Computer Numerical Control (CNC) machining has revolutionized manufacturing, offering precision and cost-effectiveness for creating high-quality parts. As we approach 2025, the choice between 3-axis and 5-axis CNC machines becomes increasingly crucial for manufacturers seeking to optimize their production processes.
What is 3-Axis CNC Machining?
3-axis CNC machining is a computer-controlled manufacturing process that uses cutting tools to shape materials along three axes: X (left-right), Y (front-back), and Z (up-down). This versatile method is widely used in industries like aerospace, automotive, and mold-making for creating precise parts and components.
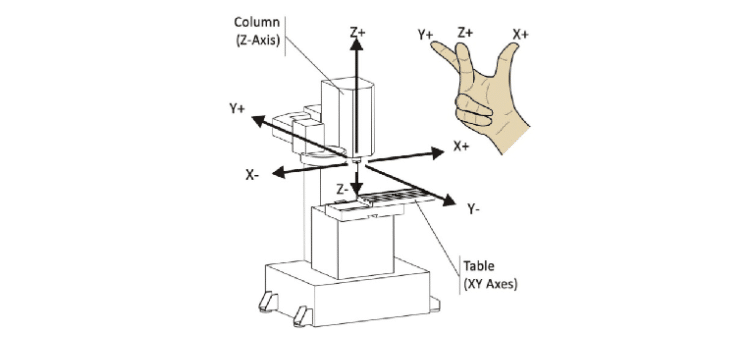
How 3-Axis CNC Machining Works
3-axis CNC machining is a precise manufacturing process that creates complex parts through computer-controlled movement along three linear axes. Here’s a concise breakdown of the process:
Digital Design Creation
- Engineers develop a 3D model using CAD software
- The design specifies exact dimensions and features
Machine Code Generation
- CAD design is translated into G-code instructions
- G-code directs the machine’s cutting paths and speeds
Workpiece and Tool Setup
- Raw material is securely mounted on the machine bed
- Appropriate cutting tools are loaded and calibrated
Automated Material Removal
- Computer guides the cutting tool along X, Y, and Z axes
- Material is precisely removed to match the digital design
Quality Inspection
- Finished part undergoes dimensional verification
- Surface finish and tolerances are carefully checked
The CNC machine’s cutting tool moves relative to the stationary workpiece, removing material with high accuracy. This computer-guided process ensures exceptional precision and repeatability, making it ideal for producing intricate components across various industries.
Advantages of 3-Axis CNC Machining
Precision and Efficiency
3-axis CNC machining delivers exceptional accuracy in part production. The automated process significantly reduces manual labor, minimizing errors and boosting productivity. This precision ensures consistent quality across multiple parts, making it ideal for industries requiring exacting standards.
Cost-Effective Manufacturing
Compared to more complex CNC systems, 3-axis machines offer a lower initial investment and reduced maintenance costs. This makes them an economical choice for small to medium-sized businesses, allowing for competitive pricing without compromising quality.
Versatility in Material Processing
3-axis CNC machines excel in working with a wide range of materials, including metals, plastics, and composites. This versatility enables manufacturers to create diverse products using a single machine, adapting to various industry needs.
Simplified Operation and Programming
The straightforward nature of 3-axis machining makes it easier to program and operate compared to more complex systems. This simplicity reduces setup time and training requirements, allowing for faster project turnaround and increased overall efficiency.
Ideal for Specific Applications
3-axis machining is particularly well-suited for creating flat or slightly curved surfaces, making it perfect for components like brackets, gears, and control panels. Industries such as aerospace, automotive, and electronics benefit from its ability to produce precise, functional parts.
By 2025, advancements in 3-axis CNC technology are expected to further enhance these advantages, with improved spindle technology and control systems leading to even higher levels of precision and efficiency.
Applications of 3-Axis CNC Machining
3-axis CNC machining is widely used across multiple industries for producing precision components. Here are the main applications:
- Automotive: Engine parts, transmission components, custom fixtures
- Aerospace: Airframe components, turbine blades, structural elements
- Medical: Surgical instruments, implants, prosthetics
- Electronics: Device casings, heat sinks, connectors
- Manufacturing: Molds, dies, jigs, and fixtures
- Prototyping: Rapid prototypes, custom parts for testing
Each industry benefits from the precision, repeatability, and efficiency of 3-axis CNC machining, enabling the production of complex parts with tight tolerances.
