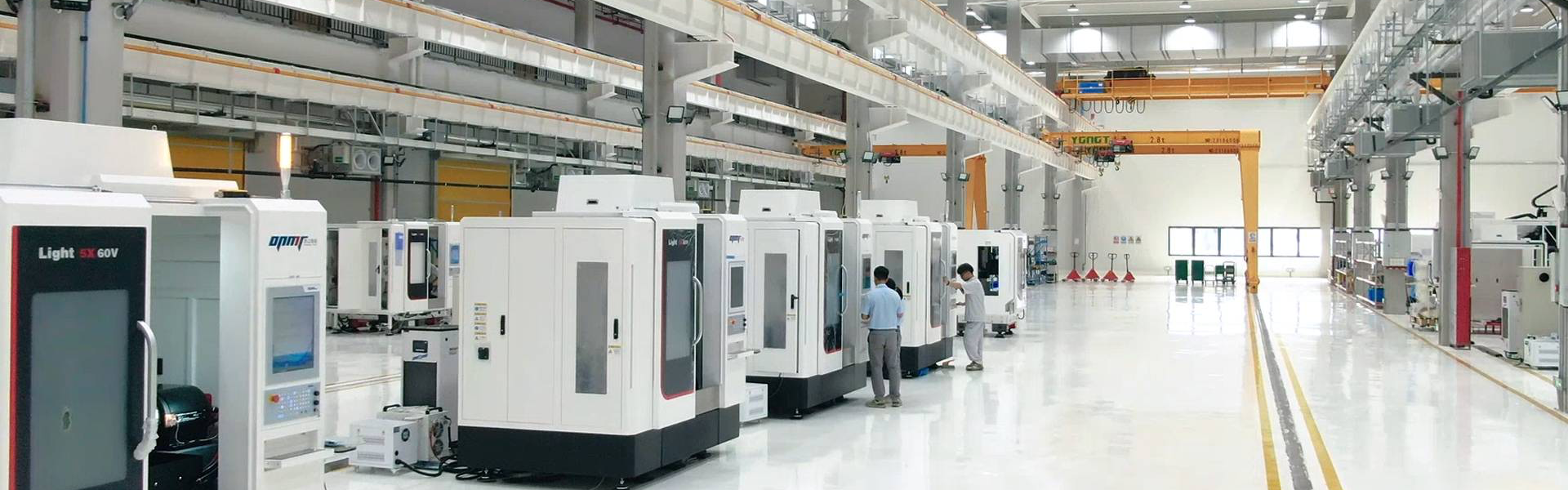
Key Benefits Driving Automation Adoption
Automation in laser welding delivers multiple advantages that traditional manual processes cannot match. The precision of a finely focused laser beam allows for exact control over the welding area, ensuring only targeted material is affected, which significantly reduces the heat-affected zone and minimizes distortion. With automated systems, manufacturers achieve consistent, high-quality welds with repeatability that human operators simply cannot match.
The speed enhancement is equally impressive. What once took 90 minutes with manual gas-tungsten-arc welding (GTAW) can now be completed in just 10 minutes using automated laser welding systems. This dramatic reduction in cycle time translates directly to increased throughput and improved productivity.
Beyond speed and precision, automated laser welding systems offer:
- Reduced labor costs through minimized human intervention
- Enhanced safety by limiting worker exposure to hazardous environments
- Decreased material waste and rework requirements
- Flexibility to handle various materials and thicknesses
- Real-time monitoring capabilities for quality control
Evolution of Laser Technology
The transition from traditional CO2 lasers to advanced fiber lasers has been instrumental in enhancing automation capabilities. Fiber lasers provide more stable and consistent output, which is essential for maintaining high-quality welds. They’re faster, more precise, and require less maintenance, making them ideal for automated welding processes.
Types of Automated Material Handling Systems for Laser Welding
Implementing the right material handling solution is crucial for maximizing the efficiency of CNC laser welding operations. Several options exist, each with distinct advantages for specific applications.
Robotic Systems
Robots represent the cornerstone of modern automated material handling in laser welding. They perform tasks with exceptional precision and repeatability, significantly enhancing production efficiency. The most common robotic systems include:
- Six-axis articulated robots: Provide maximum flexibility for complex welding paths and positions
- SCARA (Selective Compliance Assembly Robot Arm) robots: Excellent for specific applications like clamping tabs to busbars
- Collaborative robots (cobots): Designed to work alongside humans, handling repetitive tasks while allowing operators to focus on more complex aspects
Robotic systems excel at maintaining consistent weld quality by positioning laser heads with exceptional accuracy and following programmed paths precisely. They’re particularly valuable in high-volume production environments where thousands of welds must be performed with consistent quality.
