Evolving Demands in Luxury Jewelry Production
The jewelry industry is experiencing unprecedented transformation in 2025, with the global jewelry cutting machine market projected to reach $1,748.5 million this year, driven by growing consumer demand for increasingly intricate designs. Are traditional diamond cutting methods keeping pace with these evolving expectations? The evidence suggests otherwise. According to recent market analysis, over 60% of jewelers report wasting 15+ hours weekly on imperfect cuts using outdated equipment, highlighting the critical need for advanced processing solutions.
Traditional jewelry manufacturing methods like grinding and chemical etching frequently compromise cutting edge quality, directly affecting both precision and production efficiency. When processing diamonds and other superhard materials with conventional techniques such as Electrical Discharge Machining (EDM), manufacturers encounter persistent challenges including edge chipping, material cracking, and wire skipping issues when working with poor-conductivity materials. These limitations create significant bottlenecks for luxury jewelry producers aiming to meet rising consumer expectations.
The market for handmade and custom jewelry is projected to grow at a remarkable CAGR of 13.3% through 2030, with Asia-Pacific leading at 8.7% growth followed closely by North America at 8.9%. This expansion reflects changing consumer preferences, with today’s luxury jewelry buyers expecting flawless execution, complex geometries, and unique designs that traditional manufacturing methods struggle to deliver consistently. OPMT Laser’s advanced processing solutions address these exact challenges, enabling jewelers to achieve the precision and complexity modern consumers demand.
Multi-Axis Laser Technology for Jewelry Applications
OPMT Laser’s multi-axis CNC laser systems represent a technological breakthrough for jewelry manufacturers seeking superior precision and design flexibility. The company’s Light 5X series of vertical 5-axis laser machining centers achieve exceptional positioning accuracy of 0.005 mm (5 microns) with repeat positioning accuracy of 0.003 mm – critical specifications for creating jewelry with complex geometries and flawless finishes. These systems excel at processing jewelry-specific materials including PCD (Polycrystalline Diamond), CVD (Chemical Vapor Deposition) diamond, and natural or lab-grown diamonds with unprecedented precision.
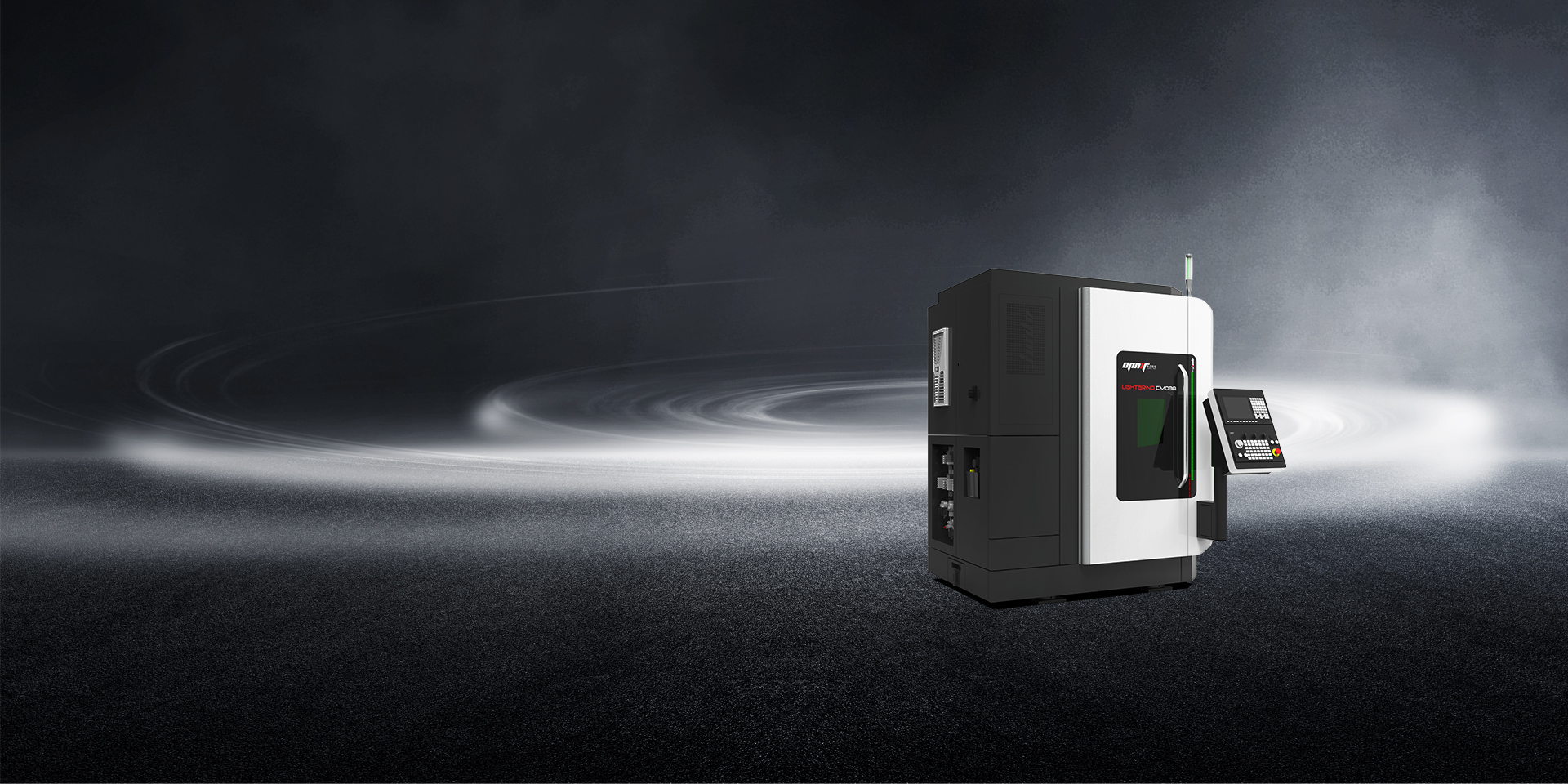
