Are you struggling to achieve the precision and accuracy your manufacturing projects demand? Imagine a solution that delivers micrometer-level accuracy while handling the most intricate designs with ease. Laser ultra-precision machining is revolutionizing industries like medical devices, electronics, and optics, offering unmatched quality and efficiency. At OPMT Laser, we specialize in cutting-edge laser technology, such as the Micro3DL530V and L03A, designed to elevate your production capabilities.
In this article, you’ll discover the key benefits of laser ultra-precision machining, from its ability to produce complex geometries to its role in reducing material waste. Did you know that laser machining can achieve tolerances as tight as ±1 micron? Whether you’re new to the field or looking to optimize your processes, this guide will show you how OPMT Laser’s innovative solutions can transform your workflow. Ready to see how precision meets performance? Keep reading to learn more!
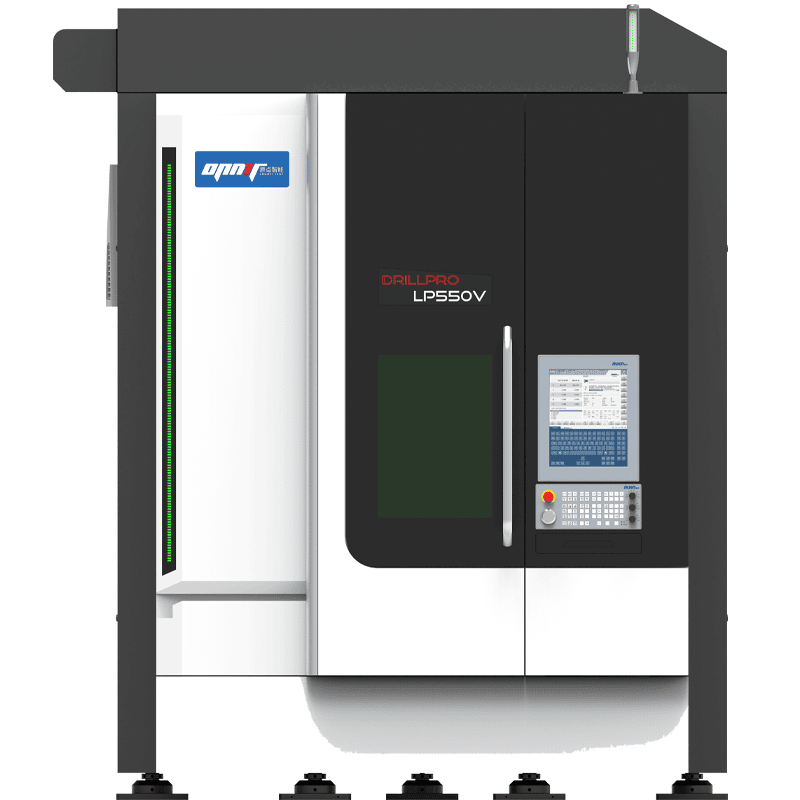
Unmatched Precision and Accuracy
Laser machining delivers exceptional precision, achieving tolerances as tight as ±0.05 mm or smaller. This level of accuracy is vital for industries requiring exact specifications, such as medical devices and electronics. The laser beam’s narrow kerf width, ranging from 0.1 mm to 1 mm, ensures optimal material utilization, reducing waste and enhancing efficiency. OPMT Laser’s advanced systems, like the Micro3DL530V, are designed to meet these high standards, ensuring consistent results for manufacturers.
Versatility Across Materials
One of the key strengths of laser technology is its ability to process a wide range of materials, including metals, ceramics, and polymers. This versatility enables the creation of intricate designs and complex geometries that traditional methods struggle to achieve. For example, OPMT Laser’s L03A system is engineered to handle diverse materials with ease, ensuring high-quality outcomes across various industries.
Minimized Material Waste
Laser cutting systems, equipped with advanced nesting software, optimize material layouts, reducing scrap rates by up to 30% compared to conventional methods. The precision of laser technology also minimizes the heat-affected zone (HAZ), preserving material integrity and preventing warping or distortion. OPMT Laser’s LP550V exemplifies this commitment to sustainability, helping manufacturers achieve both efficiency and environmental responsibility.
Cost-Effective Manufacturing Solutions
The high accuracy of laser machining eliminates the need for secondary finishing processes, significantly lowering production costs. By removing the requirement for physical tooling, OPMT Laser’s systems, such as the DIACUT L315V, reduce initial setup expenses and allow for rapid design adjustments without additional costs. This cost-effectiveness makes laser technology an ideal choice for businesses aiming to streamline operations.
Automation for Enhanced Efficiency
Laser systems operate at remarkable speeds, outperforming traditional machining methods and boosting productivity. CNC-controlled laser systems from OPMT Laser, like the LightMut 750V, ensure consistent quality across large production runs, reducing variations between parts and minimizing the need for extensive quality control. This automation translates to faster turnaround times and improved operational efficiency.
Superior Surface Finishes
Laser machining produces components with exceptional surface quality, often eliminating the need for additional processing. This is particularly beneficial in industries like optics and medical devices, where surface integrity is critical. OPMT Laser’s Light-5X-60V delivers clean, precise cuts, saving time and labor costs while maintaining the highest standards of quality.
Why Choose OPMT Laser for Ultra-Precision Machining?
OPMT Laser stands at the forefront of laser machining innovation, offering cutting-edge solutions that combine precision, versatility, and cost-effectiveness. Our systems, such as the LightGrind LT20, are designed to meet the evolving needs of modern manufacturing, ensuring superior results across a wide range of applications. By partnering with OPMT Laser, businesses can achieve unparalleled efficiency and quality in their production processes.
What makes laser machining more precise than traditional methods?
Laser machining achieves tolerances as tight as ±0.05 mm, thanks to its focused beam and advanced control systems.
Can laser technology process multiple materials?
Yes, laser systems can effectively work with metals, ceramics, polymers, and more, making them highly versatile.
How does laser cutting reduce material waste?
Advanced nesting software optimizes material layouts, while the narrow kerf width minimizes excess scrap.
Is laser machining cost-effective for small-scale production?
Absolutely. The elimination of physical tooling and secondary finishing processes reduces costs, making it suitable for both small and large-scale operations.
Conclusion
Imagine achieving micrometer-level precision in your manufacturing processes while minimizing waste and maximizing efficiency. Laser ultra-precision machining offers a solution that addresses the challenges of accuracy and versatility, making it a game-changer for industries like medical devices and electronics. At OPMT Laser, our advanced systems, such as the Micro3D-L530V and LP550V, are engineered to help you meet stringent specifications without compromising on quality.
You’ve discovered how laser technology not only reduces material waste but also enhances operational efficiency and cost-effectiveness. Did you know that laser machining can achieve tolerances as tight as ±1 micron? With OPMT Laser’s innovative solutions, you can elevate your production capabilities and stay ahead in a competitive market. Ready to explore how our cutting-edge products can transform your workflow? Dive deeper into OPMT Laser’s offerings today!
Disclaimer
This content is compiled by OPMT Laser based on publicly available information for reference only; mentions of third-party brands and products are for objective comparison and do not imply any commercial association or endorsement.