Conveyor Systems and Transfer Mechanisms
Automated conveyor systems ensure smooth part flow through the welding process. These systems can include:
- Linear transfer systems: Move parts in a straight line through the welding station
- Rotary indexing tables: Position parts at precise angles for complex welding operations
- Pallet exchange systems: Allow for loading/unloading while welding continues uninterrupted
These systems optimize workflow by minimizing downtime between operations and maintaining a steady production pace.
Ready-to-Integrate Packages
For manufacturers looking to streamline implementation, ready-to-integrate laser welding packages offer significant advantages. These comprehensive solutions typically include:
- Lasers and beam-delivery systems
- Machine vision components
- Process monitoring tools
- Robotic integration hardware/software
- User-friendly control interfaces
These packages significantly reduce setup time and development costs associated with custom configurations. They feature advanced monitoring capabilities through machine vision and real-time process monitoring, ensuring precise laser beam alignment and detecting anomalies during welding.
Comparison of Automated Handling Systems
System Type | Best Applications | Advantages | Limitations |
---|---|---|---|
6-Axis Robots | Complex 3D welds, varied part geometries | Maximum flexibility, large work envelope, high precision | Higher initial cost, more complex programming |
SCARA Robots | Repetitive tasks, planar applications | Fast cycle times, good precision, lower cost | Limited to simpler movements, smaller work area |
Cobots | Small batch production, human-collaborative environments | Easy programming, flexible deployment, safety features | Lower payload capacity, slower operation speeds |
Conveyor Systems | High-volume production, linear part flow | Continuous operation, consistent timing, scalable | Less flexible for varied part types, fixed pathways |
Ready-to-Integrate | New adopters, standardized applications | Faster implementation, reduced integration complexity | May require adaptations for unique requirements |
Implementing Robotic Systems: Best Practices and Challenges
Successfully implementing robotic systems for material handling in laser welding requires careful planning and consideration of several key factors.
Best Practices for Robotic Integration
When integrating robots with CNC laser welding equipment, consider these proven approaches:
- Conduct thorough process analysis before implementation to identify bottlenecks and opportunities for automation
- Choose robots with appropriate payload capacity, reach, and precision for your specific welding applications
- Implement comprehensive safety features including Class 1 laser enclosures for safe operation
- Design fixtures and part presentation systems that ensure consistent part positioning
- Utilize off-line programming capabilities to minimize production downtime during setup
- Invest in training for operators and maintenance personnel
Proper integration requires attention to both hardware and software aspects. Manufacturers should prioritize systems with user-friendly interfaces that enable easy programming and adjustment of welding parameters through touch screen controls.
Common Integration Challenges and Solutions
Despite the benefits, implementing robotic material handling systems presents several challenges:
- High Initial Investment: Robotic welding systems require significant upfront costs, including installation and training.
- Solution: Start with smaller-scale implementation focused on high-volume parts, then expand as ROI is demonstrated.
- Complex Setup and Programming: Setting up and programming robotic welders demands specialized skills and knowledge.
- Solution: Utilize weld cameras and monitoring systems to simplify troubleshooting and setup by providing clear views of weld quality.
- Material and Task Limitations: Robots may struggle with complex welds on varying materials or in challenging positions.
- Solution: Integrate advanced vision systems and adaptive programming to enhance flexibility.
- Maintenance Requirements: Regular maintenance is critical to ensure long-term performance.
- Solution: Implement predictive maintenance programs using IoT sensors to monitor system health and prevent unplanned downtime.
Key Considerations for Implementation
Before implementing automated material handling for laser welding, manufacturers should assess:
- Production volume and mix: Higher volumes with less variety benefit most from full automation
- Part characteristics: Size, weight, material, and complexity affect handling requirements
- Budget constraints: Balance initial investment against long-term operational savings
- Available floor space: Robotic cells require appropriate clearance and safety zones
- Integration with existing systems: Ensure compatibility with upstream and downstream processes
Case Studies: Productivity Gains Through Automation
Real-world implementations demonstrate the tangible benefits of automated material handling in laser welding operations.