Industry | Common Applications | Key Benefits |
---|---|---|
Automotive | Engine blocks, cylinder heads | High precision, mass production |
Aerospace | Wing components, fuselage parts | Lightweight materials, complex geometries |
Medical | Orthopedic implants, dental devices | Biocompatible materials, customization |
Electronics | Smartphone casings, circuit boards | Fine details, high volume production |
Manufacturing | Injection molds, stamping dies | Durability, complex tooling |
Prototyping | Concept models, functional prototypes | Quick turnaround, design iteration |
Limitations and Considerations
While 3-axis CNC machining is highly versatile, it does have some limitations:
- Complex geometries: May struggle with intricate shapes or deep cavities
- Multiple setups: Some parts may require repositioning for complete machining
- Undercuts: Difficulty in creating certain undercut features without specialized tooling
For parts requiring more complex machining, 4-axis or 5-axis CNC machines may be necessary.
Optimizing 3-Axis CNC Machining
To maximize the efficiency and quality of 3-axis CNC machining:
- Tool selection: Choose appropriate cutting tools for the material and desired finish
- Cutting parameters: Optimize speeds and feeds for optimal material removal rates
- Toolpath strategies: Employ advanced toolpath algorithms for efficient machining
- Fixturing: Use proper workholding techniques to minimize vibration and ensure accuracy
- CAM software: Utilize advanced computer-aided manufacturing software for optimized toolpaths
By implementing these strategies, manufacturers can achieve higher productivity, improved part quality, and reduced machining costs.
What is 5-Axis CNC Machining?
5-axis CNC machining is an advanced manufacturing technique that utilizes a cutting tool moving in five directions:
- Three linear axes: X, Y, and Z
- Two rotational axes: A and B (or A and C)
This method allows operators to approach a workpiece from multiple angles in a single setup, eliminating the need for manual repositioning.
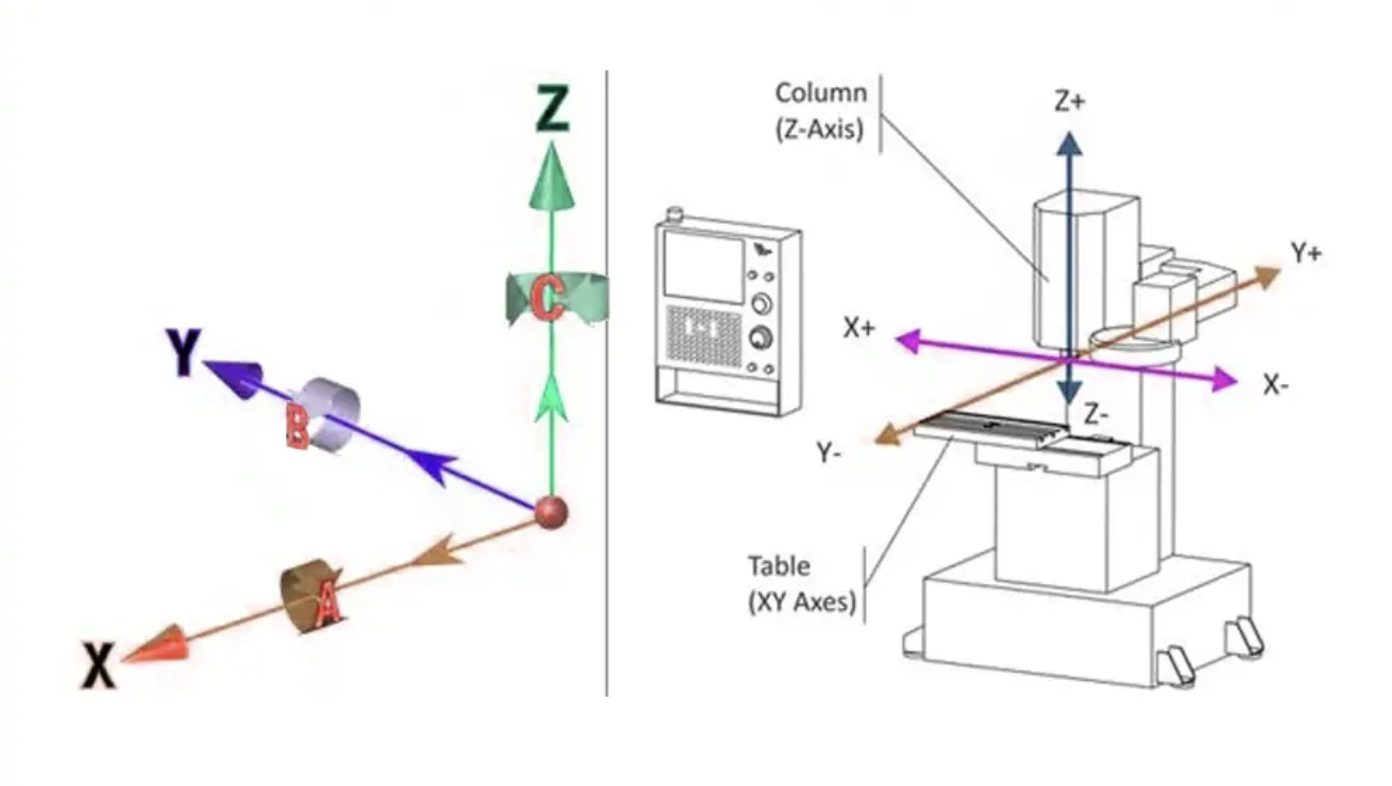
Key Benefits of 5-Axis Machining
5-axis CNC machining offers several advantages over traditional 3-axis methods:
- Improved efficiency: Reduces setup time and increases productivity
- Enhanced precision: Achieves tighter tolerances, typically within ±0.005 mm
- Complex geometries: Enables creation of intricate parts with organic surfaces
- Better surface finish: Produces smoother transitions and higher-quality finishes
- Versatility: Handles a wide range of materials, including metals, plastics, and composites