The DiaCUT L315V CVD Laser Diamond Surface Grinding Machine is specifically engineered for diamond applications, featuring precision line parallelism accuracy detection and laser interferometer calibration capabilities essential for high-end jewelry production. For jewelry manufacturers requiring intricate detailing, the LP550V Five-axis Ultrafast Laser Rotary Cutting Machine offers specialized optical modules with entrance pupil diameter of 4.5 mm and drilling capabilities ranging from 0.1-1 mm with exceptional precision.
What truly sets OPMT’s systems apart is their sophisticated software solutions that enable complex design realization:
- User-friendly GTR cutting tools software provides an easy transition from EDM to laser machining
- Advanced 3D machining path planning CAM software offers:
- Seamless importing of existing EDM projects
- Automatic 3D measurement of diamond surfaces
- Automatic program generation with 3D simulation
- Parameterized capabilities for both rotary and fixed tools
The integration of RTCP (Rotation Tool Center Point) 5-axis linkage technology allows these machines to maintain precise tool positioning relative to workpieces while executing complex multi-axis movements – essential for creating the intricate facets that define high-quality diamond jewelry.
Implementation Considerations for Jewelry Manufacturers
When integrating advanced laser systems into existing jewelry production workflows, manufacturers must carefully evaluate facility requirements, training needs, and process integration. OPMT’s Light 5X 40V requires floor space of approximately 1700×1900 mm with height clearance of 2600 mm and weighs 3500 kg, while the larger Light 5X 60V requires 2300×1800 mm with the same height and weighs 4500 kg. Both systems require industrial power supply (AC380V±10%, 23 KVA) and compressed air supply (0.7 MPa pressure, 500 L/min flow rate).
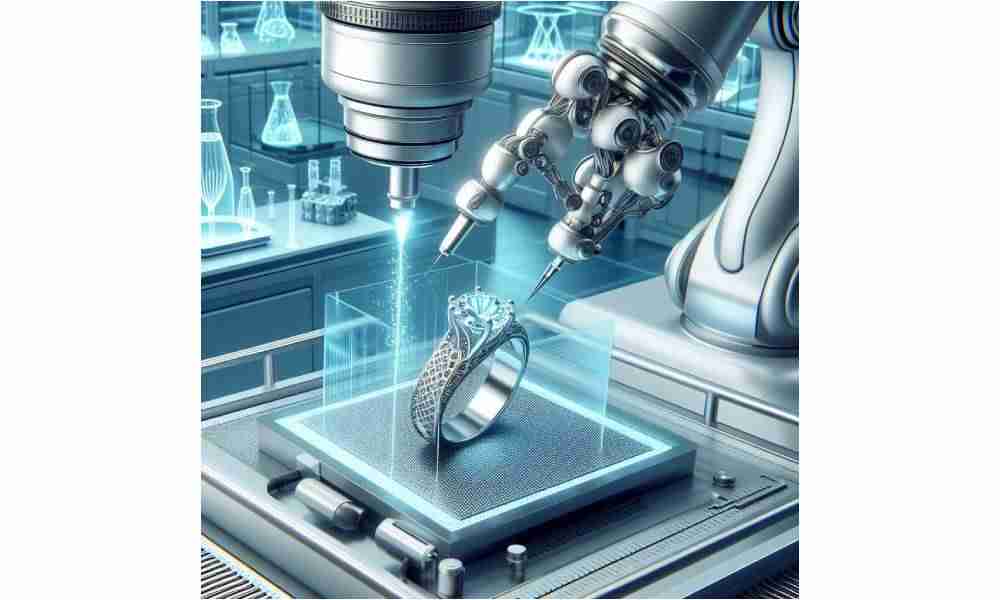
How quickly can staff adapt to these new systems? OPMT addresses this concern through comprehensive training programs, providing free one-week training in inspection, operation, and programming directly at the customer site. The company provides complete training materials at no additional cost, and the systems are designed to minimize learning curves – particularly for operations transitioning from EDM to laser technology. The user-friendly GTR cutting tools software specifically facilitates this transition with minimal retraining required.