Automotive Component Manufacturing
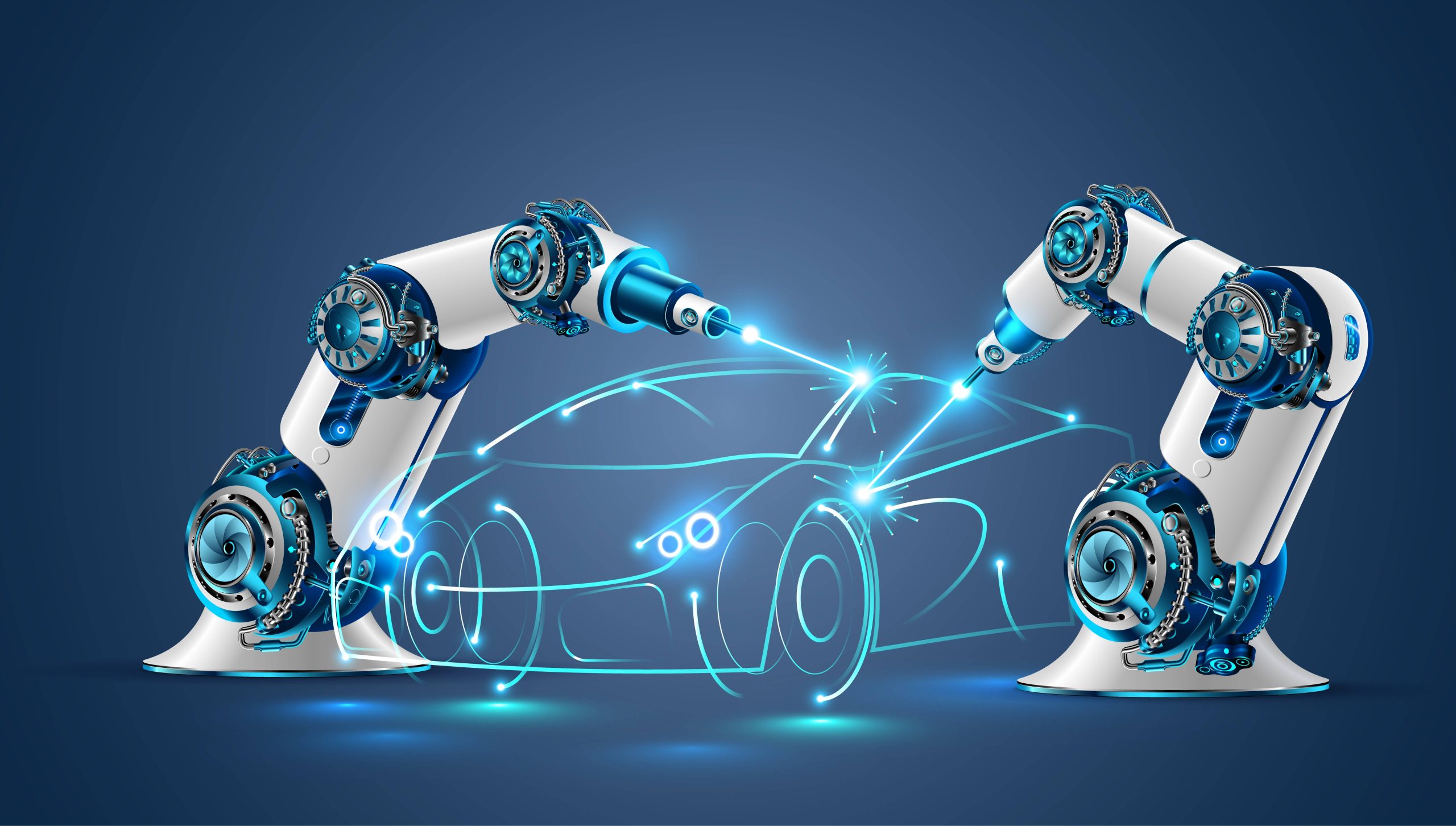
A leading automotive supplier successfully integrated a robot-assisted laser welding system for seat back components. The system included:
- FANUC 2000i robot
- IPG 4Kw fiber laser
- HighYag RLSK scanning optics
- PRECITEC LWM weld monitoring system
This integrated system produces 148 welds in just 45 seconds, with comprehensive weld inspection ensuring each weld meets stringent quality standards. The system maintains tight part alignment, allows for quick changeovers, and provides flexibility to run different models and assemblies.
EV Battery Production Transformation
OPMT Laser collaborated with an electric vehicle industry customer to create an automated laser welding system for joining copper busbars to battery tabs. The six-axis robotic system ensures consistent and repeatable welds, improving safety with a Class 1 laser designation and enhancing efficiency through a customized Human-Machine Interface (HMI).
The system supports production of multiple part numbers in a single cycle and includes remote troubleshooting capabilities. This integration significantly improved consistency, repeatability, and efficiency in the welding process.