Types of 5-Axis CNC Machines

Continuous 5-Axis Machining
In continuous 5-axis machining, the cutting tool and workpiece move simultaneously along all five axes. This approach:
- Allows for seamless creation of complex, organic shapes
- Improves surface finish quality
- Reduces cycle times for intricate parts
3+2 Axis Machining
Also known as indexed 5-axis machining, this method:
- Keeps the part fixed in a specific orientation
- Uses shorter, more rigid cutting tools
- Offers better dimensional stability
- Is ideal for less complex geometries and cost-sensitive applications
Industries Leveraging 5-Axis Machining
5-axis CNC machining is crucial in several high-precision industries:
- Aerospace: For complex turbine blades and structural components
- Automotive: To produce engine parts and custom vehicle components
- Medical: For manufacturing intricate implants and surgical instruments
- Oil and gas: To create specialized drilling equipment
Optimizing 5-Axis Machining Processes
To maximize the benefits of 5-axis machining:
- Invest in advanced CAD/CAM software for efficient toolpath generation
- Train operators in 5-axis programming and operation techniques
- Regularly maintain and calibrate machines to ensure precision
- Utilize simulation software to verify toolpaths before actual machining
- Implement proper fixturing and workholding strategies for complex parts
By leveraging these advanced capabilities, manufacturers can stay competitive in industries demanding high-precision, complex parts with shorter lead times.
3-Axis vs. 5-Axis CNC Machining: Key Differences and Applications
CNC machining has revolutionized manufacturing, offering precision and efficiency across industries. But how do 3-axis and 5-axis CNC machines compare? Let’s explore their unique capabilities and ideal use cases.
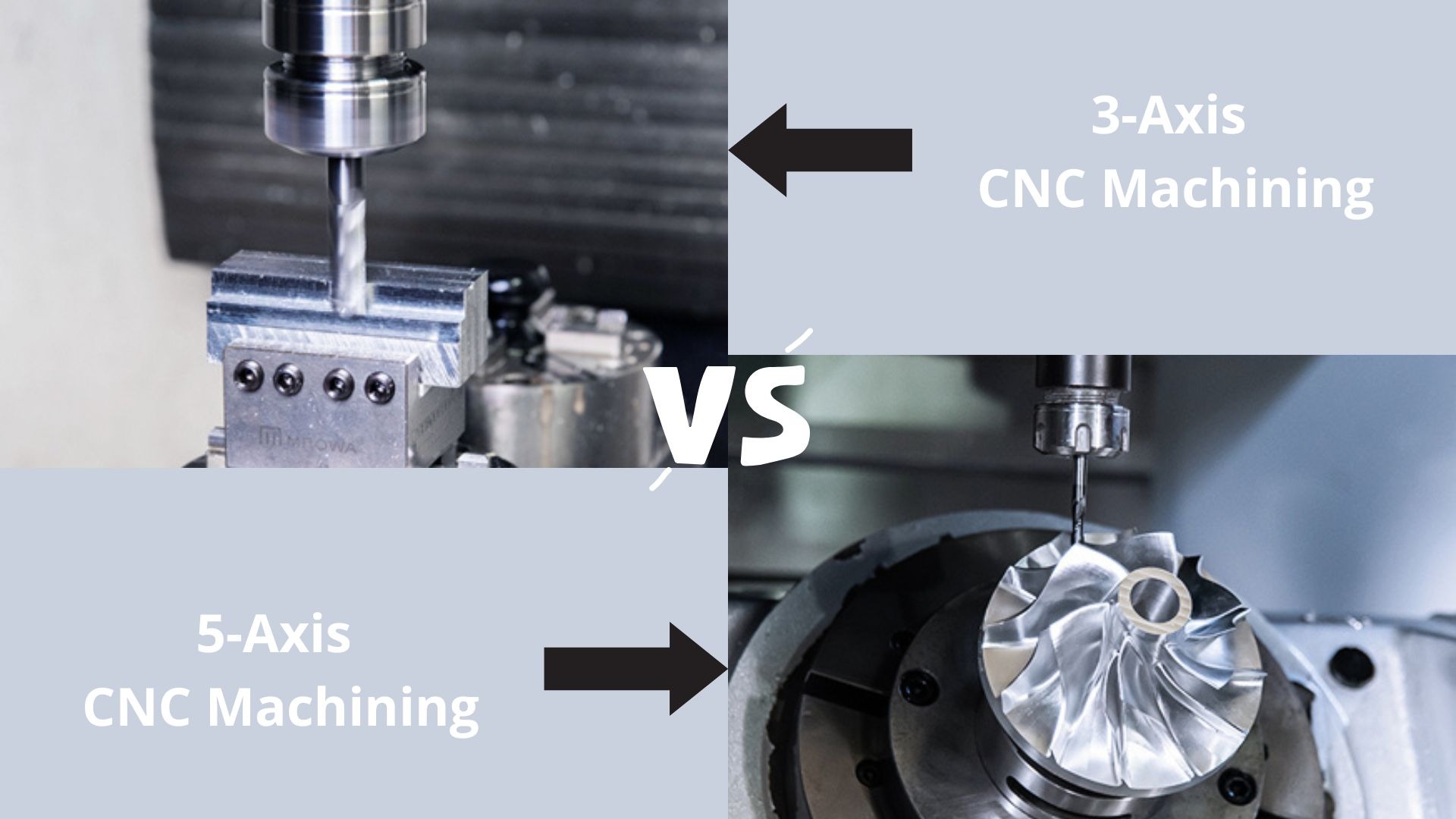
Understanding Axis Movement
3-axis CNC machines operate along the X, Y, and Z axes, allowing for linear movement in three directions. This configuration is well-suited for creating parts with flat surfaces and simple geometries. In contrast, 5-axis machines add two rotational axes (A and B) to the mix, enabling the cutting tool to approach the workpiece from multiple angles.
Efficiency and Complexity
While 3-axis machines excel at simpler cuts, 5-axis CNC machining offers superior efficiency for complex parts. How does this translate to real-world applications? Consider aerospace components:
- 3-axis machining: Suitable for flat panels or simple brackets
- 5-axis machining: Ideal for turbine blades or intricate engine parts