Integration with existing production workflows is streamlined through OPMT’s software solutions, which support:
- Industry-standard programming solutions
- Importing tool geometry as DFX files
- Both manual and automated processes
- Flexibility to handle new designs and existing patterns
OPMT’s service approach ensures smooth implementation with comprehensive pre-sale support including trial production, process planning, and fixture design. After-sale support includes responsive service within 24-48 hours depending on location, minimizing potential production disruptions. This holistic approach to implementation helps jewelry manufacturers successfully adopt advanced laser technology while maximizing return on investment.
Success Metrics: Quality, Efficiency, and Design Freedom
The adoption of OPMT Laser’s advanced systems delivers measurable improvements across critical performance indicators for jewelry manufacturers. In terms of surface quality and finish, these systems achieve exceptional metrics including edge passivation capabilities of 0.004-0.005 mm, surface roughness less than 0.1 μm for diamond materials, and contour accuracy smaller than 10 μm. This level of precision ensures flawless jewelry pieces that meet the exacting standards of luxury consumers.
When comparing production efficiency with traditional methods, the advantages are compelling:
Performance Metric | Traditional EDM | OPMT Laser Systems | Improvement |
---|---|---|---|
Processing Speed | 1 mm/min | Up to 3.0 mm/min | 3× faster |
Production Cost | Baseline | 50% reduction | Half the cost |
Diamond Processing | Baseline | 20× more efficient | 20× improvement |
Floor Space Required | 10 m² | 6 m² | 40% reduction |
Electricity Consumption | 4.5 kWh/hour | 2.5 kWh/hour | 44% reduction |
Monthly Operating Cost | 4,190 Yuan | 1,956 Yuan | 53% reduction |
Perhaps most significantly, OPMT’s laser technology enables design possibilities previously unattainable with traditional methods. The Light 5X 40V and Light 5X 60V systems unlock the ability to create complex three-dimensional contours, high-precision microstructures, and edge serration with 500X magnification at 0.002 mm precision. Additionally, these systems can process non-conductive materials that traditional methods cannot handle, opening new creative possibilities for jewelry designers.
Beyond production advantages, OPMT’s laser solutions offer significant environmental benefits, eliminating the need for cutting fluids and reducing energy consumption by 25%. For jewelry manufacturers focused on sustainable production methods, this represents a compelling advantage that aligns with increasing consumer interest in environmentally responsible luxury goods. The elimination of consumables further reduces environmental impact while simultaneously lowering operating costs.
Advanced Technology Applications in Diamond Jewelry Manufacturing
OPMT Laser’s technology is particularly well-suited for complex diamond processing applications in jewelry manufacturing. The company’s femtosecond laser capabilities available on the Micro3D L530V achieve remarkable 0.08μm surface roughness on precision components – a tenfold improvement over conventional methods. This “cold processing” approach is especially valuable for diamonds, where minimizing thermal damage is essential for preserving optical and structural properties.
The integration of artificial intelligence into OPMT’s systems is transforming production capabilities for custom jewelry designs. The 2025 innovation in OPMT’s Light 5X 40V incorporates AI-error correction that reduces scrap rates to less than 1% – a dramatic improvement over traditional manual calibration errors that typically cause 8–12% scrap rates in conventional diamond processing. This translates to a 95% first-pass success rate, critical for maximizing yield when working with valuable diamond materials.
For jewelry manufacturers requiring particularly intricate detailing, OPMT offers high-precision microstructure processing capabilities that enable:
- Creation of intricate filigree work with micro-scale precision
- Development of complex textures for unique visual and tactile effects
- Production of fully articulated chain links with reduced assembly time
These advanced capabilities allow jewelry designers to push the boundaries of what’s possible in luxury diamond jewelry, creating distinctive pieces that stand out in an increasingly competitive market. By combining multiple laser technologies (nanosecond, picosecond, and femtosecond) in versatile systems, OPMT enables manufacturers to optimize their approach based on specific requirements for each jewelry component.
Conclusion
The integration of OPMT Laser’s advanced cutting technology offers jewelry manufacturers unprecedented opportunities to elevate their diamond processing capabilities. These multi-axis systems deliver superior results in precision, efficiency, and design flexibility – critical advantages in today’s competitive luxury jewelry market.
As consumer expectations for intricate, high-quality pieces continue to rise, manufacturers equipped with OPMT’s laser technology gain the ability to create previously impossible designs while simultaneously reducing production costs and environmental impact. For jewelry makers seeking a competitive edge, investing in advanced laser cutting systems represents not just a production upgrade but a strategic advancement that opens new design possibilities and market opportunities.
Disclaimer
This content is compiled by OPMT Laser based on publicly available information for reference only; mentions of third-party brands and products are for objective comparison and do not imply any commercial association or endorsement.