Quality Tooling & Repair (QTR) Production Improvement
QTR, a machining and fabrication company, previously performed manual gas-tungsten-arc welding (GTAW) at a rate of 90 minutes per component. After implementing cobot laser welding, they reduced cycle time to just 10 minutes per component—an 89% reduction. Beyond the dramatic time savings, the company eliminated other problems such as distortion previously encountered with the GTAW process and no longer needed to clean parts after welding.
Electric Motor Assembly Enhancement
In the assembly of electric motors, ensuring the integrity and quality of welded hairpins is critical. A manufacturer implemented Senswork’s ZScan 360, an advanced 3D inspection system leveraging artificial intelligence (AI) to monitor the laser welding process for stators.
The system captures high-resolution data of welding spots and uses deep learning algorithms to evaluate weld quality in real-time. This implementation increased precision and safety in the welding process, improved efficiency through automation of the inspection process, and generated significant cost savings by minimizing defects and rework needs.
Future Trends: AI and IoT in Material Handling
The future of automated material handling in CNC laser welding lies in the integration of artificial intelligence and Internet of Things technologies, which promise to further revolutionize manufacturing processes.
AI-Driven Optimization
Artificial intelligence is revolutionizing material handling automation by optimizing workflows and predicting maintenance needs. AI implementations in laser welding include:
- Route Optimization: AI dynamically determines the most efficient paths for automated guided vehicles and robots in manufacturing environments
- Task Scheduling: Machine learning models allocate resources in real-time based on demand fluctuations
- Quality Analysis: Computer vision systems analyze weld quality, identifying defects and improving accuracy
- Anomaly Detection: AI monitors sensor data to detect irregularities in equipment performance before failures occur
These AI systems continuously learn from operational data, constantly improving their performance and adapting to changing conditions. As one industry source notes, “AI injects a new level of intelligence and adaptability into manufacturing,” fundamentally transforming how tasks are executed in welding shops.
IoT Integration for Real-Time Monitoring
IoT technologies are transforming material handling in laser welding through comprehensive monitoring and system optimization. IoT applications include:
- Real-Time Parameter Monitoring: Sensors track cutting parameters, laser power, lens health, and temperatures
- Wireless Communication: Enables seamless data transmission without physical connections
- Centralized Data Collection: Information from multiple machines flows to central analysis systems
- Remote Access: Operators can monitor and control systems from anywhere, improving safety and convenience
Through IoT, machine operators can observe cutting and welding parameters in real-time, receiving timely warnings if issues arise. This capability allows for necessary adjustments to maintain quality while improving workplace safety by reducing the need for operators to be physically present during operations.
Predictive Maintenance Through Data Analysis
Advanced data analysis enables predictive maintenance approaches that minimize downtime and extend equipment life:
- Failure Prediction Models: Machine learning algorithms analyze historical data to forecast maintenance needs
- Automated Diagnostics: AI-assisted diagnostics identify root causes of malfunctions
- Condition Monitoring: Continuous assessment of equipment health through sensor data analysis
These capabilities ensure that maintenance occurs based on actual equipment condition rather than fixed schedules, significantly reducing unplanned downtime while extending component lifespans.
Emerging Technologies on the Horizon
Several emerging technologies promise to further transform automated material handling in laser welding:
- Collaborative Robots (Cobots): Designed to work alongside humans, combining the precision of AI with human problem-solving skills
- Advanced Fiber Laser Systems: Improved laser sources and beam delivery technologies enhancing overall performance
- Real-Time Monitoring and Control Systems: Using sensors and data analytics to continuously monitor welding processes and make immediate adjustments
- 3D Printing with Welding: Integrating additive manufacturing with welding processes to create complex structures and custom parts
As these technologies mature, they will enable even greater levels of precision, efficiency, and flexibility in CNC laser welding operations.
Conclusion
Automated material handling has fundamentally transformed CNC laser welding, delivering unprecedented levels of precision, efficiency, and consistency. From robotic systems that ensure repeatable quality to AI and IoT technologies that optimize operations in real-time, these innovations are reshaping manufacturing processes across industries.
As manufacturers navigate the implementation of these technologies, understanding the available options, best practices, potential challenges, and future trends becomes essential for success. By carefully selecting the right automated material handling solutions and following proven integration strategies, companies can achieve substantial productivity gains while maintaining the highest quality standards.
In a manufacturing landscape that demands ever-greater efficiency and precision, automated material handling in CNC laser welding stands as a critical competitive advantage. Companies that embrace these technologies position themselves at the forefront of innovation, ready to meet the challenges of today’s production environment while preparing for the opportunities of tomorrow.
Disclaimer
This content is compiled by OPMT Laser based on publicly available information for reference only; mentions of third-party brands and products are for objective comparison and do not imply any commercial association or endorsement.