5-axis machines can complete intricate parts in a single setup, reducing production time and improving accuracy.
Cost Considerations
Budget-conscious manufacturers often lean towards 3-axis machines due to their lower initial investment and operational costs. However, for businesses regularly producing complex parts, the increased efficiency of 5-axis machining can offset the higher upfront costs over time.
Factor | 3-Axis | 5-Axis |
---|---|---|
Initial Cost | $25,000 – $50,000 | $80,000 – $500,000+ |
Operational Complexity | Lower | Higher |
Part Complexity | Simple to Moderate | Complex |
Setup Time | Longer for complex parts | Shorter overall |
Precision and Surface Finish
Both 3-axis and 5-axis machines can achieve high precision, but 5-axis machines often excel in creating smooth surface finishes on complex geometries. This is particularly valuable in industries like medical device manufacturing, where implants require exceptional surface quality.
Industry Applications
Which industries benefit most from each type of CNC machine?
- 3-axis machining: Automotive (simple components), electronics (housings), general manufacturing
- 5-axis machining: Aerospace, medical devices, high-end automotive, tool and die making
The choice between 3-axis and 5-axis CNC machining ultimately depends on the complexity of parts, production volume, and budget constraints.
Future Trends in CNC Machining
As we look towards 2025, the CNC machining landscape continues to evolve. Key trends include:
- AI integration: Optimizing tool paths and predicting maintenance needs
- Hybrid machining: Combining additive and subtractive processes
- Sustainability: Focus on energy efficiency and waste reduction
- Advanced automation: Increased use of robotics in material handling
These advancements are making both 3-axis and 5-axis CNC machining more efficient and accessible to a wider range of manufacturers.
Conclusion
Still unsure about choosing between a 5-axis and 3-axis CNC machine for your 2025 projects? OPMT Laser’s expert team can guide you through your CNC machining options, ensuring you select the ideal process for your specific needs. As a leading CNC machining partner, OPMT Laser offers cutting-edge capabilities with advanced router-, lathe-, drill-, and mill-based equipment. Contact OPMT Laser today to elevate your manufacturing precision and efficiency.
Disclaimer
This content is compiled by OPMT Laser based on publicly available information for reference only; mentions of third-party brands and products are for objective comparison and do not imply any commercial association or endorsement.